Hopper Car Loading
Optimizing Workplace Safety and Productivity with Loading Access Solutions
SafeRack: Full-Service Solutions for Safe & Efficient Hopper Car Loading
Hopper railcars play a crucial role in bulk material transport, featuring an open-top for loading and a sloped floor for gravity-assisted unloading. While this design optimizes bulk handling, it also presents safety risks due to the height of the railcar hopper and the need for secure worker access. Additionally, space constraints at many cement loading facilities require carefully planned solutions to ensure safe and efficient railcar loading operations.
SafeRack goes beyond supplying high-quality gangways, safety cages, and loading platforms—we partner with facilities to provide on-site safety assessments, engineering support, and seamless equipment integration. Our experts evaluate space limitations, workflow inefficiencies, and compliance requirements to design custom, OSHA-compliant solutions for hopper rail cars, enhancing both worker safety and operational throughput.
From initial consultation to installation guidance and ongoing maintenance support, SafeRack delivers a complete service solution for rail hopper car unloading systems and railcar loading operations. Whether handling covered hopper railcars, hopper railcars, or open-top hopper rail cars, our solutions ensure safe, compliant, and efficient operations.
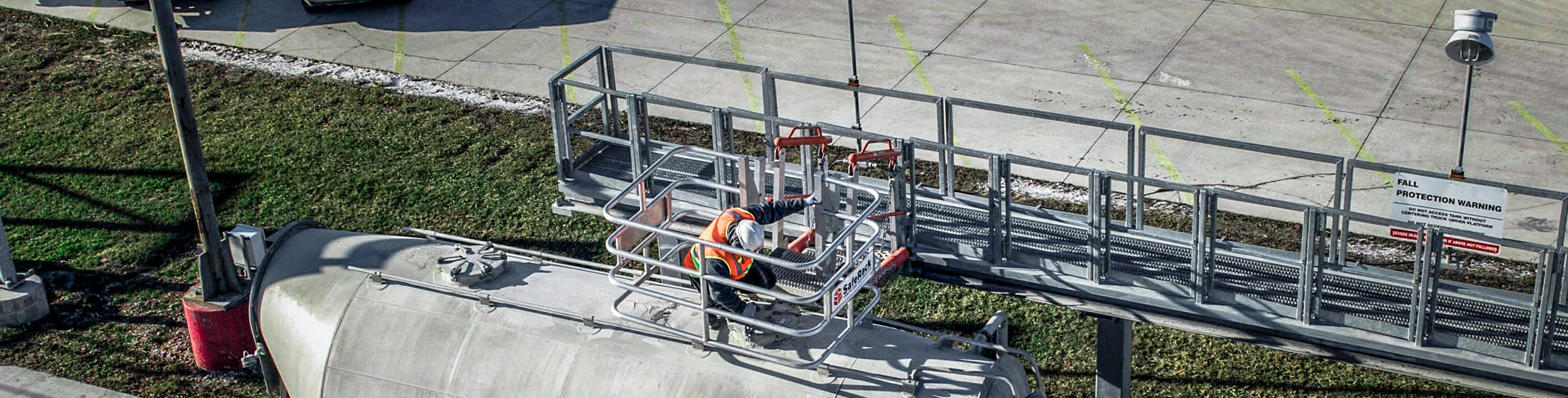
Reliable, Innovative Access Systems Designed for Safety and Efficiency
Collaborative, Customized Solutions Designed for Your Facility
Fine dust from loading spouts can accumulate on hopper railcars, creating hazardous working conditions for operators. To ensure a safe environment, fall arrest and fall prevention systems are essential, allowing workers to perform their duties quickly and securely. SafeRack’s railcar loading and unloading platforms, equipped with RetractALok gangways, provide an optimal balance of safety, ergonomics, and efficiency. These systems are designed for easy operation, requiring minimal effort to lift while maintaining rock-solid stability.
