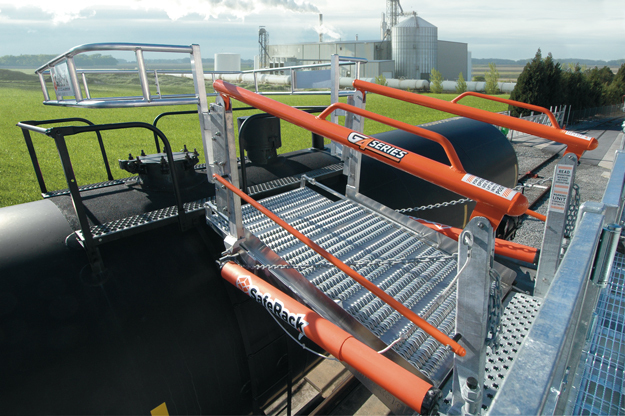
When it comes to Railcar Fall Protection, customer service is a key selling point as a liquid storage facility installs several G4 Series fall-protection systems to protect the safety of their workers.
Westway Terminals*, New Orleans, LA, which operates 18 bulk-liquid storage facilities in the United States, 12 in Europe and one each in Canada, Brazil, South Korea, and Mozambique, made the determination that the railcar fall-protection system at its Jacksonville (FL) Terminal was due to be upgraded. This was not a consideration to be taken lightly as Westway puts a great deal of pride in the safety of its employees. In fact, its Health, Safety, Environment, Security, and Quality (HSEQ) program has earned membership in the prestigious OSHA “Star” Voluntary Protection Program, as well as accreditation by ISO and GMP in Europe, and Responsible Care in the U.S.
This is especially impressive when considering that the facility is a never-ending beehive of activity with nearly 17 million gallons of capacity spread among 31 storage tanks, which handle commodities as varied as solvents, caustic soda, lignin sulfonate, acids, pesticides, and chemicals. These liquids are transferred into and out of the facility via barge, rail, truck, and ship, and stored in tanks with capacities ranging from 50,000 gallons to 2 million gallons.
Tasked with identifying and acquiring the new railcar fall-protection system was Garry Swearingen, Westway Jacksonville’s Terminal Manager. He began his search knowing he would not only need a fall-protection system that guaranteed the safety of his employees but one that had to come from a vendor that was able to also provide the best customer service. He identified three vendors he thought would be able to meet the facility’s criteria and one of them was SafeRack, LLC, the leading provider of stronger, safer, and easier-to-handle trucks and railcar loading-rack and fall-protection equipment. Handling the Westway bid for SafeRack was Chris Hite, the company’s Southeast Territory Manager. Thanks in part to Hite’s diligence, Swearingen ordered and subsequently installed several SafeRack G4 Series Flat Ramp Telescopic (FRT) Gangways for use in the railyard.
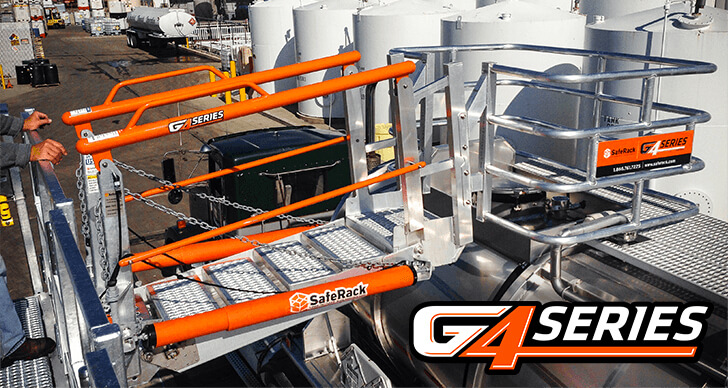
“One of the biggest selling points was Chris Hite himself,” said Swearingen. “Some of the competitor companies wanted to take measurements and give me a quote, then send the equipment out here and drop it off. Chris is a whole lot more than that. He was out here more than once to make sure he had the right dimensions, then he made sure that what he was ready to quote was what I, the customer, wanted. Chris made it work and that’s what I want—somebody who can help me make it work. Chris Hite is one of the best I’ve ever met.”
Hite’s legwork was necessary because the railyard layout required a great deal of custom design of the SafeRack equipment. Currently, Westway Jacksonville has the new FRT systems in fixed locations with an additional MAU-I mobile railcar loading/unloading access unit that can be used where needed.
“Probably over half of the systems had to have special dimensions to them because these racks, when they were built years ago, were not made for this type of fall protection,” explained Swearingen. “The rail locomotive has to pass by without hitting them, and that’s easier said than done sometimes.”
The SafeRack FRT model gangway was perfect for Westway Jacksonville’s needs because it features a slip-resistant surface and a telescoping extension on the end, which eliminates gaps when accessing the top of the railcar. The FRTs also feature telescoping top handrails with the option to add a safety cage. Westway Jacksonville is using the model with a 24-inch wide track-mount system, which allows the gangway to slide horizontally until it is over the desired area on top of the railcar. The FRT models also benefit from SafeRack’s patent-pending G4 design features, which use cutting-edge metal-stamping technology to create a stronger, yet lighter and easier-to-operate gangway. G4 Gangways are constructed using parts, most often aluminum, that is stamped out in a tool-and-die process and then formed by bending the metal into the required shape, eliminating the need to weld the pieces together.
“With our old system, there is a drop-down ramp that’s pulled out to the railcar,” said Swearingen. “With the SafeRack, there’s ease of operation. You can get the ramp down without taking two men and a boy to do it. It’s a one-man operation. The ramp comes down easily and goes up easily, and when you’re on top of the railcar, you’re protected by the cage.”
*Editorial Note: Contanda Terminals LLC (formerly Westeway Terminal Company LLC) is a premier provider of bulk liquid storage and related services across North America. We concentrate on the chemical and commodity markets and distinguish ourselves by providing high quality customer service. From creating convenient locations to custom building facilities to unique storage and blending services, we are willing to do whatever it takes to help our customers. By placing an emphasis on flexibility and quality, Contanda has expanded over the years to 15 listed facilities in North America. Customers are assured of receiving the same high quality service in whichever facility they use. Our commitment to compliance on Health, Safety, Security and Environmental (HSSE) is demonstrated by our zero tolerance for incidents. This is substantiated by many long-standing customers using our facilities in multiple locations.