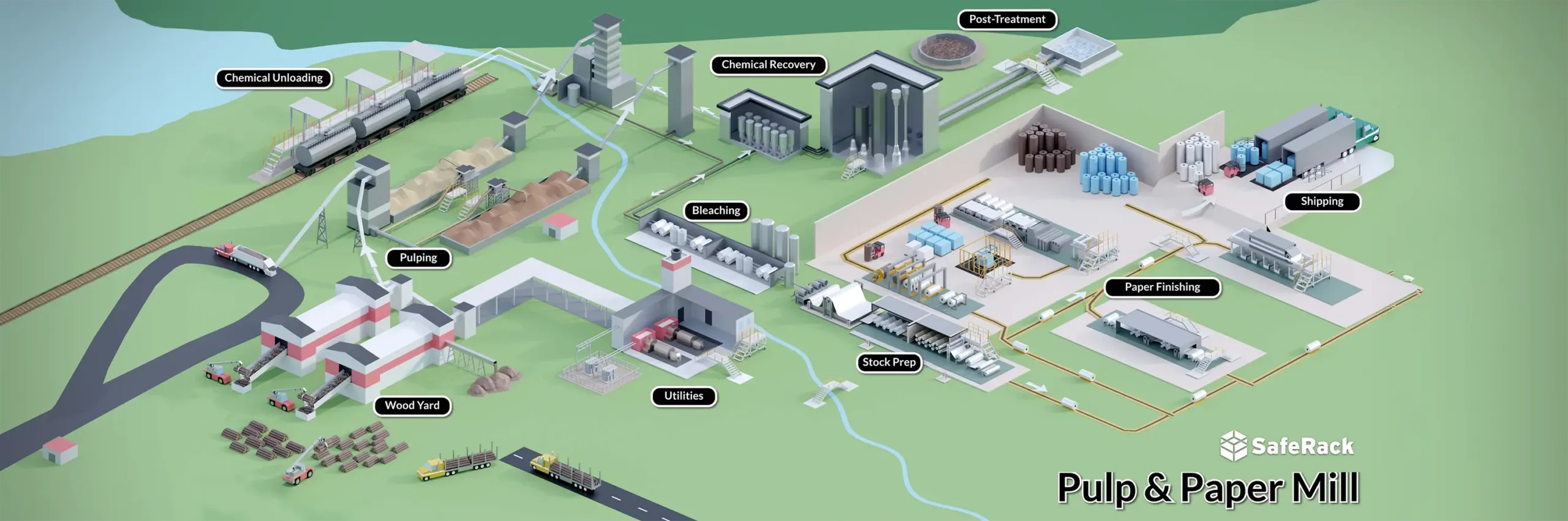
Wood Yard
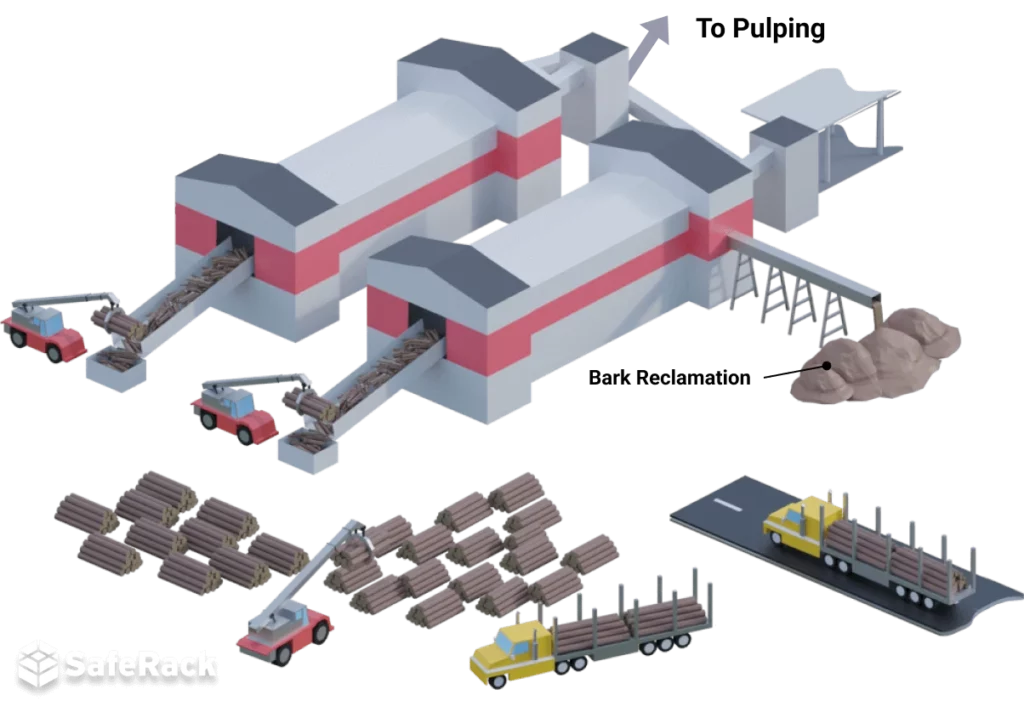
The process of making paper begins in the wood yard. Here, wood is unloaded, debarked, chipped, and screened. Wood is delivered to the mill in two forms: logs known as roundwood and as pre-cut chips. During unloading, all roundwood is separated and stacked into softwood (i.e., pine and spruce) and hardwood piles (i.e., oak and maple) so that wood fibers can be isolated later in the pulping process.
Roundwood then travels by a conveyor belt to the debarking drum. Once inside, the logs tumble until the bark is removed and falls through holes in the drum. This allows the bark to be reclaimed later and utilized as an environmentally friendly biofuel. From there, logs are fed into an industrial chipper. The chipper converts them into 1”x1” square chips within a matter of seconds.
The chipper converts the logs into 1”x1” chips, which are then sent through a screening process to remove any irregularities. Chip uniformity will be important later in the process. The undersized chips, sawdust, and bark are sent to a power boiler to generate clean electricity that helps power the mill and supporting buildings. If wood chips were delivered directly to the mill, then they are unloaded and sent directly to screening, bypassing the earlier steps. Hardwood and softwood remain separated as the wood chips await the pulping process.
