SafeRack Dry Bulk Loading Solutions
The cement industry has the highest volume of truck loadouts per day, making efficiency, safety, and driver satisfaction essential to maintaining productivity. SafeRack partners with industry leaders to engineer and patent innovative dry bulk loading solutions designed to improve throughput, enhance ergonomics, and reduce workplace injuries.
Why Drivers Prefer Facilities with SafeRack Systems
Truck drivers have choices when it comes to where they load their dry bulk trailers. Facilities that prioritize safe, easy-to-use equipment attract and retain drivers, ensuring smooth operations. SafeRack’s solutions make loading safer and more efficient for all drivers, including:
- Experienced drivers seeking reliability – Stable, OSHA-compliant platforms reduce slip, trip, and fall hazards.
- Aging and less physically strong drivers – Ergonomically designed equipment minimizes strain, making SafeRack-equipped facilities the preferred choice.
- Operators focused on speed and efficiency – Optimized loading systems ensure quick, seamless truck loadouts, maximizing facility throughput.
Dry Bulk Loading
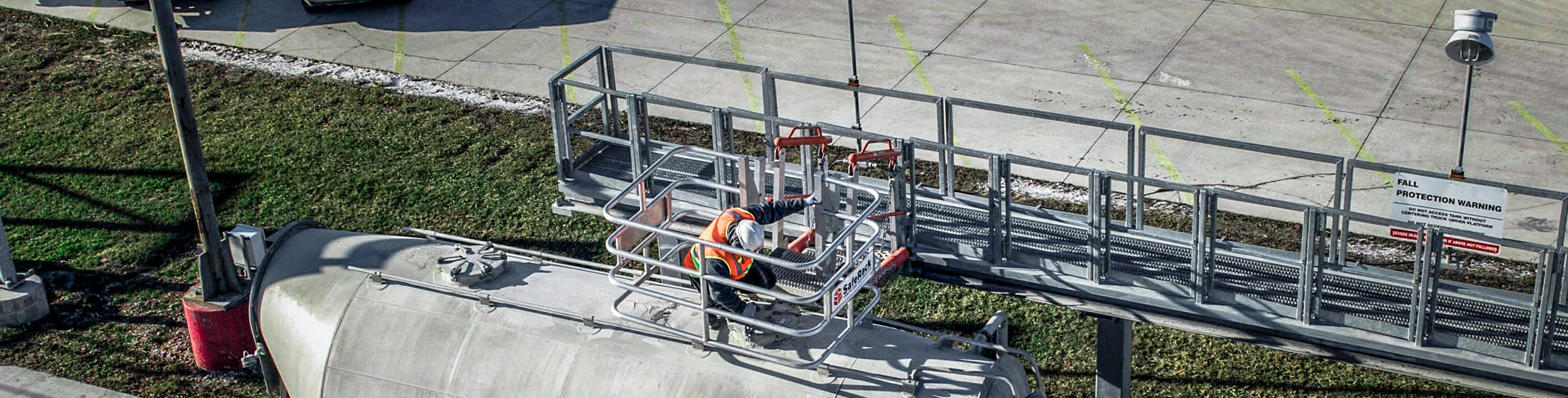
Supporting Safer Work Environments with Reliable Access Solutions
Innovations in Dry Bulk Loading
SafeRack continuously raises the bar for safety, efficiency, and ergonomics with patented solutions developed in response to customer needs. Many of our designs are the result of direct collaboration with top cement and bulk material companies seeking to eliminate accidents caused by outdated access equipment.
Safer Dry Bulk Loading with Offset Safety Cages
- Unobstructed Hatch Access – Our innovative offset safety cage features flared and tapered rungs, ensuring a full range of motion for dry bulk trailer hatches and manholes.
- Seamless Equipment Integration – The cage and gangway design prevents interference with hatch access, allowing smooth operation when the equipment is lowered onto the truck.
Maximizing Efficiency with Fast Delivery & Custom Solutions
- Industry-Leading Delivery Times – SafeRack’s advanced manufacturing processes allow us to deliver access systems in days, not weeks, keeping cement plants and terminals running without delays.