The size and design of covered hopper railcars, including multiple hatches, require unobstructed access across the top of the car. SafeRack’s gangways and platforms are engineered to provide full mobility, ensuring operators can safely reach every necessary point without restriction. Our adjustable, OSHA-compliant hopper rail car gangways offer superior flexibility and ergonomic design, improving worker safety while maximizing throughput. By integrating SafeRack’s customized solutions for rail hopper car unloading systems, facilities can streamline operations while maintaining the highest levels of safety and compliance.
Products
Loading Racks & Metering Skids
Truck & Railcar Transloading, Metering Skids and Loading Racks – From single-spot to multi-spot systems.
Truck & Railcar Gangways
The industry’s safest and most ergonomic gangway for truck and railcar access.
Barrier Gates
YellowGates XL barrier gate provides 6 feet of adjustability protects every pathway in your facility
Safety Swing Gates
YellowGate – The Original Universal Self Closing Safety Gate
Gate Openers and Hopper Car Shakers
The PCS-3 Hopper Car and Hopper Trailer Shakers can be modified to comply with force and design requirements set for the ACF “center-flow” hopper car, Contact us for details.
Loading Arms & Couplings
Truck, rail, and marine bulk fluid transfer top/bottom loading arms, couplings, swivel joints, hoses, and breakaways.
Tools and Loading Accessories
A comprehensive range of facility and loading terminal equipment, accessories and safety solutions.
Early Departure
Our safety interlock system prevents accidental drive-offs and can be designed into your pump, fall protection or any other preferred loading apparatus.
Hopper Car Loading Solutions for the Cement Industry
SafeRack provides OSHA-compliant railcar loading solutions designed to enhance safety, efficiency, and reliability for cement hopper car operations. Our full-service approach includes on-site safety assessments, expert design support, and seamless equipment integration, ensuring that facilities handling hopper railcars, covered hopper railcars, and rail hopper cars operate safely and efficiently while minimizing downtime and maximizing throughput.
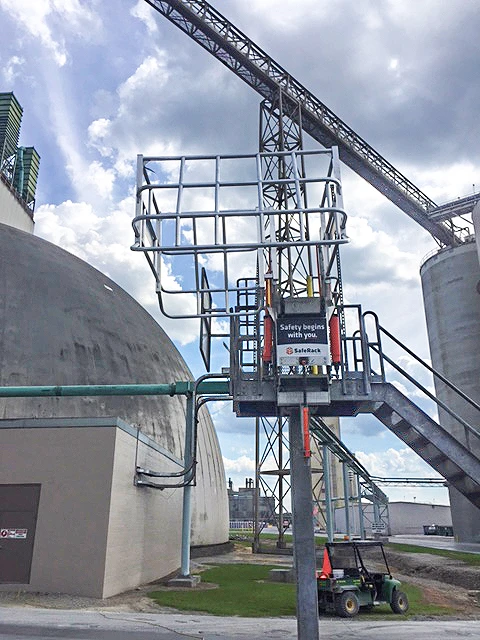
Top Hatch Access Platforms
Loading cement into hopper cars requires secure, ergonomic access to ensure safe and efficient operations. SafeRack’s top hatch access systems provide stable platforms that allow operators to work safely and productively while minimizing fall hazards.
SafeRack’s access solutions are designed to fit the unique height and configuration of hopper cars, ensuring safe and unobstructed access for loading and inspection. Our lightweight, corrosion-resistant construction ensures durability in high-dust, heavy-use environments, while our team works directly with facilities to design solutions that fit within space constraints and workflow demands.
