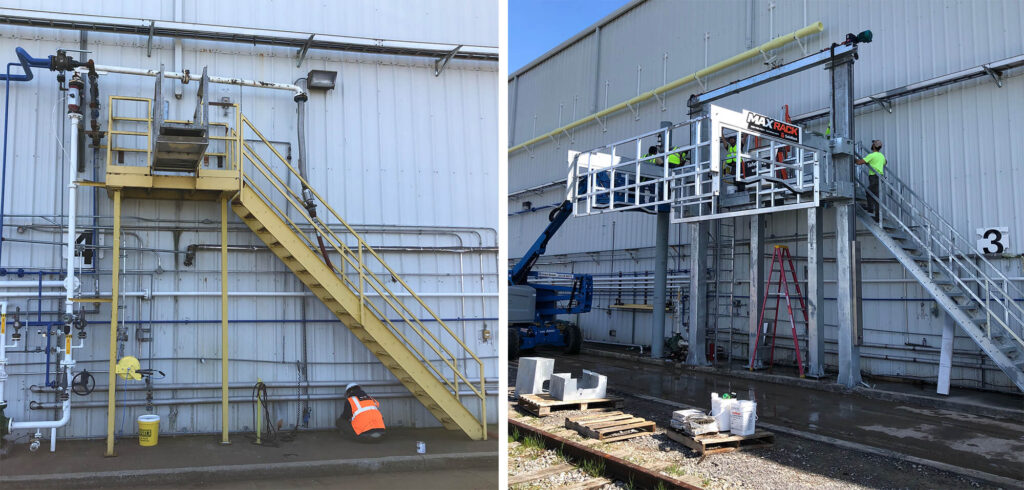
Nutrien Ag Solutions™, the retail division of Nutrien™ Ltd. provides full-acre solutions through a network of crop consultants at more than 1,700 locations around the globe. By helping growers achieve the highest yields with the most sustainable solutions possible, their wide selection of products includes proprietary brands such as Loveland Products, Inc.®, Proven® Seed, and Dyna-Gro® Seed. In addition to crop protection and engineered seed solutions, Nutrien provides a full line of liquid and granulated fertilizers to help farmers enhance crop production with increased yields to feed the world.
Early last year, Nutrien was ready to remedy serious safety and productivity issues at their Greenville, Mississippi facility. They contacted SafeRack to design access solutions for their tank truck and railcar stations that would improve efficiency and ensure safety for operators throughout the loading and unloading processes. Inefficiency and compliance issues meant production was inconsistent, with loading stations periodically unusable and ergonomically unsafe for operators. As one of the world’s largest crop inputs company, Nutrien was motivated to do the right thing for workers while improving the bottom line. The end goal was dual purpose: to design an innovative and lasting solution that provided the safest OSHA-compliant work environment for operators while increasing throughput.