- Flexible Stocking and Rapid Replacements – Many customers rely on SafeRack’s commercial stocking agreements, ensuring 24- to 48-hour equipment replacements when needed.
- Custom Solutions for Every Facility – Our experts conduct on-site safety assessments to design solutions tailored to your dry bulk loading operations.
With SafeRack, you get more than just high-quality loading equipment—you gain an industry-leading partner dedicated to safety, efficiency, and innovation.
Dry Bulk Loading & Unloading Solutions
The following loading and unloading solutions highlight just a few of the ways SafeRack enhances safety, efficiency, and compliance in dry bulk loading operations. Our team works closely with you to assess site-specific challenges, design tailored solutions, and ensure seamless integration into your facility’s workflow.
SafeRack provides innovative, OSHA-compliant solutions that enhance safety, efficiency, and reliability in dry bulk loading operations. Our industry expertise, on-site assessments, and ability to customize solutions ensure that your facility operates smoothly and safely, minimizing downtime and maximizing throughput.
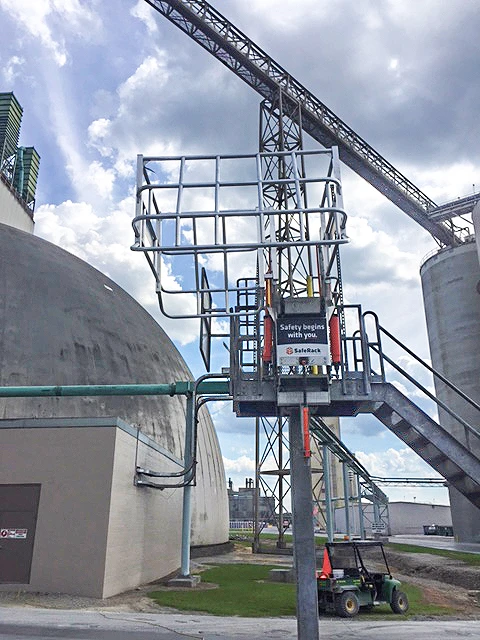
Top Hatch Access Platforms
Safe, ergonomic access is essential for loading dry bulk trailers. SafeRack’s top hatch access systems provide stable platforms for operators, ensuring efficient loading and maintenance while keeping workers protected.
- Custom Fit for Any Facility – Our team evaluates facility constraints and traffic patterns to design optimal access solutions tailored to your operation.
- Designed for Dry Bulk Operations – Built to accommodate different trailer configurations, ensuring easy access for loading and inspection.
- Lightweight, Durable Construction – Aluminum and galvanized steel options reduce weight while maintaining strength and corrosion resistance.
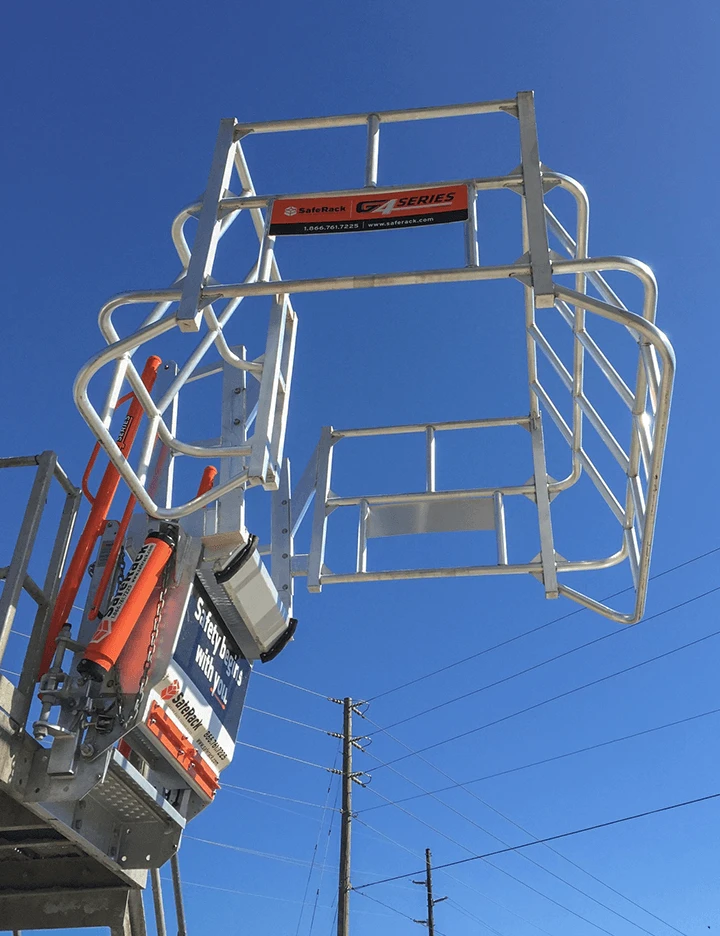
Loading Gangways with Safety Cages
SafeRack’s loading gangways and safety cages provide secure, OSHA-compliant access for dry bulk trailers while protecting operators from fall hazards.
