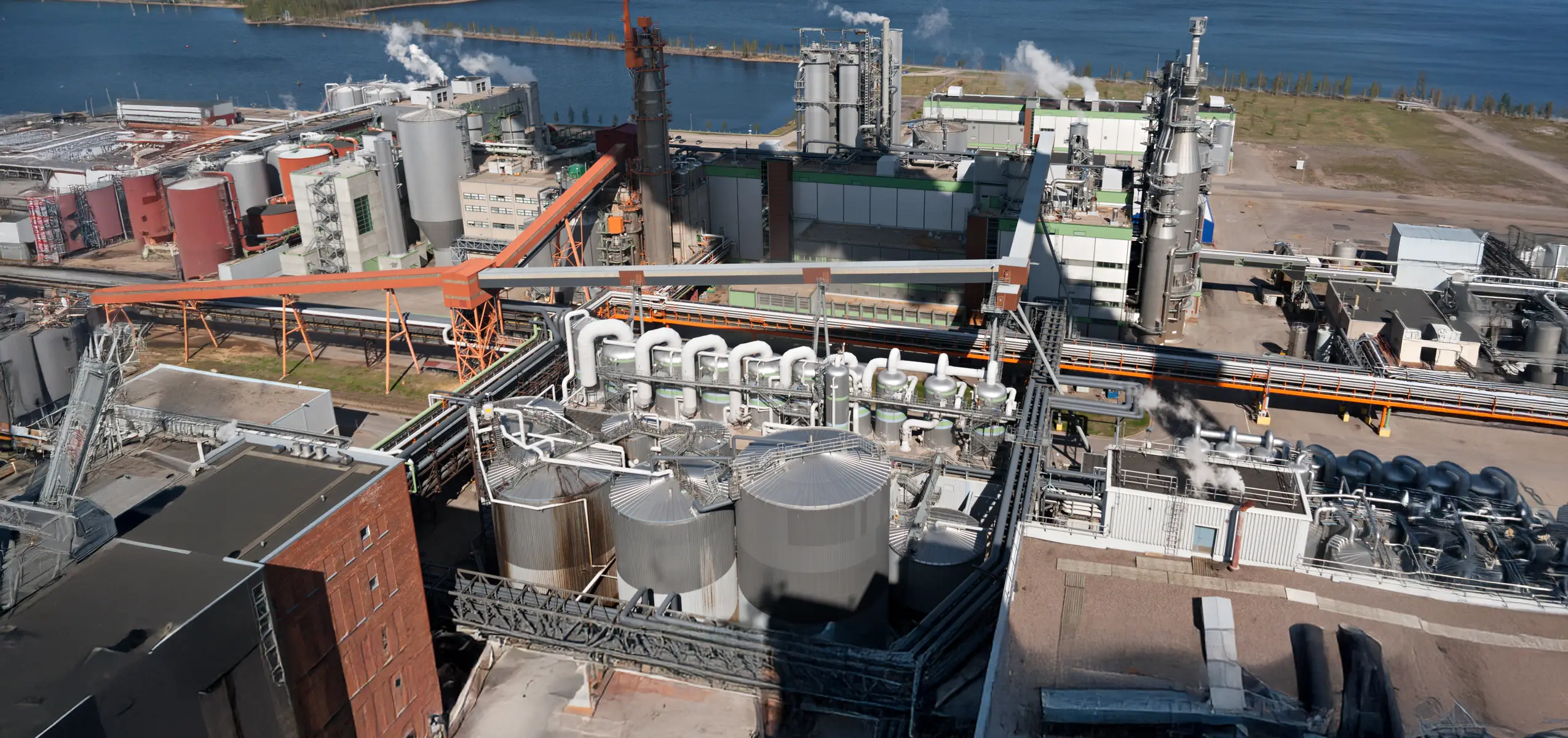
Green Liquor
Custom Loading, Spill Containment & Fall Protection Solutions
Green Liquor Handling Design, Loading & Installation for the Paper Industry
SafeRack provides specialized loading systems designed to address the specific challenges of green liquor handling. Our green liquor loading systems are tailored for both railcar and tank truck operations and include closed-loop loading arms, pressure relief components, and green liquor spill containment solutions to help maintain worker safety and environmental compliance.