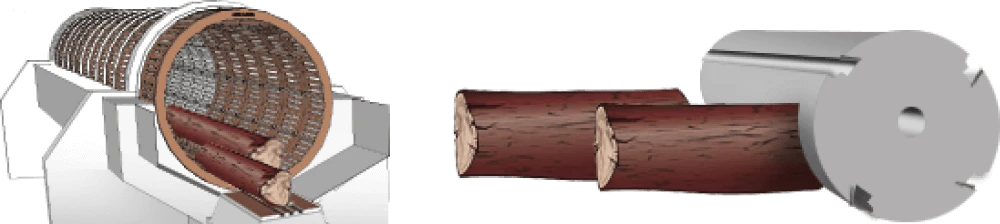
A drum debarker consists of a large rotating cylinder (the drum) and an inside surface equipped with ridges. As the drum rotates, the ridges cause the logs to tumble against one another. The bark is removed through friction, while other debarkers such as ring debarkers and chain flail debarkers mechanically remove bark.
The two most common types of wood chippers used in the pulp and paper industry are disc chippers and drum chippers. Disc chippers consist of a steel disc, spout, and chopping blades. Logs are typically fed to the disc using an angled spout. The chopping blades are mounted to the disc. Disc chippers produce the most uniform chips but the blades must be sharpened often which results in downtime.
The second type is a drum chipper. Drum chippers consist of a large steel drum and blades. The drum is horizontally orientated and the knives mounted to the drum cut with a scooping motion. Drum chippers are more energy efficient but can produce uneven chips.
SafeRack is the safety leader for loading and unloading solutions for the pulp and paper industry. Our innovative solutions allow workers to safely, efficiently, and cost-effectively load and unload railcars and road tankers.