- On-Site Design Support – Using our advanced 3D configurator, we can design and configure gangway systems in real time at your facility.
- Engineered for Dry Bulk Trailers – Safety cages are designed with offset, flared, and tapered rungs, ensuring unobstructed hatch movement during loading.
- Custom Integration – Our gangways and cages adapt to new and existing loading racks for a seamless fit.
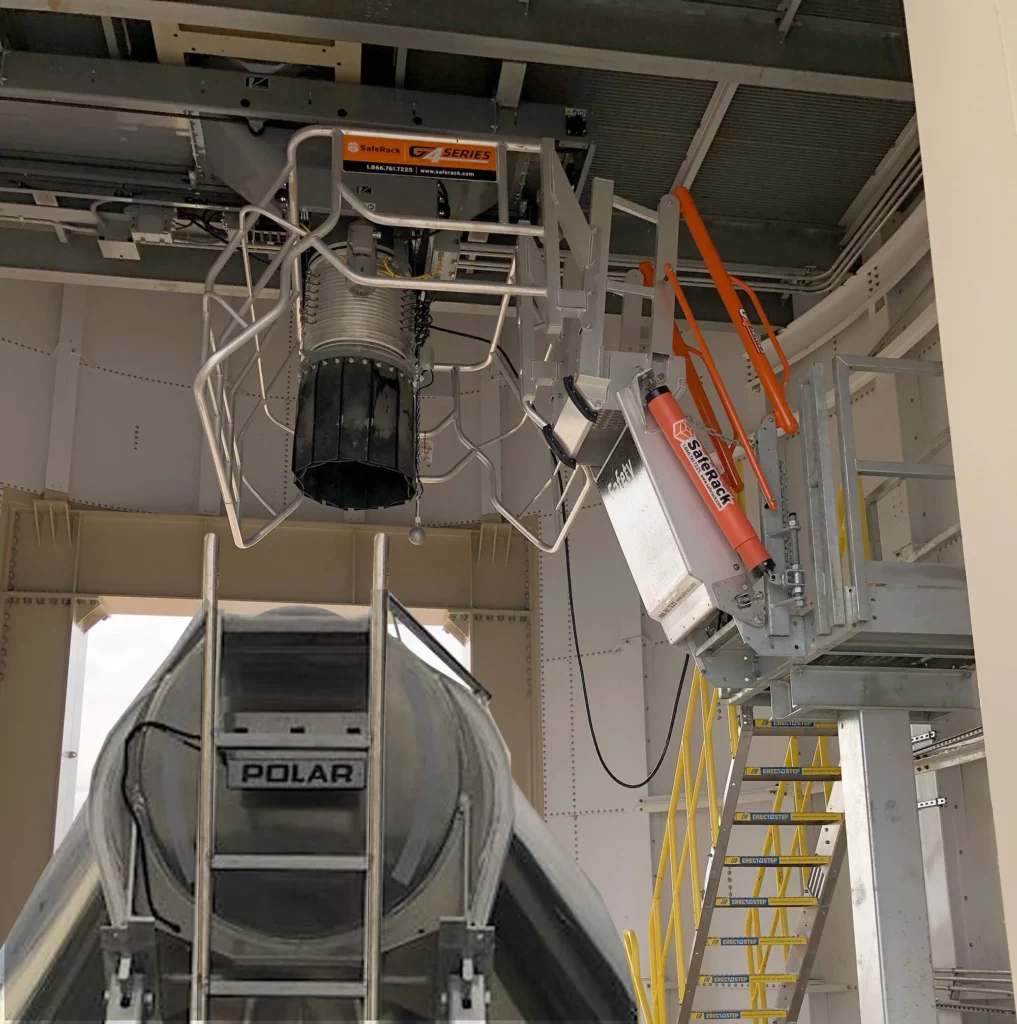
Loading Chutes
For facilities where space constraints or budget considerations impact equipment choices, SafeRack offers customized loading chute solutions that integrate seamlessly with dry bulk operations.