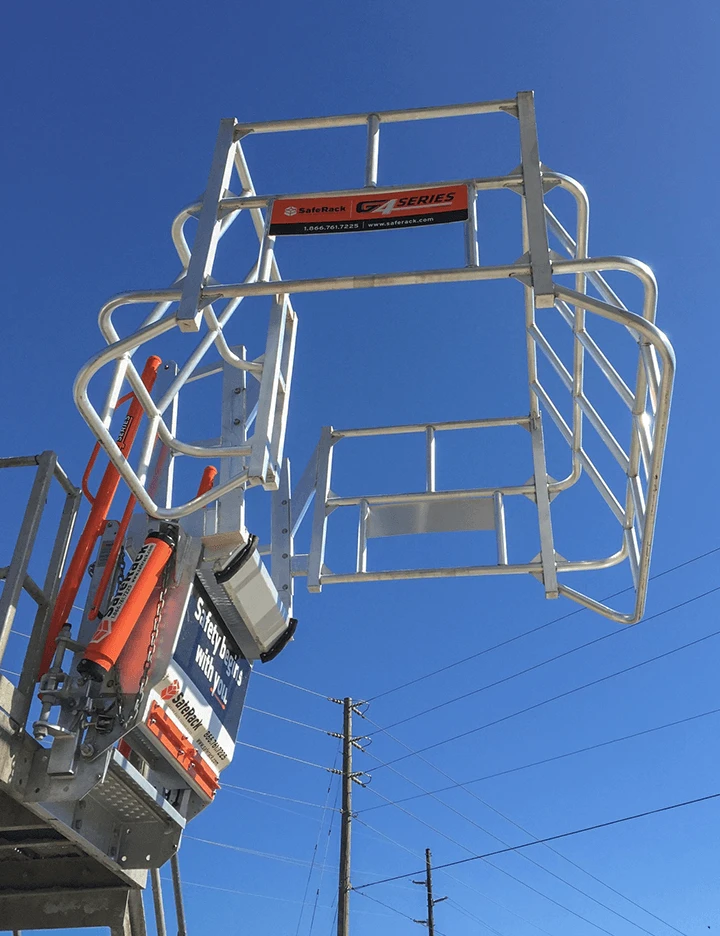
Loading Gangways with Safety Cages
SafeRack’s loading gangways and safety cages provide stable, OSHA-compliant access to hopper cars while protecting workers from fall hazards.
Our gangways are designed with full-range movement to accommodate the multiple hatches on hopper cars, ensuring operators can safely open, close, and inspect each compartment without restriction. SafeRack’s adjustable, ergonomic designs improve both worker safety and productivity, while our on-site design support ensures a customized, efficient integration into existing loading platforms.
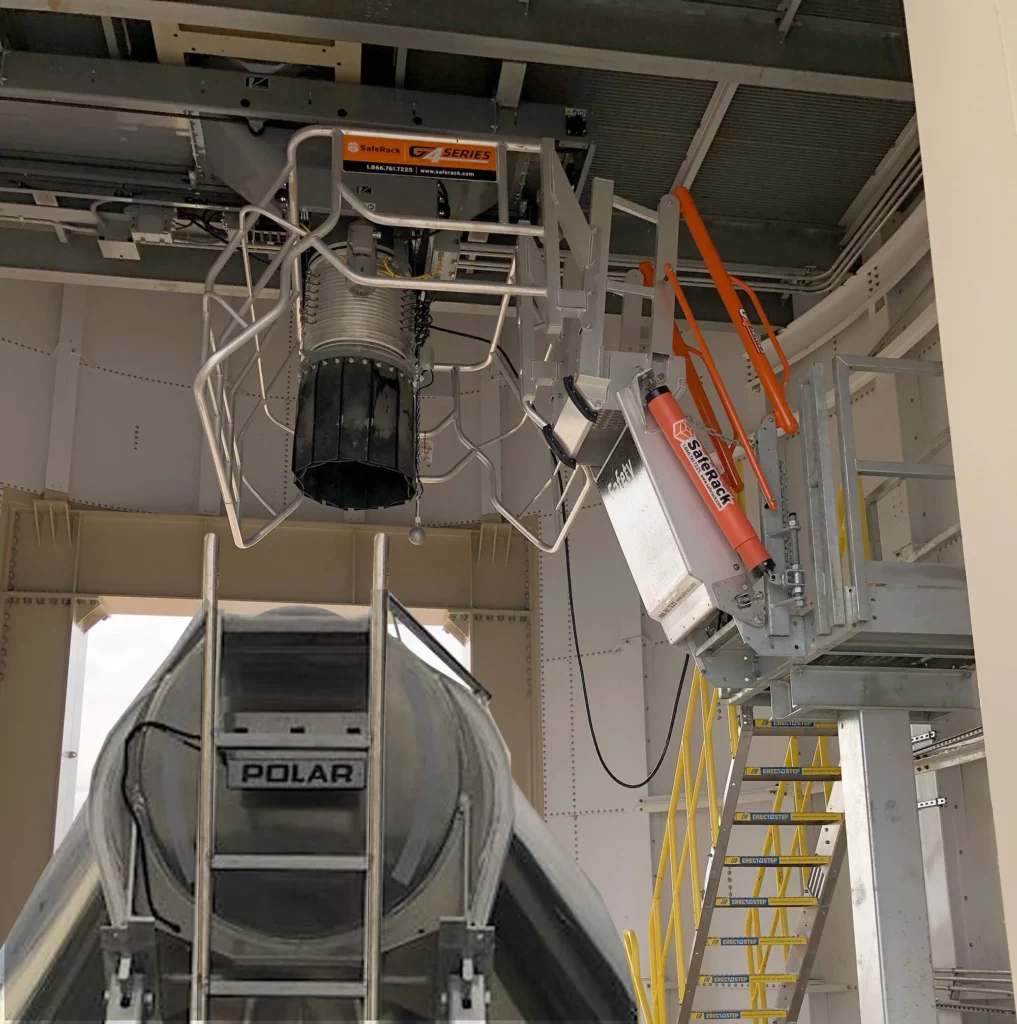
Loading Chutes
Space constraints in cement facilities often limit the placement of gangways and access systems, requiring specialized loading chute solutions. SafeRack’s loading chutes are designed to optimize space usage while maintaining safety and compliance.
Our engineering team develops solutions that minimize footprint without sacrificing safety, ensuring operators have clear access to loading points while maintaining a secure working environment. With custom configurations available, we help facilities maximize efficiency in even the most challenging layouts.
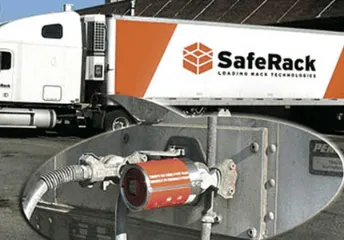
Early Departure Systems
IPreventing premature railcar departures is critical for worker safety and equipment protection. SafeRack’s early departure systems integrate with hopper car loading operations to prevent movement until loading is complete, ensuring a secure, controlled process.
By interlocking with braking systems, SafeRack’s solution reduces the risk of accidental drive-offs, protecting workers, gangways, and loading equipment. Our team provides custom integration support, ensuring the system functions seamlessly with existing operations.