Pulping
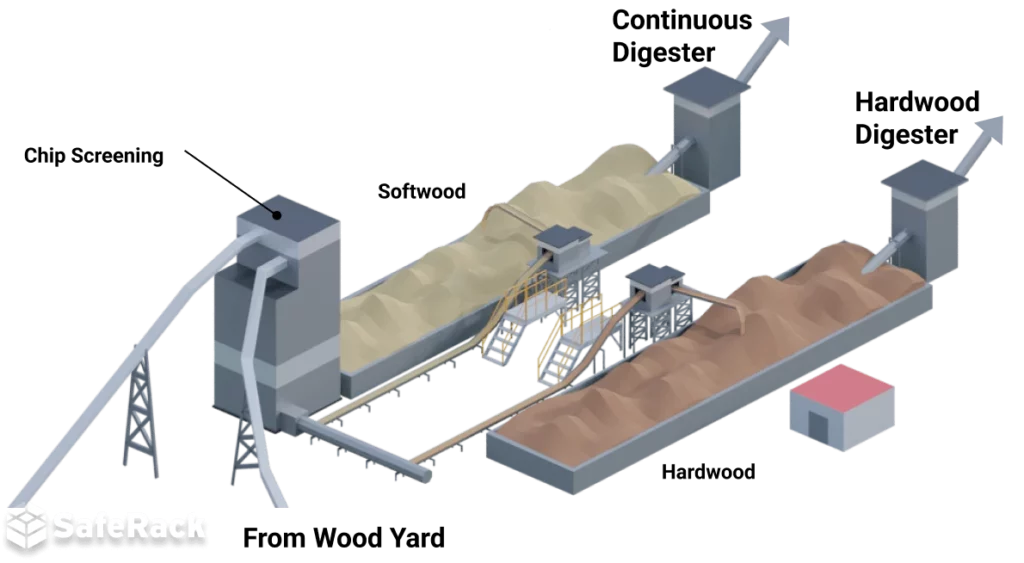
Once the roundwood has been chipped and screened, it is ready to enter the pulping process. During the chemical pulping process, the wood chips are transported on conveyor belts into a large machine called a digester. A hot mixture of water and chemicals referred to as “white liquor” are added to break the bonds between lignin, cellulose, and hemicellulose. The wood spends about 2 hours in the digester under extreme pressure and heat until the wood disintegrates leaving behind wood fibers (pulp) and black liquor.
From there, the pulp and black liquor are sent to the washing and screening area where the black liquor is washed away. Oxygen delignification also occurs at this stage, which removes any remaining lignin. The process also helps to remove some of the natural brownish color from the pulp so that fewer chemicals are required during the bleaching process. The pulp is then bleached until it achieves a bright white color.
Despite the use of chemicals, chemical pulping can be an environmentally friendly process. Many mills use chlorine-free or ECF chemicals for bleaching. Moreover, most facilities operate in a “closed loop” system. Chemicals are reused for the next batch of pulp and the left-over liquid is used to generate electricity for the plant.
The fibers are now ready to make paper.
A digester is a large vessel used for chemical pulping in which wood reacts with a chemical liquid, pressure, and heat to isolate cellulose fibers for pulp. Some digesters operate in a batch manner while others use a continuous process.