- Optimized for Tight Spaces – Designed to minimize gangway storage footprint while maintaining operator safety and compliance.
- Proven Engineering Solutions – Our experience in dry bulk handling allows us to design around site-specific constraints without sacrificing efficiency.
- Full-Service Support – SafeRack’s team provides on-site assessments to recommend the best chute configurations for your facility.
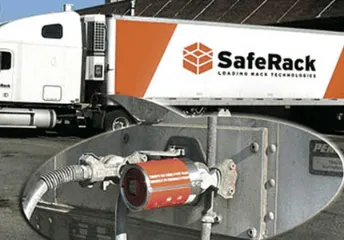
Early Departure Systems
Prevent premature truck departures and reduce the risk of equipment damage with SafeRack’s early departure systems—a vital safety feature in dry bulk loading.
- Expert Consultation – SafeRack works with your team to ensure proper system integration for maximum effectiveness.
- Integrated Safety Mechanisms – Interlocks with the truck’s braking system, preventing movement until loading is complete.
- Prevents Costly Drive-Off Incidents – Helps protect gangways, chutes, and loading arms from unintended movement.
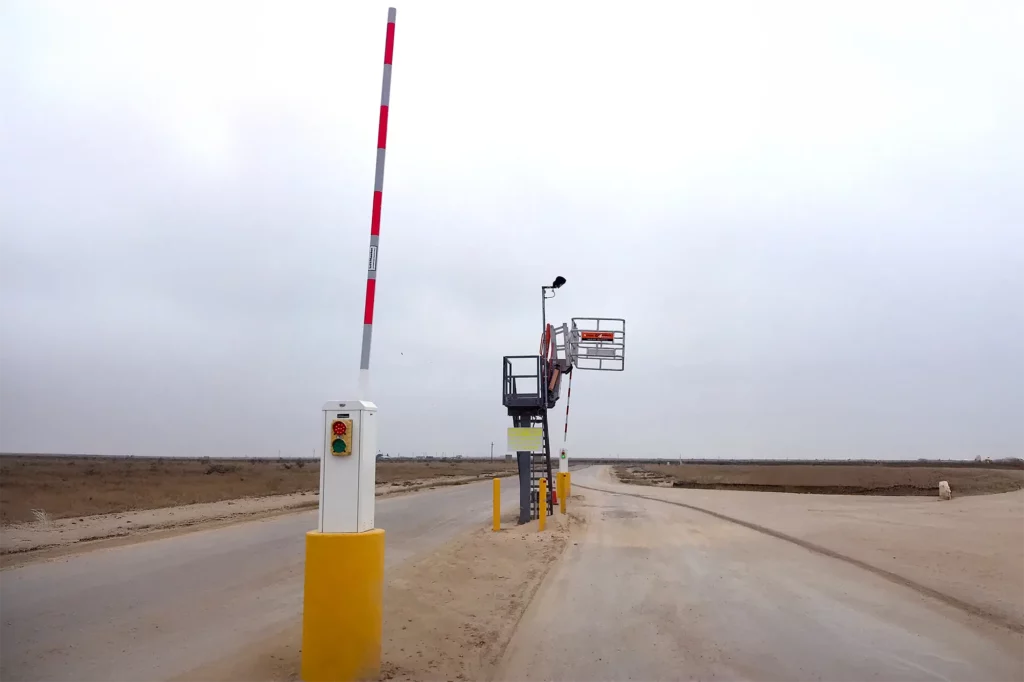
Truck Traffic Gates
SafeRack’s truck traffic gates provide an added layer of safety and control by preventing trucks from departing before gangways and cages are properly stowed.
