Environmental Stewardship in Plastic Pellet Bulk Handling
Plastic pellet pollution represents an environmental challenge where tons of plastic pellets—often called “nurdles”—enter ecosystems annually through routine bulk handling operations, causing marine life and wildlife to ingest these microplastics that cannot pass through digestive tracts, leading to malnutrition and starvation, which is why facilities must implement comprehensive containment strategies as regulatory scrutiny intensifies.
Key Takeaways:
- Regulatory Compliance: EPA requirements and Operation Clean Sweep initiatives pellet containment best practices
- Engineering Solutions: Proper spill containment systems, loading platform design, and pneumatic transfer protocols prevent environmental releases
- Business Benefits: Effective containment reduces material loss, avoids regulatory penalties, and enhances operational efficiency
- Partnership Approach: SafeRack’s expertise in bulk handling and spill containment for railcars, trucks, and facilities provides comprehensive solutions in environmental stewardship.
- FAQ Section
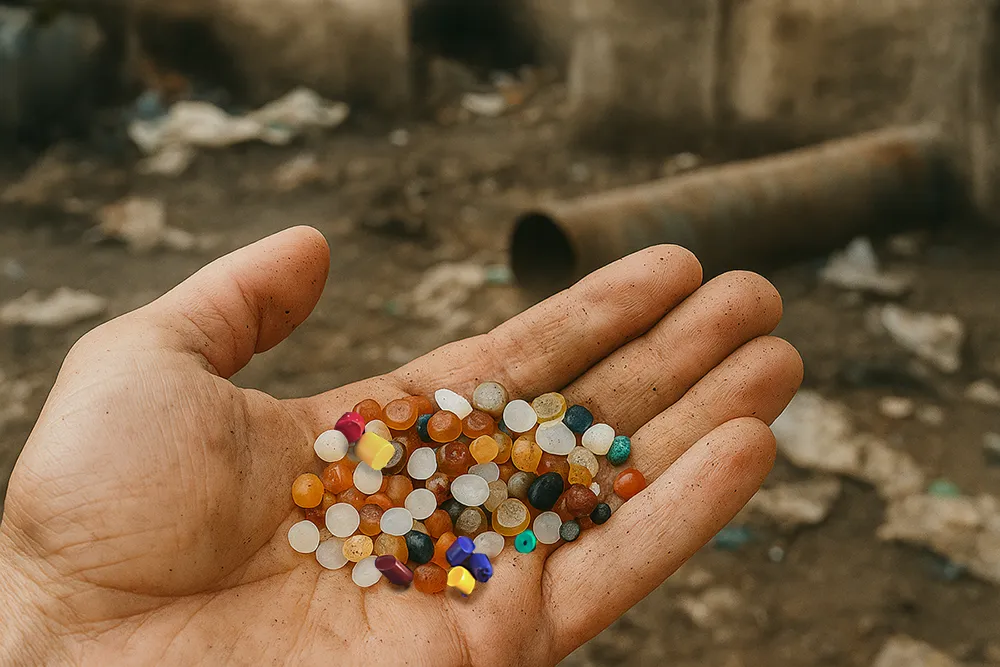
Regulatory Requirements or Framework for Plastic Pellet Containment
The regulatory landscape reflects a multi-layered approach combining existing federal frameworks, emerging legislation, state leadership, and industry self-regulation to address plastic pellet containment challenges.
Federal Regulatory Development
While comprehensive federal regulations specifically targeting plastic pellet discharge remain limited, regulatory momentum is building. The proposed Plastic Pellet Free Waters Act represents a significant step toward establishing uniform federal standards that would prohibit pellet discharge from facilities manufacturing, using, or transporting pre-production plastics under Clean Water Act authority.
Current EPA Requirements
Existing regulations under the Plastics Molding and Forming Effluent Guidelines (40 CFR Part 463) already prohibit plastic pellet discharge from certain regulated facilities. Additionally, facilities processing crude intermediate plastics fall under the Organic Chemicals, Plastics and Synthetic Fibers category (40 CFR Part 414), creating specific compliance obligations.
EPA’s Plastics Molding and Forming Effluent Guidelines
State-Level Leadership
States like California have implemented specific industrial stormwater regulations requiring containment systems to prevent pre-production plastic discharge, demonstrating how state-level action can drive industry standards ahead of federal requirements.