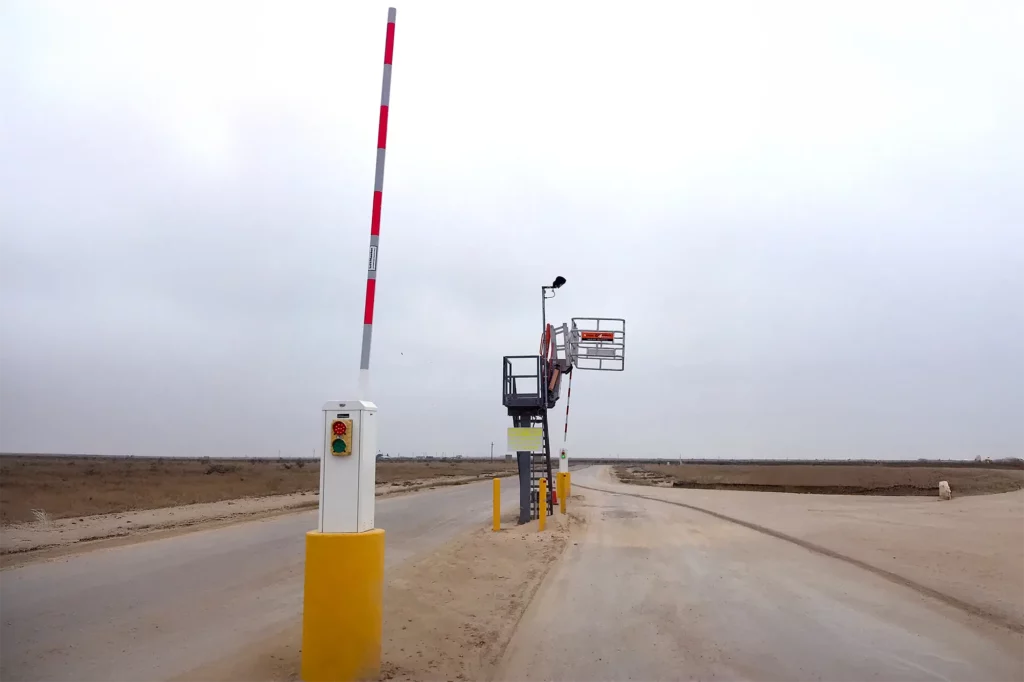
Truck Traffic Gates
Cement loading facilities require strict traffic control to prevent accidents and ensure safe loading procedures. SafeRack’s truck traffic gates provide a physical and visual barrier, ensuring proper equipment stowage before trucks or railcars depart.
These gates are synchronized with gangway and safety cage operations, preventing premature departures and improving overall site safety. Optional high-visibility LED indicators enhance driver awareness, while SafeRack’s integration support ensures a seamless installation into existing traffic management systems.
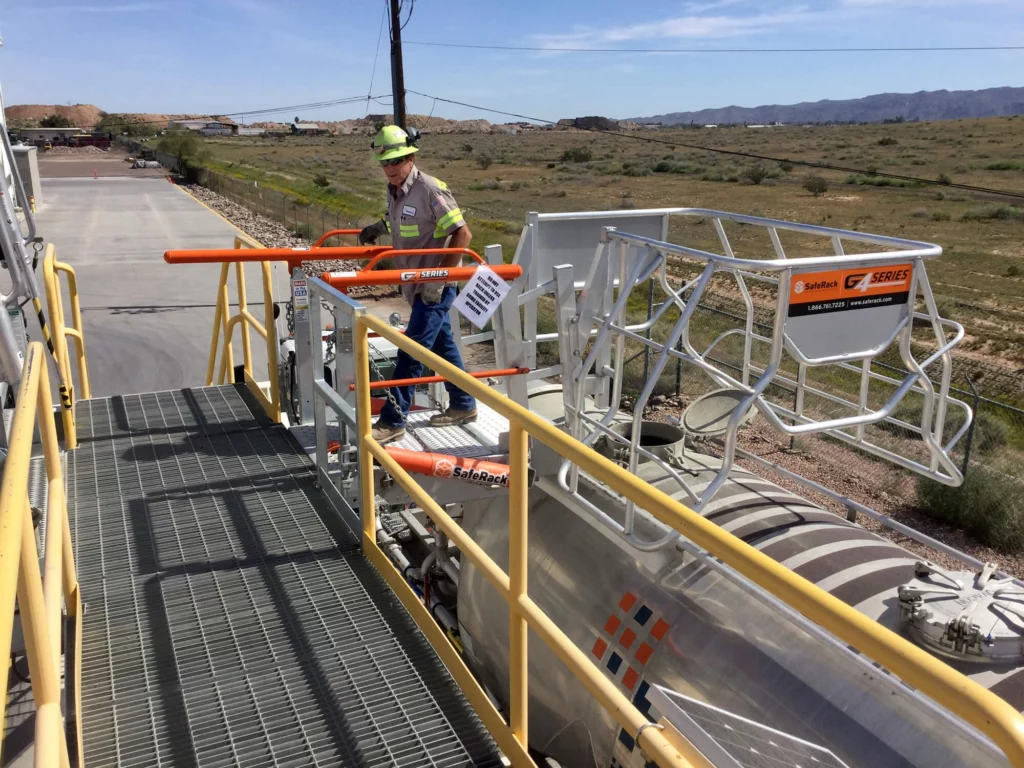
Gangway Extended Top Handrail
SafeRack’s extended top handrail provides an additional layer of safety for hopper car loading platforms, serving as a visual and physical reminder for operators.