- Custom Implementation Support – Our team helps integrate traffic gates seamlessly into your existing loading operations.
- Automated Safety Synchronization – Gates lower when the gangway is deployed, creating a clear physical barrier to prevent premature departures.
- Enhanced Driver Awareness – High-visibility LED indicators (optional) signal when it is safe to exit the loading area.
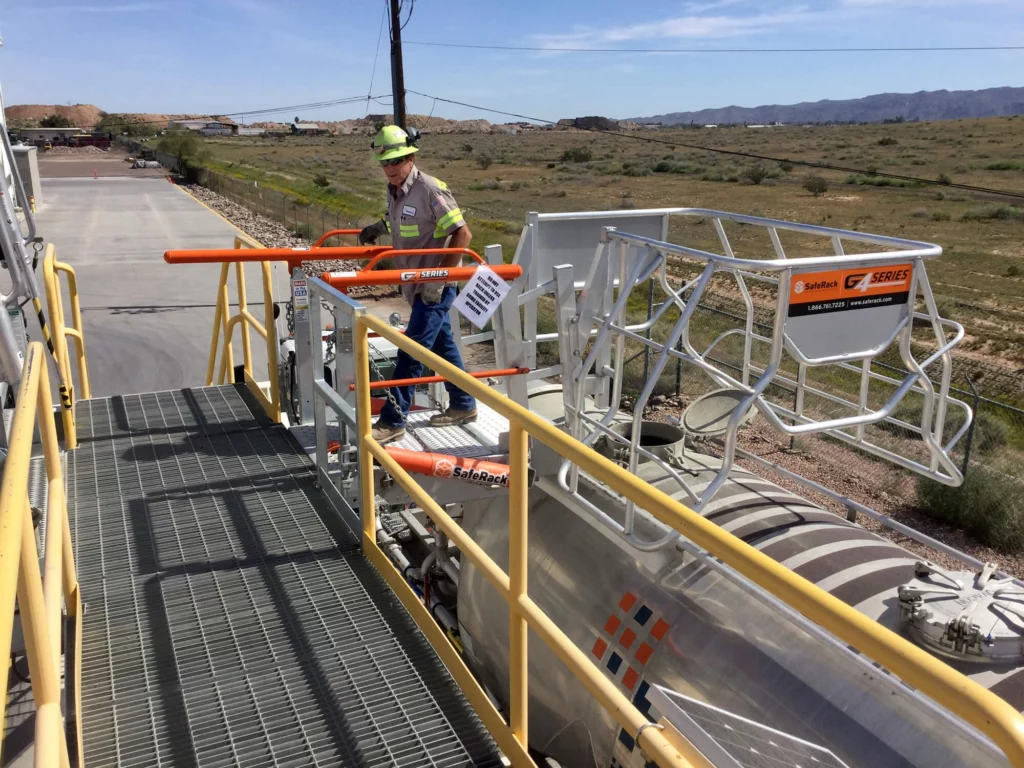
Gangway Extended Top Handrail
An additional safeguard against premature truck departures, SafeRack’s extended top handrail provides an extra visual and physical reminder to operators.
- Seamless Integration – Designed to work with SafeRack’s gangways and loading platforms for improved safety.
- Increased Driver Awareness – The bright safety-orange handrail extends into the platform, ensuring that operators properly stow equipment before exiting.
- Minimizes Risk of Equipment Damage – Helps prevent drive-offs while gangways and cages are still engaged.