Industry Self-Regulation
Operation Clean Sweep (OCS), administered by the American Chemistry Council and Plastics Industry Association, leads voluntary pellet loss prevention efforts through standardized practices, employee training, and certification programs. This industry-driven initiative has gained support from America’s Plastic Makers, who advocate for enhanced federal standards and responsible transportation practices.
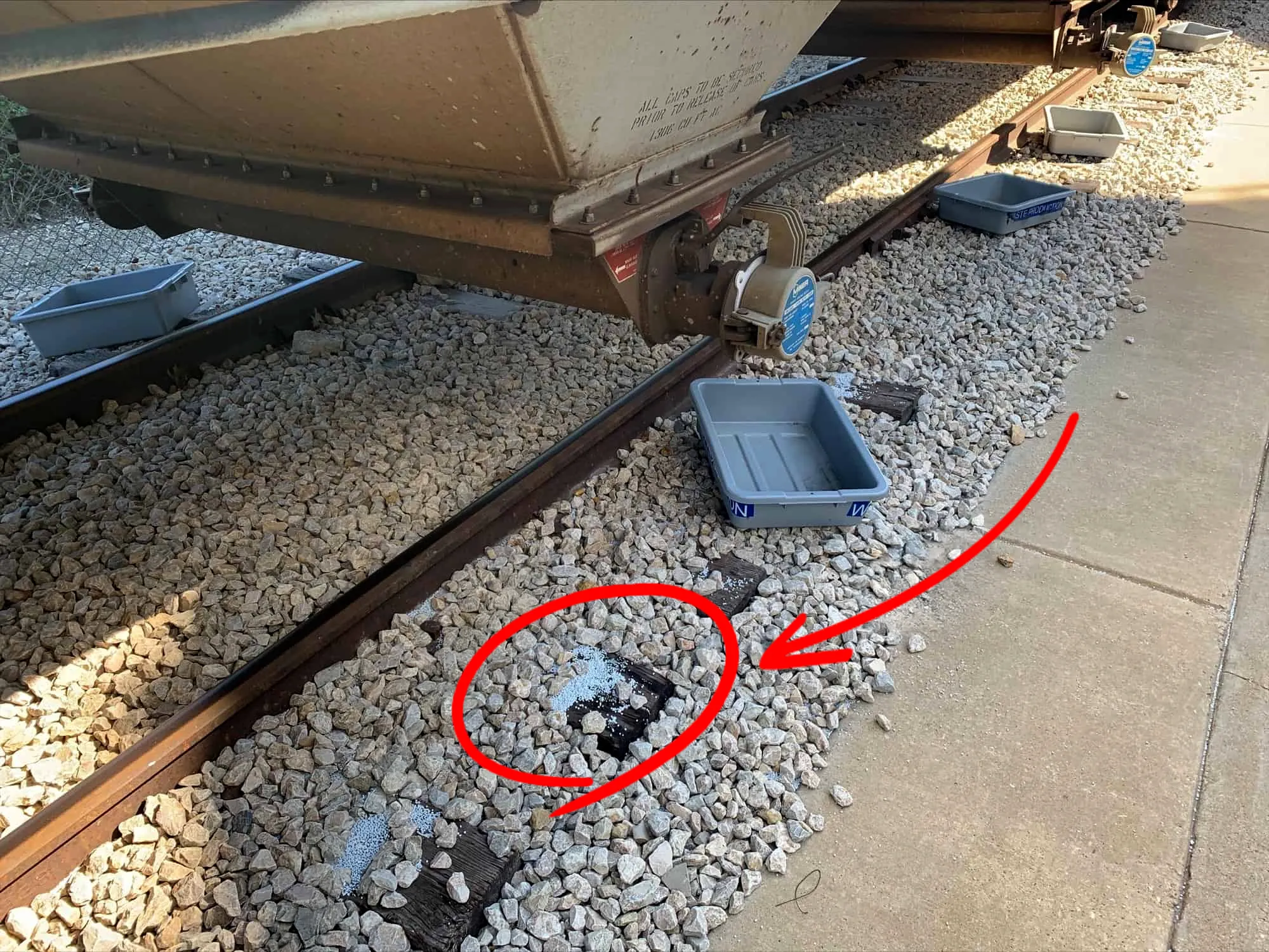
The Environmental Challenge
Plastic pellets, the raw material for countless products, are transported in massive quantities across North America daily. Even minor losses during loading, unloading, and transfer operations accumulate into a significant environmental impact. These “nurdles” persist in ecosystems for decades and pose serious risks to marine life.