The high-visibility, safety-orange design ensures that gangways and safety cages are properly stowed before a truck or railcar moves. This simple yet effective safety measure reduces the risk of accidental drive-offs and equipment damage.
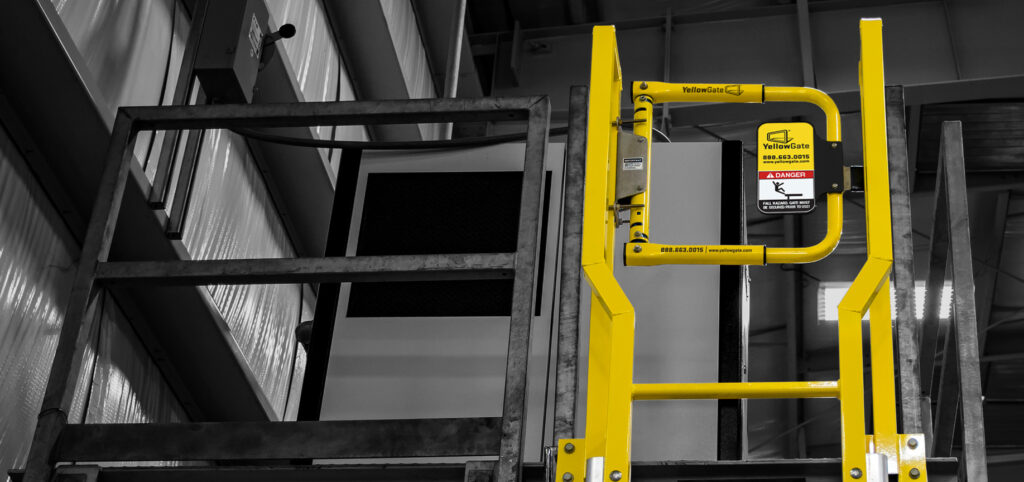
Safety Gates
SafeRack’s industrial safety gates help facilities maintain OSHA compliance and controlled access during hopper car loading operations.
Designed for heavy-duty use, these gates are adjustable and easy to install, ensuring secure access while protecting workers from fall hazards. Our team works with facilities to customize gate placement for maximum safety and efficiency.
Magnetic Swing Gates
When the gangway and safety cage are in a lowered position, the proximity switch engages the gate lock, preventing premature egress. Once the system is properly stowed, the gate automatically unlocks, allowing for safe and efficient movement.
Magnetic swing gates enhance safety and access control, ensuring that workers only exit platforms when conditions are safe.
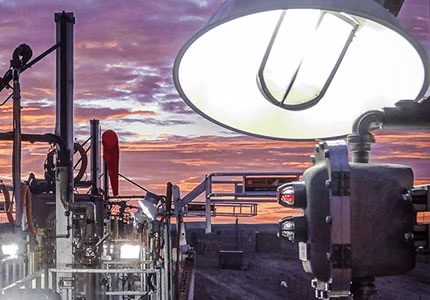
Loading Options
Lighting – Lighting both over and under the platform will be provided. For overcast days or second shift, lighting is essential for improved safety and improved productivity.
Platform & Canopies – Full platform canopies reduce exposure to the elements and improve the safe and productive loading operation from the operator’s perspective.