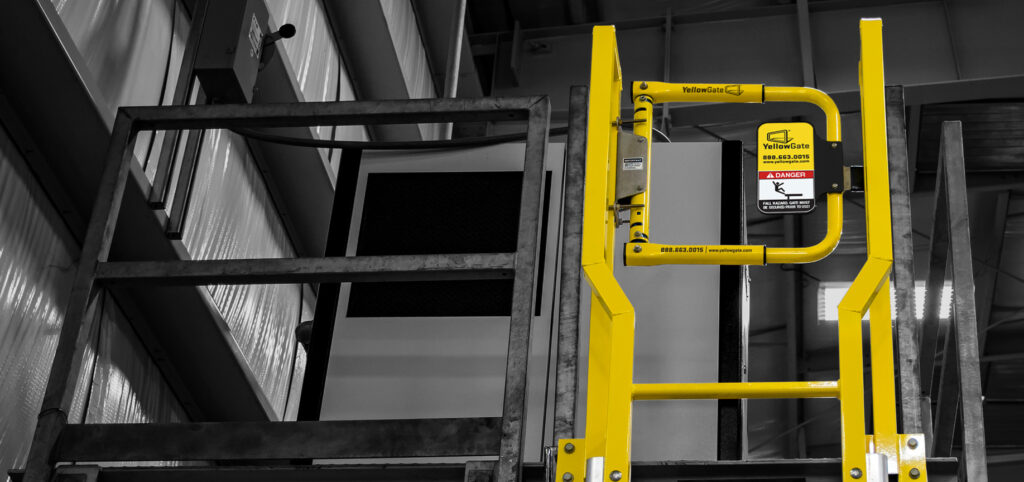
Safety Gates
SafeRack’s industrial safety gates are an essential component for fall protection and controlled access in dry bulk loading environments.
- Adjustable and Field-Ready – Gates span 16” to 36” openings and adjust easily with just a wrench.
- Durable and OSHA-Compliant – Built to withstand high-use industrial applications while keeping workers safe.
- Custom Integration for Any Facility – Our team ensures proper placement and configuration to meet your site’s safety requirements.
Magnetic Swing Gates
Magnetic swing gates add another layer of safety and access control, working in coordination with gangway and cage operations.
- Seamless Integration – Designed to function as part of a comprehensive dry bulk loading safety system.
- Automated Locking Mechanism – When the gangway and cage are lowered, the proximity switch engages the gate lock, preventing workers from exiting onto an unsafe platform.
- Operator Convenience – The gate automatically unlocks once the system is properly stowed, ensuring safe and efficient movement.
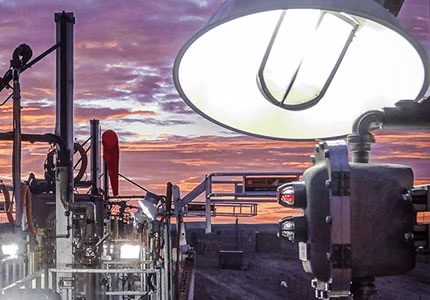
Loading Options
Lighting – Lighting both over and under the platform will be provided. For overcast days or second shift, lighting is essential for improved safety and improved productivity.
Platform & Canopies – Full platform canopies reduce exposure to the elements and improve the safe and productive loading operation from the operator’s perspective.
Operator Shelter – Depending on your site requirements, consideration should be given to the requirement of an operator or guard building on the loading platform. This can be customized to meet specific site requirements
Wheel Chocks – Railcar Wheel Chocks provide fast blocking of all types of railcars and meet OSHA regulations to safely prevent railroad cars from moving during loading or unloading operations. This is a requirement by the Department of Homeland Security.
More Than Equipment—A Full-Service Partner
SafeRack’s dry bulk loading solutions are backed by our full-service approach:
- On-Site Safety Assessments to identify risks and workflow inefficiencies.
- Expert Design Support using real-time 3D configuration tools.
- Fast Equipment Delivery with stocking agreements available for 24-48 hour replacements.
- Ongoing Maintenance and Support to keep your loading operations running smoothly.
With SafeRack, you get more than just high-quality equipment—you gain an experienced partner committed to safety, efficiency, and long-term success.