These systems are frequently used in green liquor pulp and paper operations where reliability, safety, and OSHA compliance are required.
By integrating SafeRack’s green liquor safety solutions, pulp and paper facilities can significantly reduce risk during transport and transfer operations. Our green liquor railcar loading platforms, green liquor truck loading systems, and associated handling equipment help ensure the safe handling of green liquor in pulp mills while maintaining operational efficiency.
- Fall Protection – Operators working with green liquor require stable gangways and OSHA-compliant safety cages to ensure secure access during top-loading operations.
- PPE Compliance – Proper protective gear is mandatory, including chemical-resistant gloves, splash-resistant goggles, and respirators to guard against burns and inhalation risks.
- Spill Containment – SafeRack’s track pans and drainage solutions help prevent hazardous leaks and ensure compliance with safety protocols in pulp mills.
- Ventilation & Gas Detection – Due to the release of sulfur-based gases, green liquor handling equipment must be supported by continuous ventilation and toxic gas monitoring systems.
Green Liquor
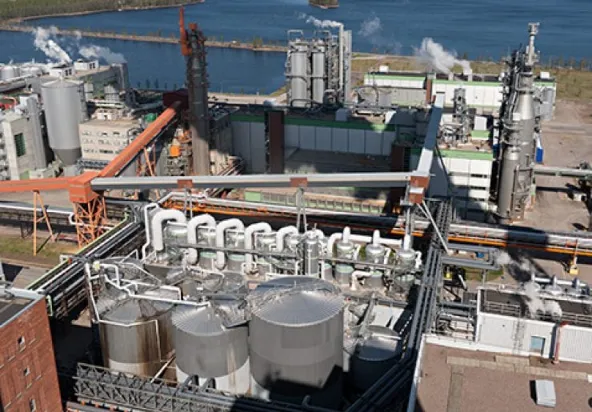
Enhancing Workplace Safety with Reliable, Compliant Access Systems
What is Green Liquor in the Pulp & Paper Industry?
Green liquor is a corrosive and caustic by-product of the Kraft pulping process, formed when smelt from the recovery boiler is dissolved in water. It plays a critical role in the chemical recovery cycle within pulp mills, acting as a precursor to white liquor. Composed mainly of sodium carbonate (Na₂CO₃) and sodium sulfide (Na₂S), green liquor owes its name and distinctive color to the presence of colloidal iron sulfide.
Understanding what green liquor is and how it functions in the paper mill process is essential for safe operations. Although it is not a final product, green liquor in paper industry workflows must be carefully managed due to its reactivity and the potential for releasing toxic sulfur gases when heated or improperly contained.
Green Liquor Loading & Unloading Procedures
Proper loading and unloading procedures are essential to the safe handling of green liquor in pulp mills. As a highly caustic chemical used in the chemical recovery cycle of the Kraft process, green liquor must be transferred using carefully engineered systems that protect workers and the environment.
Railcar Loading & Unloading
Green liquor is typically top-loaded using closed-loop systems designed to limit vapor exposure and control spills. These systems utilize 3-inch stainless steel loading arms or chemical transfer hoses equipped with vapor recovery functionality. The standard railcars used in green liquor pulp and paper operations are 26,000-gallon DOT-111 insulated or non-insulated tank cars, each featuring safety valves and either center or offset 6-by-6-foot crash box openings. They measure approximately 9 feet in outside diameter and between 45 and 50 feet in overall length.
To support safe rail operations, SafeRack provides green liquor railcar loading platforms engineered with OSHA-compliant GX Gangways and integrated safety cages. These systems are complemented by green liquor spill containment solutions, such as track pans and berms, which help prevent environmental contamination. Vapor recovery arms combined with gas detection systems are also essential for monitoring and minimizing exposure to sulfur-based emissions during transfer.
Tank Truck Loading & Unloading
When transferring green liquor via tank truck, approved DOT trailers such as MC 307 or low-pressure chemical ISO containers are used. These vehicles are typically bottom-unloaded using an extension pipe equipped with two flanged valves, which allow controlled and sealed product flow.
