Polyolefin Tank Truck Gangway Installation
Categories: Gangways G4/GX Gangway SafeRack Facility
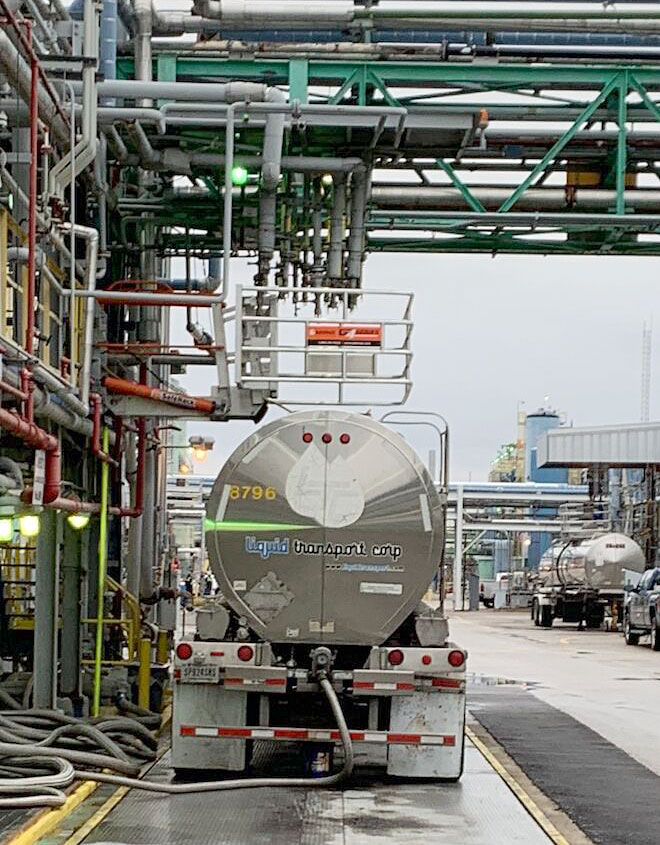
Recent Polyolefin tank truck installation at a specialty chemical company. SafeRack designed and engineered (6) six access solutions at this facility that required either wide gangways and/or modified safety cages to work with customers existing process pipes.
Polyolefin is a type of polymer composed of alkenes. These polymers are used in various industries and have many applications. One of the most common uses for polyolefin is in producing plastic bags and packaging. This material is also used to manufacture pipes and tubing and construct some automotive parts. Polyolefin is an extremely versatile material that manufacturers can customize this polymer to meet their needs in a variety of industries via bulk chemical transport. As a result, this type of polymer is an essential component of plastics like HDPE, LDPE, polypropylene (PP), and EPDM.
Polyolefin can produce harmful smoke when roasted or fumigated and irritates the eyes and lungs. Dripping eyes, sneezing, coughing, and other symptoms are common. By going outside and getting some fresh air, workers exposed should feel better.
Shifting silos and tank trucks to the side and the possible consequences of flipping over a transport vehicle on people and equipment can be a great risk. Product lines, silo discharge lines, steam lines, pumps, and compressors might be affected. Pellets may spill on the surrounding area during the unloading process. Aside from the threat of sliding, pellets may infiltrate rainwater gullies and finally reach the coastal areas. Spilled pellets should be collected immediately, and terminal officers should safeguard drainage systems.
Each unloading situation is distinct due to local variables, such as the distance of the silo-loading pipe, the depth of the silo, the pipe’s thickness and interior hose surface, and the number of loops of unloading hoses required. Each unloading circumstance requires the workers to strike a balance between the airflow and product flow that will yield a target unloading pressure. It is a fallacy that a truck driver seeks the maximum feasible discharge pressure to complete a task as rapidly as possible. It is important to remember that the devices used to measure the air pressure on the containers are indications rather than accurately calibrated instruments. These are the important factors to consider in the bulk transfer of olefins.
The loading terminal above required six access solutions, and one of these is a bottom loading hose access. A bottom loading arm is a more viable option to prevent the bending of hoses, and a hose reel might be required without a loading arm to deter workers from tripping over the large hoses blocking their way.
Another factor to consider is the vapor pressure of the product being transferred. The air pressure in the container will decrease as the product is unloaded, and this can cause a vacuum effect that might make it difficult to remove all of the product from the container. To prevent this, workers can use a vapor return line to allow air to enter the container and equalize the pressure.
A loading coupler installed is also important equipment to consider. A quick-connect coupling can be used for easy disconnection in case of an emergency, while a more permanent connection might be necessary for products that cannot be allowed to spill.
The top-loading option in the terminal requires a flat ramp-style (SFR) gangway with an offset safety cage. This installation provides a safe walkway for workers to access the hatch of the container during loading and unloading. The enclosure also provides a secure access option for workers and allows them to access the hatch area safely by eliminating fall risks.
The terminal can also provide various customized options to match tank trucks and railcars. These options include a pump station, an air compressor, and a filter system—various safety features, such as emergency shutdown buttons, fire suppression systems, and spill containment systems, might also be mandated in some circumstances.
The loading terminal should be designed and managed in such a way as to provide safe conditions for working around different iso containers and tank trucks, including secure access to the top of vehicles in compliance with OSHA mandates. Working on top of a vehicle is not allowed unless proper fall protection facilities are available. The loading terminal should have a loading dock with a loading platform that is level with the trailer bed, and the trailer should be securely fastened to the loading dock. There should also be adequate personnel on hand to assist with loading and unloading operations. Once the trailer is loaded, workers should cover it with a tarp to protect the cargo from weather conditions.