Location | Greenville, Mississippi United States |
Project | Upgrade facilities bulk chemical loading platform’s |
Product | MaxRack elevating railcar cage, loading arms, platforms, access gangways, safety cages, drench showers, eyewash station |
Client | ![]() |
Product | Isopropylamine (IPA) |
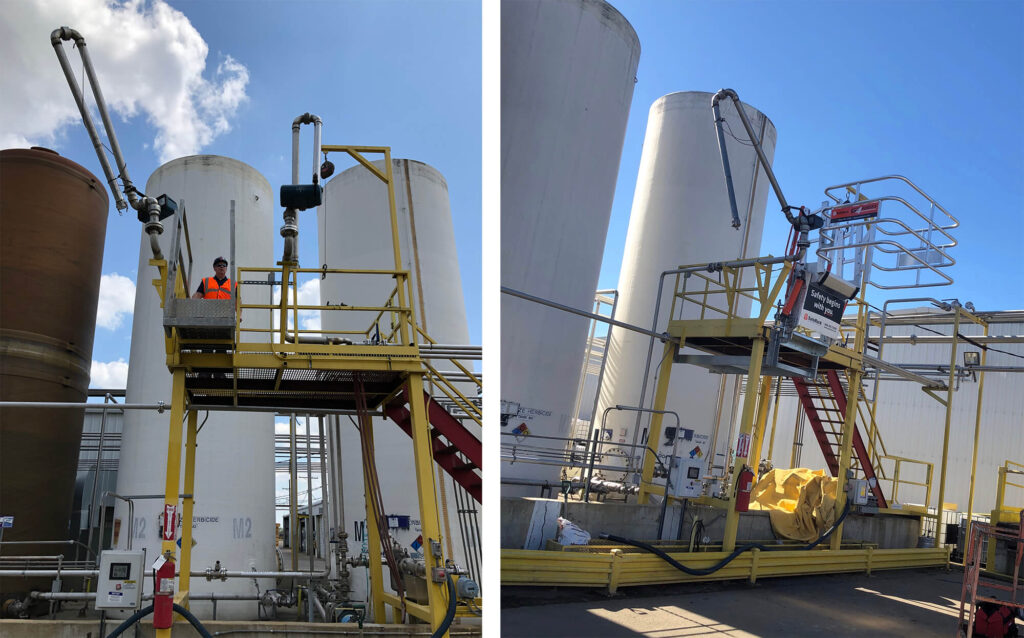
SafeRack’s Regional Area Manager Flo Verstraten knew the MaxRack elevating railcar cage would be the logical place to begin. Three outdated truck loading stations were unsafe. Upgrades including new loading arms, platforms, access gangways, and safety cages would ensure proper ergonomics to prevent repetitive injuries and fall prevention for operators while working at heights. The addition of a safety shower and eyewash station would make the installation as comprehensive as possible. The Greenville Nutrien facility bottom unloads Isopropylamine (IPA) from the liquid tank cars. IPA is a raw ingredient used to make Glyphosate which is the active ingredient in herbicides such as Roundup. Open-hatch fill splash loads mean proper measures must be taken to keep operators safe in the event of a chemical splash or spill.
Because the rail spur was particularly close to the building, a very short centerline proved to be the biggest challenge. The task was to design a system that would clear and store out of the railroad envelope when not in use. Utilizing a collaborative approach, SafeRack’s engineers worked directly with Nutrien’s team on a workable solution that would bring their facility into compliance and keep workers safe, while increasing overall productivity.
According to Verstraten, the time spent on-site prior to installation proved quite valuable in the end. “The folks at Nutrien thoroughly understood how the solutions we developed were going to help them achieve their goals,” he explained. “They also had previous experience with us on am extensive MaxRack project in Loveland, Colorado. That installation also brought them into compliance and was a game-changer when it came to ergonomics, so they knew we had the solutions they needed to improve working conditions for operators.”