SafeRack supports green liquor truck loading systems with critical safety equipment, including corrosion-resistant hoses and pumps designed to withstand the chemical’s aggressive nature. Pressure relief valves are installed to prevent trailer over-pressurization, while grounding and bonding systems ensure proper static discharge control during transfers.
Whether handling bulk rail or truck operations, SafeRack’s green liquor handling equipment and safety systems are engineered to meet the strict demands of modern pulp and paper facilities—improving safety, reducing exposure, and supporting long-term operational reliability.
Products
Semi Trailer & Truck Steps
Semi-truck steps for loading semi and flatbed trailers
Break Away Smart-Hose Safety System
Smart-Hose™ Break-Away Safety System (LL3-B) can help protect your facility from the potentially devastating consequences associated with pull-away incidents.
Samplers and Oil Thieves
Crude oil samplers, including oil thieves and sample catchers.
Hose and Electric Reels
Our hose and electric reels selection help keep your hose neatly wrapped away when not in use. The hose reels come with ready-to-mount brackets for easy installation.
Gate Openers and Hopper Car Shakers
The PCS-3 Hopper Car and Hopper Trailer Shakers can be modified to comply with force and design requirements set for the ACF “center-flow” hopper car, Contact us for details.
Guardrail Systems
Guardrail Systems from SafeRack, the leader in fall protection, bulk loading, and truck, railcar, and vehicle access.
Bollards and Bumper Posts
The Bollards and Bumper Posts provide durable protection, custom sizes, and easy-to-install covers for enhanced facility safety.
Loading Dock Stairs
Prefabricated IBC, ADA, or OSHA Aluminum Loading Dock Steps that bolt together in about an hour.
Signs and Signals
Signs and Signals
Drench Showers
Emergency Drench Showers and Safety Eyewash Stations
Pipe Racks
Prefabricated Pipe Racks Constructed Faster and Easier Than Ever Before
Tools and Loading Accessories
A comprehensive range of facility and loading terminal equipment, accessories and safety solutions.
Grounding & Monitoring
Protect personnel, product, and terminals with static grounding (earthing) solutions
Safety Gates
Industrial safety swing gates, facility guardrails, mezzanine gates and barriers gates.
Spill Containment
SPCC and EPA compliant solutions. Railcar track pans, truck spill containment, drum and IBC spill pallets, and industrial containment berms.
Top Loading Arms
Top Loading Arms
Loading Arms & Couplings
Truck, rail, and marine bulk fluid transfer top/bottom loading arms, couplings, swivel joints, hoses, and breakaways.
Portable Access Platforms
SafeRack’s MAUI mobile access units provide secure, adjustable stair solutions for safely accessing elevated truck and railcar work areas, even in the most challenging environments.
MaxRack Elevated Platforms
Powered elevating platform system for accessing railcars and trucks
Gangways
Truck, Railcar and Marine Gangways, Safety Cages, and Inspection Services
Stairs & Work Platforms
Fixed and Mobile Access Stairs, Work Platforms, Crossover Stairs, Rolling Stairs & Mobile Platforms, Roof Stairs and Access, Ship Ladder
Green Liquor Solutions
Best Practices for Safe Handling of Green Liquor in Pulp Mills
Handling green liquor, a corrosive by-product of the Kraft process, requires strict adherence to safety protocols to protect personnel and equipment in paper mill environments. Only trained and qualified personnel should be permitted to manage or transfer green liquor, due to its chemical hazards and potential to release toxic sulfur gases.
Personal Protective Equipment (PPE)
Operators must be equipped with chemical-resistant clothing, splash-resistant goggles, respirators, and gloves. Proper PPE use helps prevent skin and eye injuries as well as respiratory complications caused by vapors or accidental splashes.
Ventilation and Gas Monitoring
Green liquor may emit hydrogen sulfide and other sulfur compounds during transfer or when heated. Effective ventilation systems and gas detection monitors must be installed and operational to ensure that any buildup of toxic gases is quickly identified and addressed.