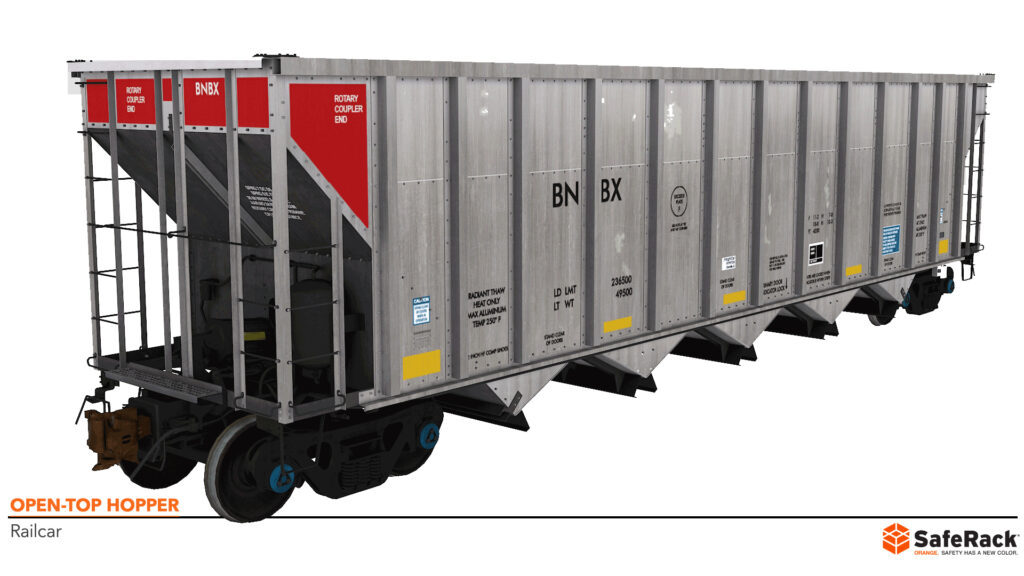
Preventing Accidents on Rail Hopper Cars with SafeRack
With decades of experience in railcar fall protection, SafeRack has been at the forefront of designing and engineering railcar loading platforms that improve safety, efficiency, and compliance. Having developed one of the first crude oil railcar loading safety systems, we understand how to create durable, reliable solutions that keep dry bulk loading operations running smoothly.
Many workplace injuries occur when workers access the tops of rail hopper cars. SafeRack’s experts collaborate with companies to develop effective fall prevention strategies, reducing risks and ensuring compliance with OSHA regulations. Beyond protecting workers, implementing proper safety measures helps facilities avoid costly fines and legal liabilities, reinforcing a commitment to workplace safety.
Dry Bulk Loading Process
Loading dry bulk materials like sand, clay, and other aggregates into a dry bulk cargo trailer is typically a straightforward process. The driver positions the dry bulk truck under a silo chute, where gravity allows the material to flow smoothly through the manhole and into the trailer. To ensure even distribution, the bulk loading process moves systematically from one manhole to the next.
More complex materials, such as plastic pellets or fine powders, require a pneumatic loading system. In these cases, compressed air moves the product from a railcar through a hose and into the dry bulk tanker. This process demands skill, as the operator must carefully regulate air pressure to maintain steady product flow without causing blockages. Before bulk loading begins, it’s critical to inspect the trailer to ensure it is clean, dry, and properly sealed. Many facilities require a wash slip to verify proper cleaning, and all manhole seals and hopper valves must be checked to prevent leaks or contamination.
Dry bulk unloading process
Unloading a dry bulk tanker truck requires precision and experience. Upon arrival at the receiving site, the driver checks in with facility personnel to verify that the delivered product matches the order. If offloading into a silo, confirming the correct destination is essential, and obtaining written confirmation can help avoid costly mix-ups.
Positioning the bulk cement truck as close as possible to the silo is key to a smooth operation. Proper planning ensures that the driver has enough hose length to make a secure connection between the dry bulk cement tanker and the silo’s intake system. Once everything is in place, the driver starts the vacuum or blower system, gradually adjusting pressure to maintain an even flow of material. The unloading path may include multiple turns and elbows, requiring careful monitoring to prevent clogging. Depending on the product, bulk unloading typically takes one to one-and-a-half hours, though an inexperienced driver may take longer if pressure mismanagement leads to blockages that require clearing.