Chemical & Material Transfer
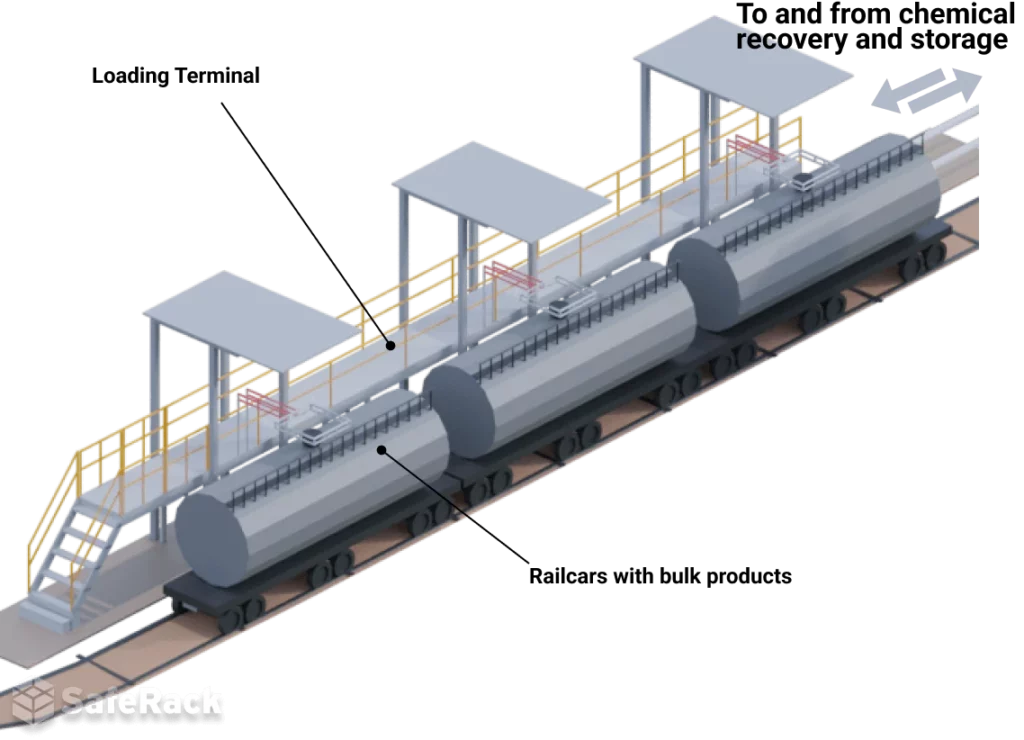
Pulp and paper manufacturing processes require the transportation of hazardous chemicals. Some of these chemicals are used in the manufacturing process while others are byproducts that are recylced and repurposed.
For instance, green liquor is a manufacturing byproduct that is used to make white liquor. When transported by rail, green liquor is typically shipped in 26,000 gallon DOT-111 tank cars equipped with safety valves that meet DOT specifications. Green liquor is a closed-loop loading operation that is top loaded into rail cars via chemical hoses or 3” stainless steel loading arms.
The loading and unloading process can expose workers to significant risks. If not handled properly, green liquor can cause burns. Moreover, since operators are required to go on top of tanks during loading and unloading, they require adequate fall preventation that keeps them safe without compromising productivity.
Tank truck loading and unloading procedures are similar to railcar applications. DOT trailers approved for the transport of green liquor include MC 307 or low pressure chemical ISO containers. However, unlike railcars these trailers are usually bottom unloaded. An extension pipe with two valves is flanged to the top of the trailer. Trailers must be equipped with pressure relief valves and remote controlled stop valves.
A loading platform consists of a platform and a loading arm that helps workers to safely load and unload a truck tanker or railcar. Loading platforms typically have facilities for both top and bottom loading and are equipped with control devices that prevent overfilling and ensure that vehicles are grounded to prevent dangerous statc discharges.
Chemical Recovery
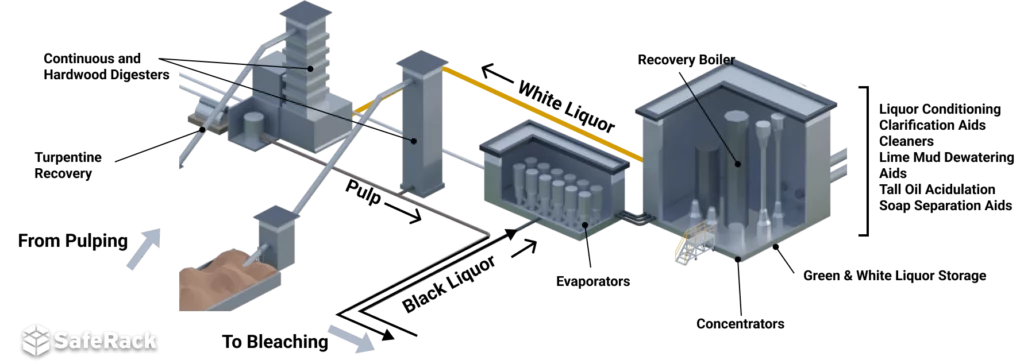
Black Liquor
Black liquor is the byproduct of the kraft process when lignin and hemicelluloses are removed from the wood to free fibers. The black liquor contains more than 50% of the energy content of the wood that was fed into the digester. Paper mills use it as an energy source.