Corrosion Prevention and Equipment Maintenance
Because green liquor is highly caustic, storage tanks, pipelines, loading arms, and transfer components must be made of corrosion-resistant materials and inspected routinely for signs of degradation. This proactive maintenance reduces the risk of leaks, spills, or equipment failure.
Emergency Response Protocols
In the event of exposure:
- Move the affected individual to fresh air immediately.
- Remove contaminated clothing and thoroughly wash the skin with soap and water.
- If eye contact occurs, flush with water for a minimum of 15 minutes.
- If green liquor is ingested, do not induce vomiting. Call poison control or seek emergency medical care immediately.
- If aspirated into the lungs, green liquor can cause chemical pneumonitis—a potentially fatal condition requiring immediate medical intervention.
Critical Safety Warnings
- DOT-Regulated: Green liquor is classified as Hazardous Caustic Alkali Liquid, UN 1719.
- Avoid contact with acids: Reactions may release toxic gases such as hydrogen sulfide.
- Ensure proper ventilation: Exposure to sulfur gases can cause serious respiratory distress.
- Use corrosion-resistant equipment: Prevents failures that could result in environmental contamination and safety violations.
By following these best practices, pulp and paper mills can ensure the safe handling of green liquor and reduce the risk of accidents, exposure, or environmental damage.
Green Liquor Handling Solutions
The following examples showcase potential loading and unloading solutions for green liquor handling. Recognizing that each facility has distinct requirements, our team of experts collaborates closely with you to develop a customized system that ensures safety, efficiency, and compliance with industry standards.
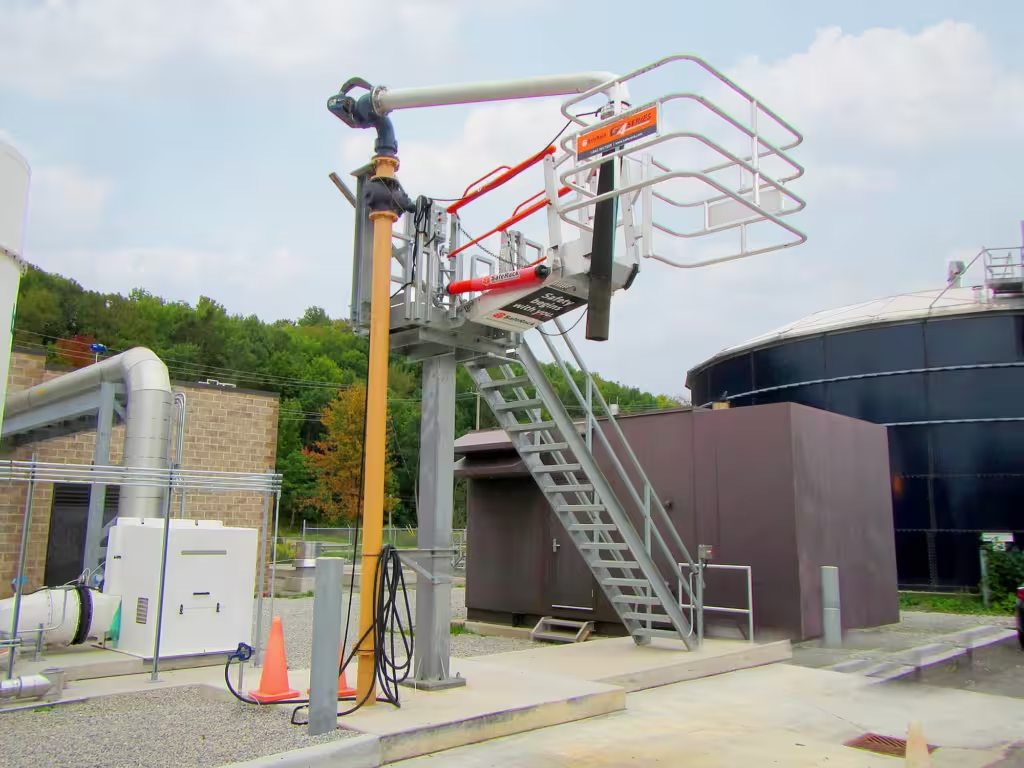
Loading Gangways
A wider access gangway (48″-60″ is preferable) as it helps improve access and egress to and from the vessel. In addition, a wider gangway will reduce the risk of the operator’s PPE getting caught, torn, or damaged, and will improve productivity and safety. Powered gangway solutions are also an option, with both hydraulic and pneumatic solutions being commonly used.