Operator Shelter – Depending on your site requirements, consideration should be given to the requirement of an operator or guard building on the loading platform. This can be customized to meet specific site requirements
Wheel Chocks – Railcar Wheel Chocks provide fast blocking of all types of railcars and meet OSHA regulations to safely prevent railroad cars from moving during loading or unloading operations. This is a requirement by the Department of Homeland Security
More Than Equipment—A Full-Service Partner
SafeRack’s hopper car loading solutions are backed by a comprehensive service approach that ensures long-term safety and efficiency:
✔ On-Site Safety Assessments to identify risks and workflow inefficiencies.
✔ Expert Design Support using real-time 3D configuration tools.
✔ Fast Equipment Delivery with stocking agreements available for 24-48 hour replacements.
✔ Ongoing Maintenance and Support to keep your loading operations running smoothly.
With SafeRack, you get more than just high-quality loading equipment—you gain a trusted partner dedicated to safety, efficiency, and long-term operational success.
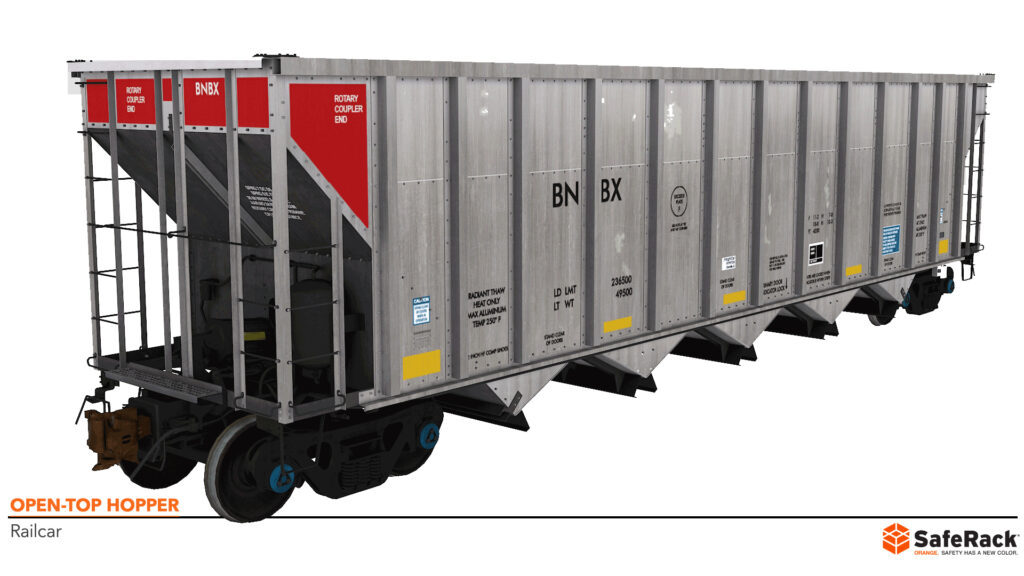
Comprehensive Fall Protection for Rail Hopper Cars
With decades of experience in railcar fall protection, SafeRack has been a leader in designing, engineering, and installing safe, efficient railcar loading systems. As pioneers in hopper railcar safety solutions, we understand what works in the field and how to create systems that stand the test of time. Our platforms, gangways, and safety solutions keep operations running smoothly, improving worker protection while maximizing throughput.
Accessing the tops of rail hopper cars presents significant fall hazards, and failure to implement proper precautions can lead to serious injuries, OSHA fines, and legal liabilities. SafeRack works directly with facilities to identify risks, develop fall prevention strategies, and implement OSHA-compliant solutions that enhance worker safety and improve efficiency. Whether working with covered hopper railcars, hopper rail cars, or open-top hopper rail cars, SafeRack provides customized solutions to mitigate fall risks and streamline operations.
By partnering with SafeRack, you gain more than just equipment—you gain a dedicated safety partner committed to protecting your workforce and optimizing your railcar loading operations.