White Liquor
White liquor consists of caustic and sodium sulfide. This solution is combined with heat and pressure to help release lignin from fibers in the wood to produce pulp.
Green Liquor
Black liquor is burned in an oxygen deficient atmosphere to form a molten material that is referred to as “smelt.” The smelt is combined with water to produce green liquor. Green liquor is typically reacted with lime to regenerate white liquor.
Today’s pulp and paper mills face rising energy and chemical costs as well as increasingly stringent environmental and safety regulations. It is critical for pulp and paper mills to maximize power production while minimizing chemical losses.
The chemical recovery process furthers these objectives by:
- Minimizing the environmental impact of waste material
- Recycling pulping chemicals
- Generating steam and power
Recall that white liquor is added to the digester to help remove lignin and hemicelluloses to isolate the wood fibers. The byproduct of this process is called black liquor. Black liquor contains more than 50% of energy content of the wood and is th 5th most important fuel sources in the world behind coal, oil, natural gas, and gasoline.
The black liquor is burned in an oxygen deficient atmosphere to form smelt. The smelt is then combined with water to produce green liquor. Green liquor is reacted with lime to form white liquor. The white liquor can then be used in the pulping process.
Evaporators are used to evaporate black liquor to increase its dry solids percentage. This process releases volatile compounds from the black liquor for reuse in the mill. The compounds are typically incinerated using kilns or a recovery boiler. A recovery boiler is used to recover inorganic chemicals as smelt and burn off the organic chemicals so they are not discharged as pollutants.
Bleaching & Stock Prep
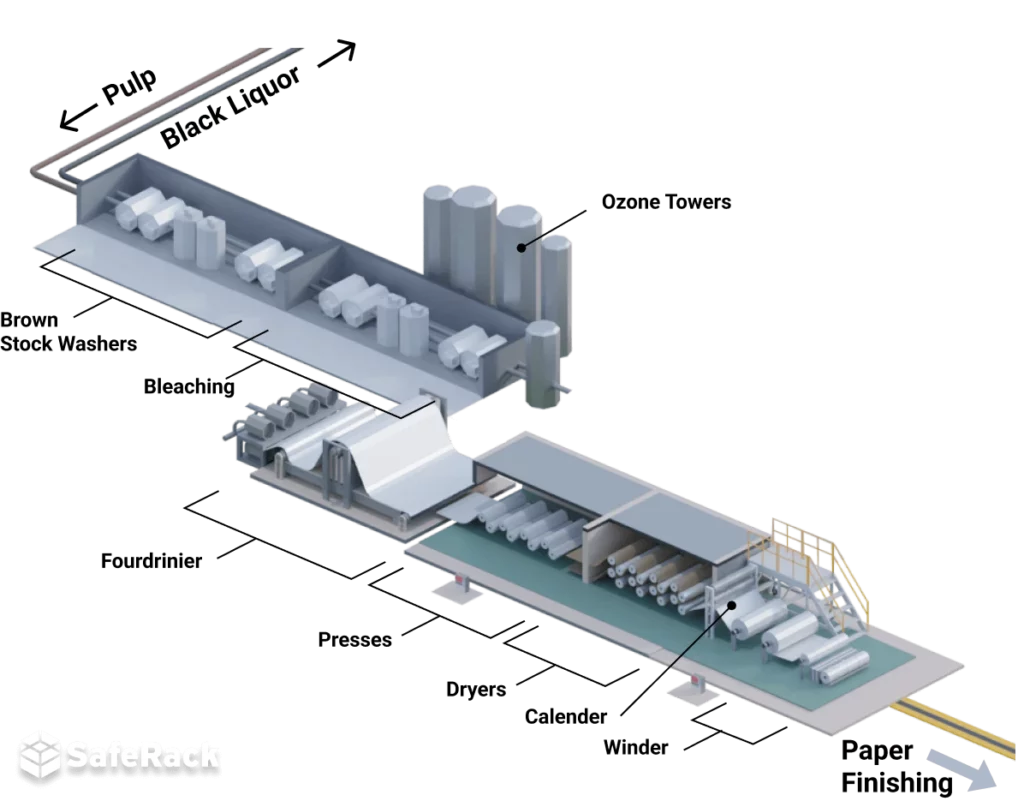
The Fourdrinier machine, or flat wire machine, is a paper machine that utilizes a horizontal, moving mesh upon which a mixture of pulp and water is deposited. The pulp travels through the machine on an endless belt of mesh. Excess water is drained off forming a continuous sheet for further drying by suction, pressure, and heat.
The presses squeeze the web of wet papers and lower water content to about 65%.
Drying consists of a series of cast-iron cylinders, heated to a temperature in excess of 100°C, where the web of sheets pass through to reduce the moisture content to approximately 6%.
Calenders (rollers or plates) smooth the paper or board and impart gloss or other desired finishes to the surface.