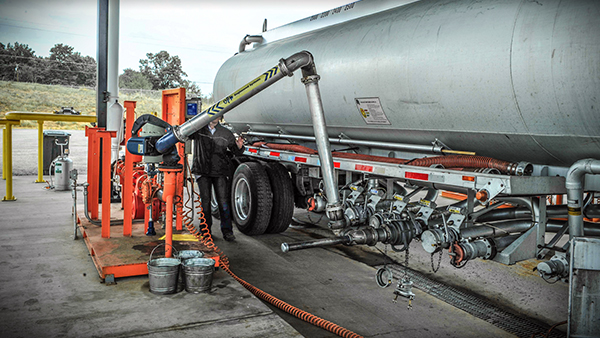
Loading Arms
In paper mills, Tall Oil Fatty Acid (TOFA), Black Liquor, White Liquor, and Green Liquor (Spent Pulping Liquor) are typically loaded into railcars or tank trucks via boom-supported stainless steel loading arms or chemical hoses with a flange connection. The arm or hose will have a top inlet with a control valve to ensure that it is self-draining after use and is supported along the length of a mechanical loading arm to improve handling, known as a by-pass arm. You can install one liquid and one vapor arm, or mount both the liquid and vapor hoses on one by-pass arm.
For unloading, typically you would use a rigid stainless steel self-draining loading arm with Buna-N, PTFE or Viton seals. Purge lines can be fitted to the arm, for nitrogen purging. Additional features such as parking latches with proximity sensors can be incorporated into the total system to ensure the arm is correctly stowed when not in use before any rail movement can occur.
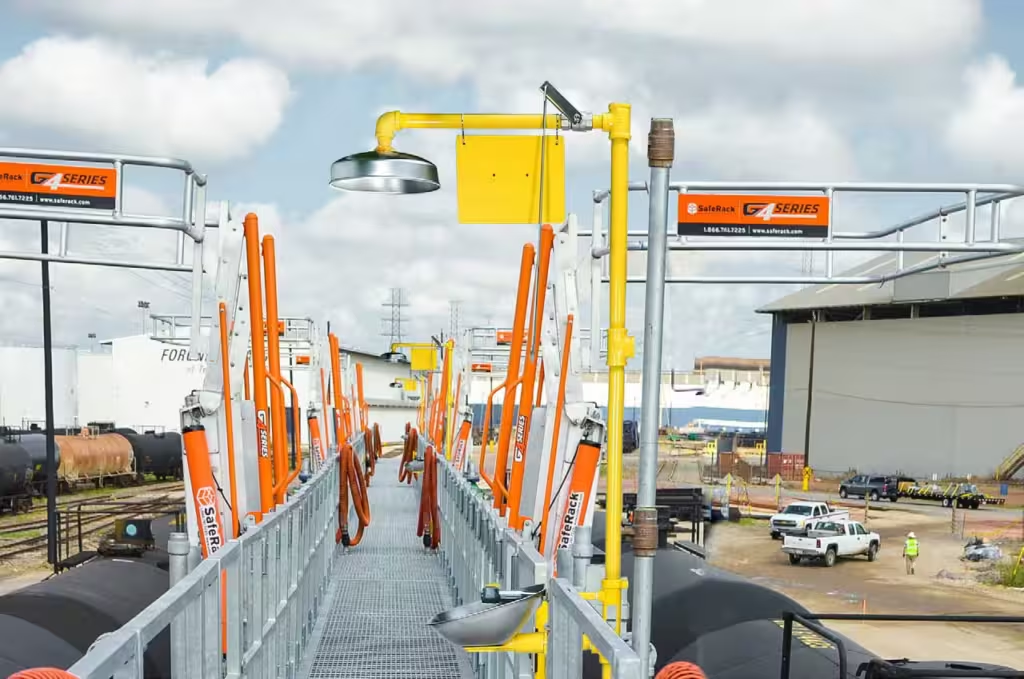
Eye Wash/Drench Showers
Spill containment pans will be provided at the point of loading operations and are an essential piece of equipment in overall site safety and environmental protection
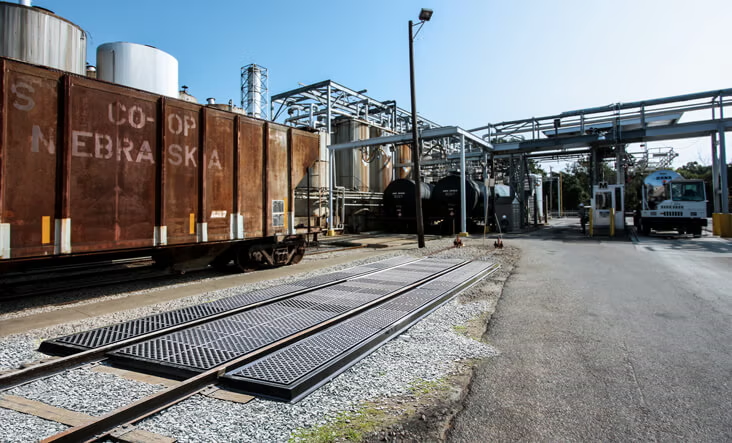
Spill Containment
Spill containment pans will be provided at the point of loading operations and are an essential piece of equipment in overall site safety and environmental protection.