What Customers Are Saying

I simply place the order and everything else is taken care of. I just want to say how great everyone at SafeRack has been to us since we started using them for our gangways. Dana Hamor, Tom Semiklose and John Edwards have been very, very helpful and always respond quickly to my calls or e-mails and I have no doubt that everyone at SafeRack is just as great as they have been to me. The purchasing of a great quality gangway is not a problem anymore. I simply place the order and everything else is taken care of.
By Ed S. from Buzzi Unicem
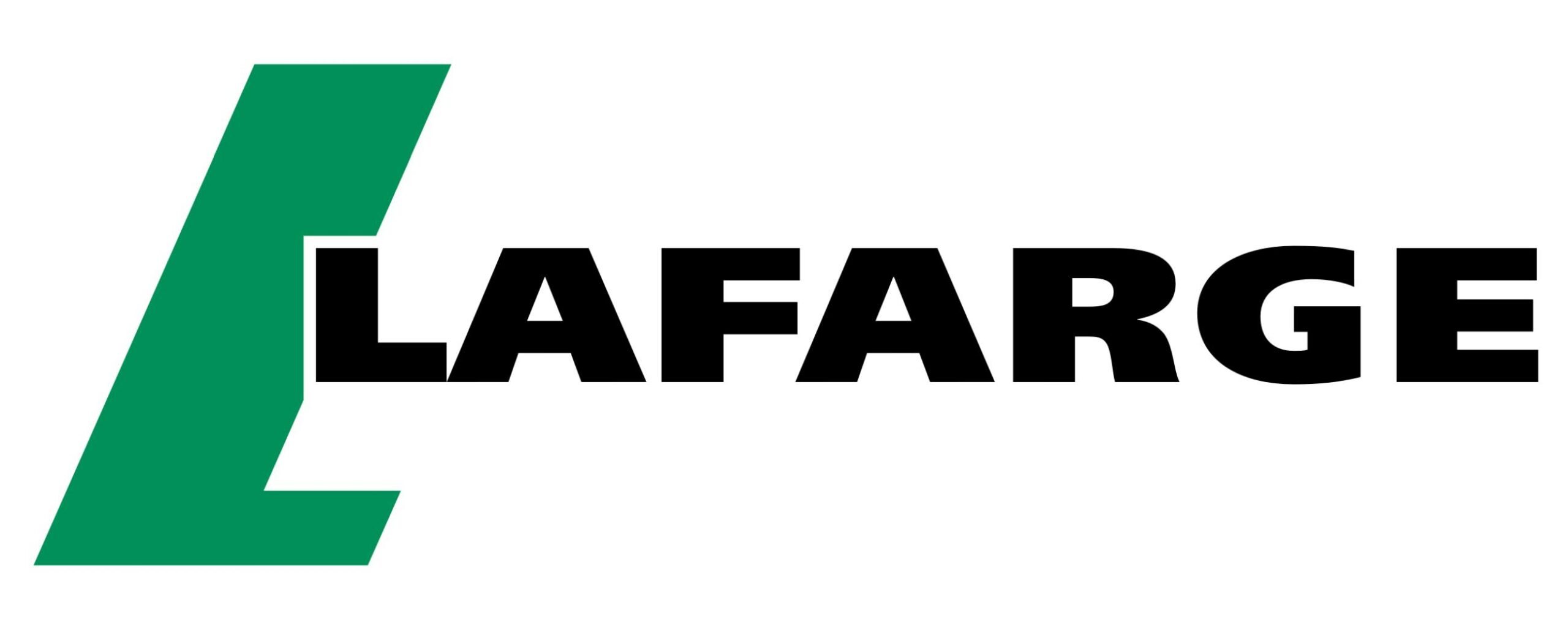
Existing parts that we had is worn that need changed. The sales team at SafeRack was very helpful and responsive.
By Carmelito L. from Lafarge C/O Financial Services Center