Common Loss Points:
- Pneumatic loading and unloading operations
- Transfer between transport modes
- Equipment maintenance and cleaning
- Routine handling at processing facilities
SafeRack’s Containment Solutions
Effective pellet containment requires proper equipment design and operational protocols. SafeRack’s spill containment for truck and railcar solutions addresses the primary sources of pellet loss:
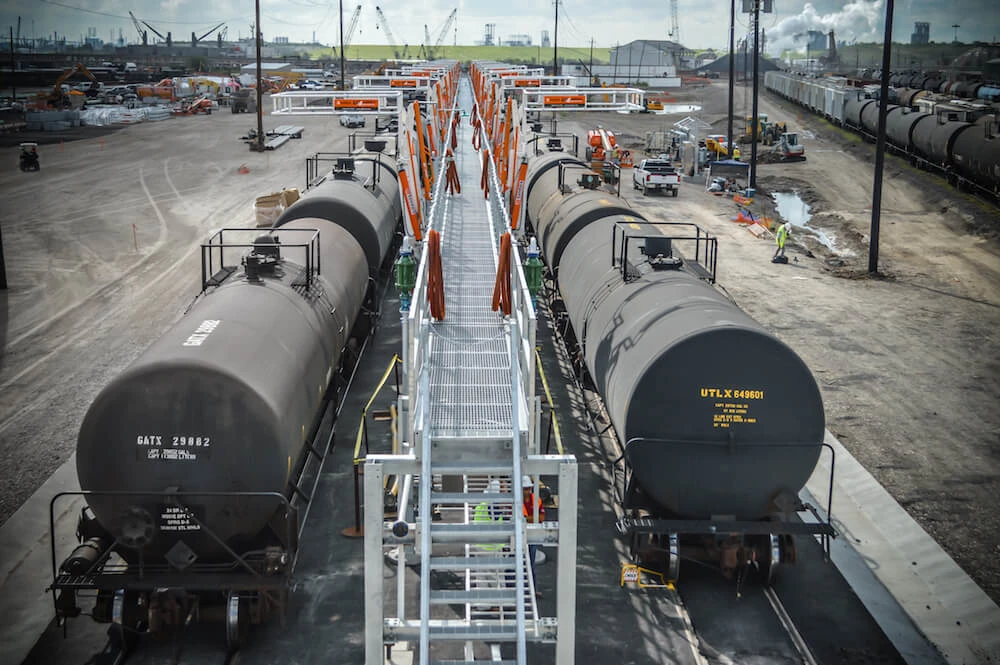
Loading Platform Systems
- Integrated spill containment with proper drainage
- Enclosed walkways that capture incidental spillage
- Non-slip surfaces preventing pellet accumulation
Pneumatic Transfer Containment
- Sealed connections preventing escape during pressure operations
- Collection systems for routine maintenance
- Emergency containment for equipment failures
Comprehensive Spill Prevention
- Track pans and truck loading containment systems
- Facility-wide drainage solutions
- Emergency response equipment and procedures
Railcar Track Pans
SPCC & EPA Compliant Track pans for capturing hazardous spills from railroad tankers and railcars
Truck Spill Containment
SPCC & EPA Compliant Truck Spill Containment Solutions
Drum & IBC Spill Containment
Interior and exterior SPCC compliant and EPA approved spill pallets
Loading Racks & Metering Skids
Truck & Railcar Transloading, Metering Skids and Loading Racks – From single-spot to multi-spot systems.
Business Benefits
Environmental stewardship delivers measurable returns:
Cost Avoidance
- Eliminated regulatory fines and cleanup costs
- Reduced material loss and replacement expenses
- Lower insurance premiums through risk management
Operational Excellence
- Improved facility cleanliness and safety
- Enhanced equipment longevity
- Streamlined operations through systematic procedures
Market Advantage
- Enhanced corporate reputation
- Stronger customer relationships
- Competitive advantage in environmental markets
Implementation and Partnership
SafeRack’s approach combines proven containment technology with operational expertise gained through decades of experience in bulk material handling. From initial assessment through final implementation, our team provides the technical knowledge and practical solutions needed to achieve both environmental compliance and operational excellence.