Now that we have extracted the fibers from the wood, we are ready to refine the pulp, add fillers and dyes, and run the mixture through a paper machine. During the refining process, the fibers are shortened and frayed to increase the contact area and make it easier for the fibers to intertwine. There are some significant differences between hardwood and softwood fibers, and it is for this reason that they have been isolated throughout the pulping process.
Softwood fibers are long and have a greater contact area, adding strength to finished sheets. Hardwood fibers are short and pack closer together. This helps make paper smooth while also adding bulk and opacity. Altering the content of softwood and hardwood fibers allows manufacturers to create paper products that have a broad range of physical characteristics.
The softwood and hardwood fibers are pumped into a blend chest along with fillers such as clay and calcium carbonate to improve the appearance and quality of the paper. This blended mixture is called the furnish. Once mixed, the furnish moves from the blend chest to the paper machine.
In its simplest form, a paper machine is like a large dryer. As the furnish and paper move through the machine at a high rate of speed water is gradually extracted. Modern paper machines are based on the principles of the Fourdinier machine. These machines can vary greatly in size with some being as large as a football field.
Most paper machines consist of 5 sections:
- Forming
- Presses
- Dryers
- Calender
- Winder
As the furnish enters the forming section, it consists of approximately 99.5% water and 0.5% fillers and additives. A continuous rotating wire mesh removes water from the paper through simple gravity while a top wire former suctions water from above the mesh. It then passes through the presses which are large rolls loaded under pressure. The presses reduce moisture levels in the paper to approximately 65%.
The paper then makes its way into the drying section. Here, a series of steam heated drying cylinders reduces the moisture content to around 6%. In the calender section, the dried paper becomes smooth under high pressure and loading. High tech scanners analyze the paper for variations such as weight, brightness, moisture content, as well as physical defects such as small holes.
In the winder section, the paper exits the machine and is wound onto large steel spools that are capable of holding over 15 tons. When the spools reach capacity, they are split into smaller rolls and rewound onto thick cardboard cores. This makes it easier to transport paper to the wrapping station or to other areas in the mill for further processing.