Wheel chocks allow for safe access to and storage of treatment chemicals, while spill containment pans utilized at the point of loading operations serve as essential safety and environmental protection tools.
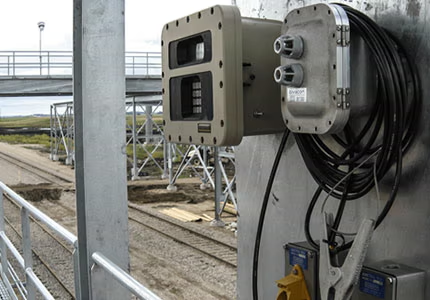
Grounding
While much of the products being transferred in the pulp and paper manufacturing aren’t combustible, it is an industry best practice to include the grounding of all vessels before starting the (un)loading process.
Ground controllers — ensure true grounding before product flow is permitted
Explosion-proof enclosures — meet or exceed UL, CSA, and Ex requirements
Non-sparking tools are also recommended while working around this product
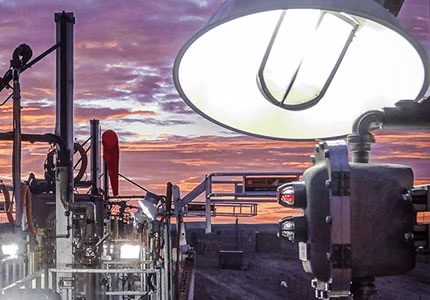
Loading Platform Options
Lighting – General exterior and task lighting to illuminate work and walk areas.
Platform & Canopies – Full platform canopies reduce exposure to the elements and improve the safe and productive loading operation from the operator’s perspective.
Operator Shelter—Depending on your site requirements, consider the requirement of an operator or guard building to keep personnel out of the elements. This can be customized to meet specific site requirements.
Wheel Chocks – SPCC options to allow for safe access and storage of water treatment chemicals.