Environmental responsibility and operational efficiency aren’t competing priorities—they’re complementary objectives that strengthen both business performance and community relationships. SafeRack’s comprehensive containment solutions ensure facilities can protect natural resources while maintaining the productivity and compliance that drive long-term success.
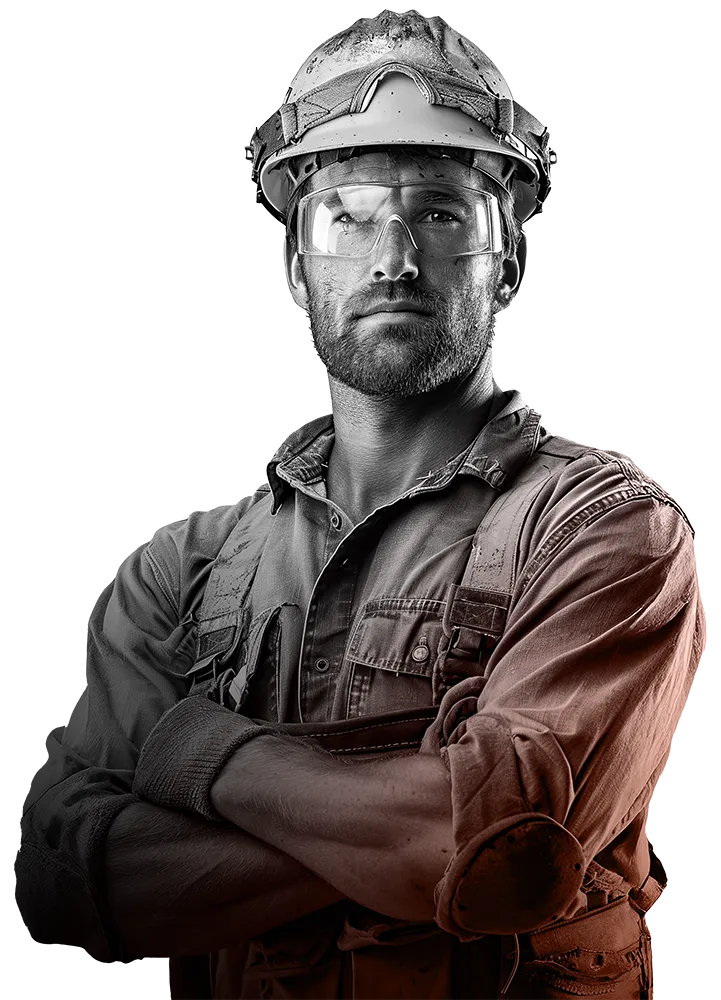
Your Full-Service Partner for
Railcar Spill Containment Site Design & Compliance
– More Than Superior Products –
- Compliance and Productivity Optimization
Expert design support to meet Spill Prevention, Control and Countermeasure Act (SPCC) 40 CFR 112 regulations while streamlining operations and reducing downtime. - Large Project Consultation
Collaboration with your team to design loading platform with spill containment solutions that meet regulations and facility needs.
- On-Site Safety Assessments
Complimentary evaluations to identify risks, ensure compliance, and improve workflow efficiency. - Proprietary Configurator
Save time and costs with same-day 3D renderings, loading and spill containment or track pan drawings, and budgetary quotes—all with built in compliance and efficiency.
Frequently Asked Questions
EPA’s NPDES permits require Best Management Practices to prevent pellet discharge. The proposed Plastic Pellet Free Waters Act would establish uniform federal standards. Many states already have specific requirements for industrial stormwater management.
EPA violations can result in significant fines, monitoring requirements, material loss costs, environmental cleanup expenses, and potential damage to corporate reputation.
SafeRack provides loading platform containment, track pans, truck loading systems, pneumatic transfer containment, and integrated drainage solutions for comprehensive spill prevention.
Any facility that loads, unloads, transfers, or handles plastic pellets should implement containment measures. SafeRack’s Regional Area Managers can conduct on-site assessments to determine your specific needs.
Yes, many SafeRack containment solutions can be retrofitted to existing infrastructure. Our engineering team designs integrated solutions that work with current operations.
Standard systems can often be installed within weeks, while custom solutions may require additional design time. SafeRack provides realistic timelines during the assessment phase.
Temporary solutions like portable berms work short-term but may not provide adequate ongoing protection. Permanent engineered systems offer reliable, long-term protection with proper drainage and facility integration.