Tank Washing in Dry Bulk Trucking
One of the key differences between dry van and dry bulk trucking is the need for thorough trailer cleaning after each load. Unlike dry van shipments, where cargo is simply unloaded, dry bulk tankers and dry bulk trucks often require a specialized tank wash before they can be reloaded with another product. This process can add significant time and cost to each shipment, as drivers may need to travel an hour or more—sometimes across state lines—to reach a certified tank wash station. In addition to the wash itself, shippers must account for the expense of deadhead miles and the tank cleaning fee.
For many dry bulk loads, the cleaning process is relatively simple. High-pressure water jets blast the inside of the dry bulk cargo trailer, using a spinning nozzle system lowered through the manholes to ensure a thorough rinse. Afterward, the bulk tanker is blown dry, making it ready for its next load. If a driver is hauling similar products—such as sand or clay—a full certified wash may not be necessary. Instead, a local wash station can perform a quick, high-pressure rinse to remove residual dust or debris.
More stringent cleaning is required when switching between different products, particularly when handling plastic pellets or other sensitive materials. In these cases, a conversion wash is mandatory. This process involves disassembling the trailer’s bottom piping, removing all fittings, and thoroughly cleaning every component before reinstallation. Ensuring a clean, contaminant-free dry bulk cement tanker or bulk cement truck is essential for maintaining product integrity and meeting industry regulations.
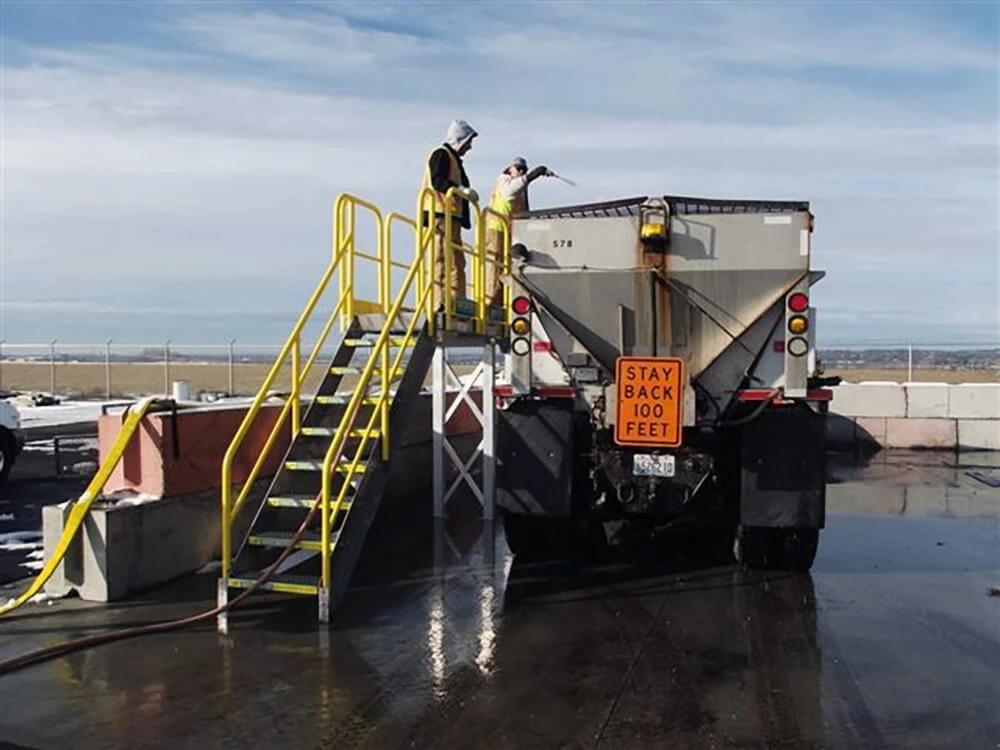
What Customers Are Saying

Good design. Good design, easy to replace seal, and easy to weld with pipe without damaging bearings or seal.
By Adam M. from Agrium
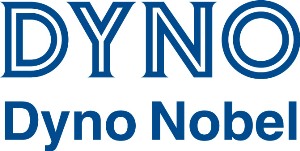
Products were delivered in a timely manner. Products were delivered in a timely manner and installed on all platforms in our plant making the plant safer. We even recommended them to our other plants.
By Johnnie P. from Dyno Nobel Inc.