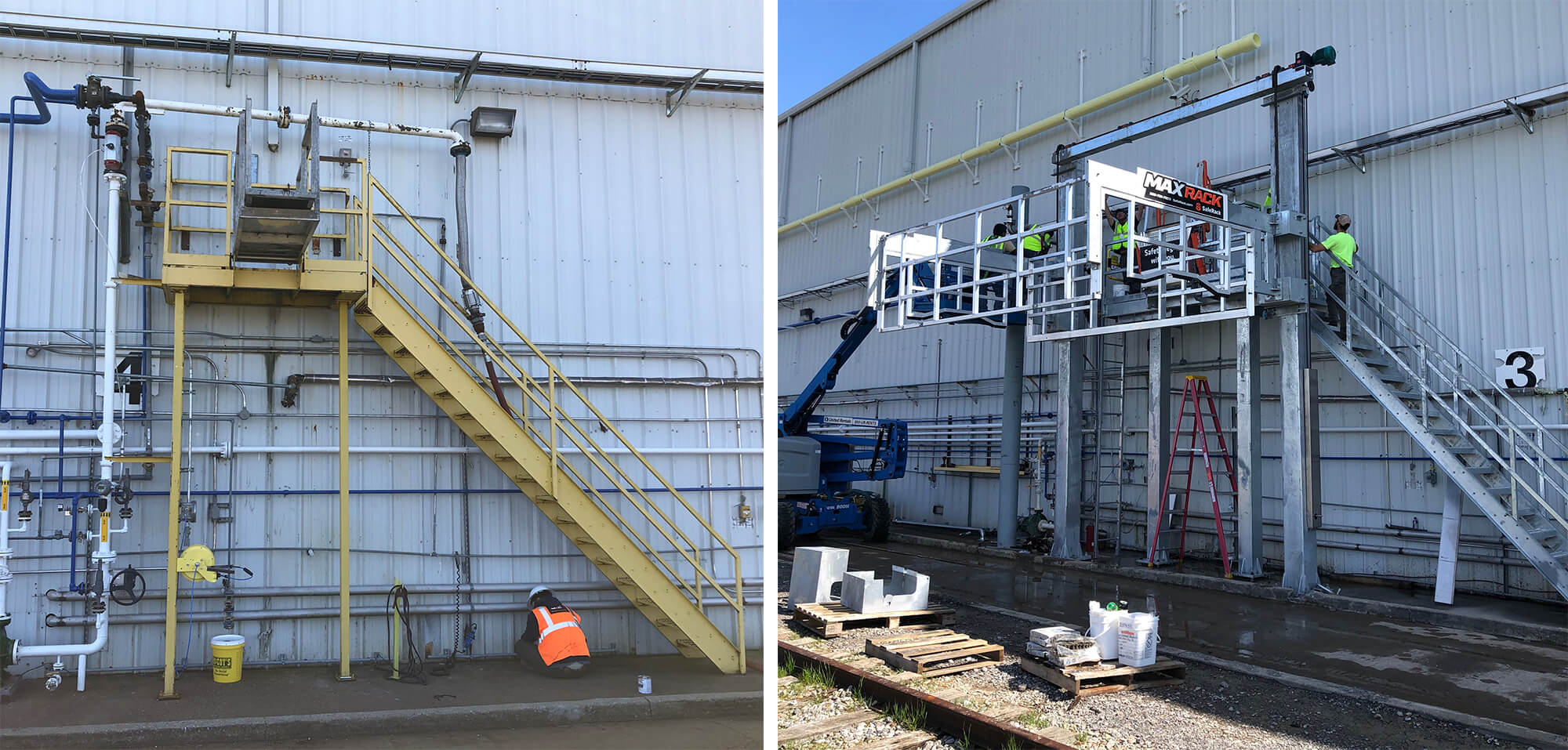
SafeRack’s SCS team took care of the installation, providing the foundation plan so all Nutrien had to take care of was pouring the concrete. A turnkey project proved to be the ideal solution. “The amount of time we spent on-site prior to the quoting process made it possible for us to be as accurate as possible. Once we secured SCS for installation, we knew it would be a seamless project,” says Verstraten.
One of the biggest challenges on the Greenville project was an existing continuous handrail that runs down the length of both sides of the Nutrien railcars. “Not a problem,” explained Verstraten. “We were able to notch both sides of the cage to accommodate the rail to create a seamless approach for operators loading and unloading.” SafeRack’s Bulk Chemical Vertical Market Specialist Ray Evans assisted with the equipment layout and design. “Anytime we can assist a powerhouse client like Nutrien improve safety while significantly increasing productivity, it’s a total win,” notes Evans. “Knowing we’re providing peace of mind to our customers makes it all worthwhile.”
Known as the Ag retailer of the future, Nutrien Ag Solutions™ keeps the needs of American farmers top of mind. They are committed to providing the best technologies, tools, and products so farmers can focus on what they do best: grow. Similarly, SafeRack has been leading the fall protection and safe access markets in the truck, rail, ship, aviation, and aerospace industries since 2003. Their award-winning products and patents have helped support the efforts of industry-leading Fortune 500 companies such as Boeing, Dow, and Coca-Cola.
“We’re in the business of overcoming problems with innovative, safe, productive solutions,” beams Verstraten. “It’s what we do.”