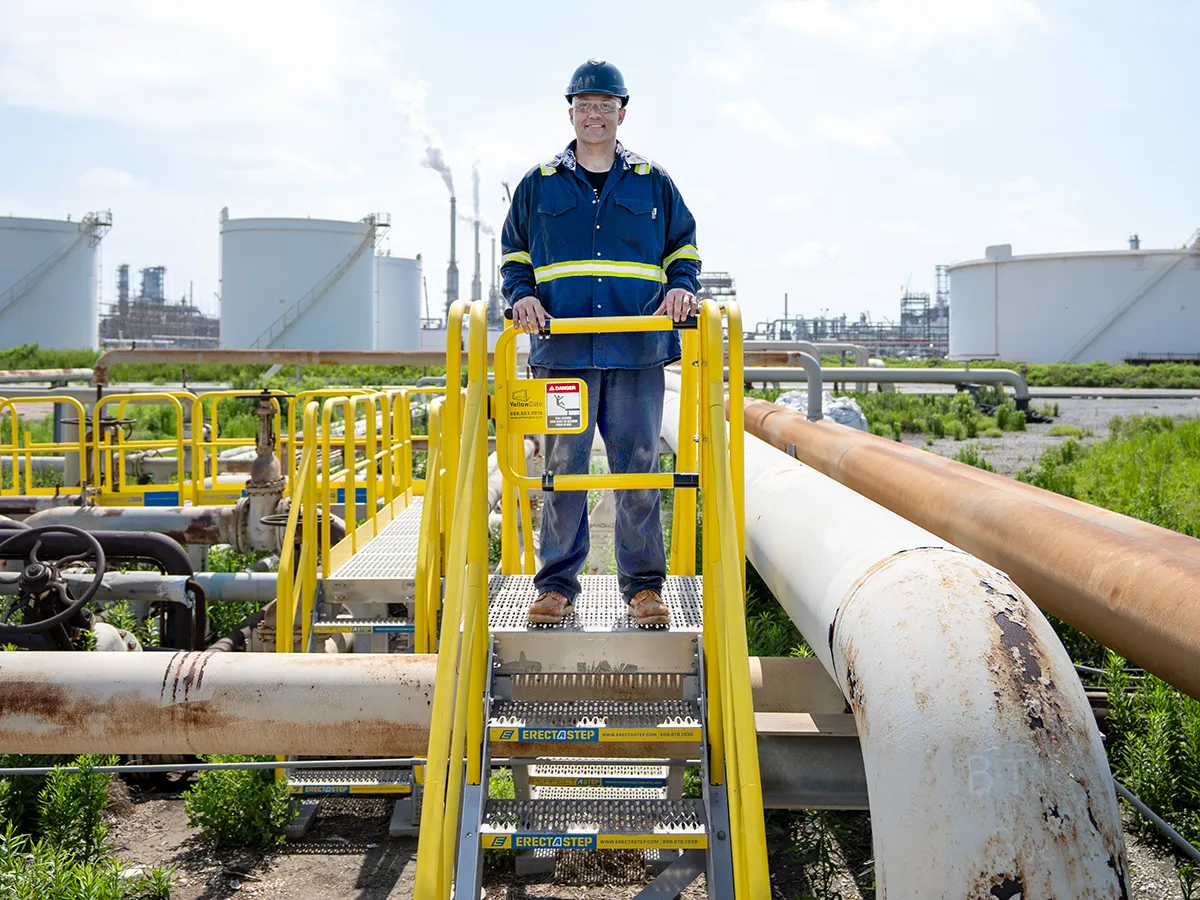
Safety Gates, Stairs, Ladders, & Platforms
Safety Gates will be installed at the top of stairs and any other openings to ensure operator safety.
SafeRack’s line of industrial safety gates is the most flexible product on the market with the ability to span openings between 16” and 36” and is field adjustable with nothing more than a wrench. We also have guardrails, metal handrails, and full-fledged fall protection solutions with customizable options to fit your needs.
Frequently Asked Questions
Yes, SafeRack’s loading platforms are designed to enhance safety and efficiency in pulp and paper mills. They provide secure access for loading and unloading materials, reducing the risk of falls and improving operational productivity.
SafeRack’s gangways offer safe passage over hazardous areas such as chippers and conveyors, minimizing the risk of accidents. Their durable construction ensures long-term reliability in demanding mill environments.
Absolutely, SafeRack provides spill containment systems specifically designed to manage hazardous chemicals commonly used in pulp and paper production, ensuring environmental compliance and workplace safety.
SafeRack offers custom specialty platforms that help improve worker safety, ergonomics, and productivity when accessing elevated equipment in pulp and paper mills.
Yes, SafeRack’s safety solutions are designed to meet or exceed OSHA regulations, ensuring that pulp and paper facilities maintain compliance while protecting their workforce.
Projects
-
Secondary Spill Containment Calculator
Secondary Containment: How to Calculate Capacity for SPCC Compliance and Environmental Protection Secondary spill containment is essential in protecting the…