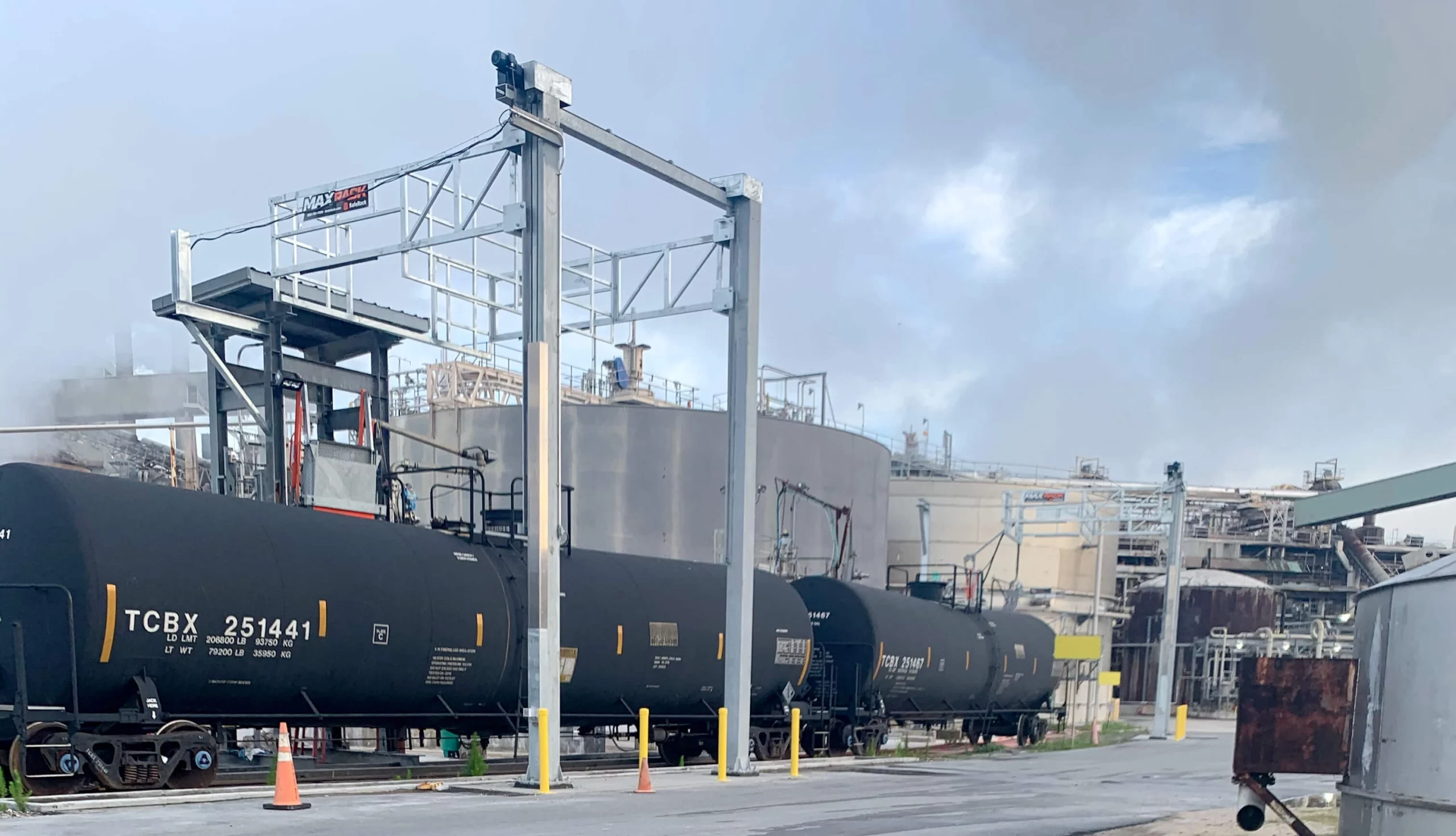

This Palalka, Florida installation is a three spot loading terminal for loading railcars with Caustic, Tall oil and Black Liquor.
Installed are SafeRack’s 48” wide pneumatic FRT gangways interlocked with customized MaxRack Elevating Safety cages.
Paper Finishing
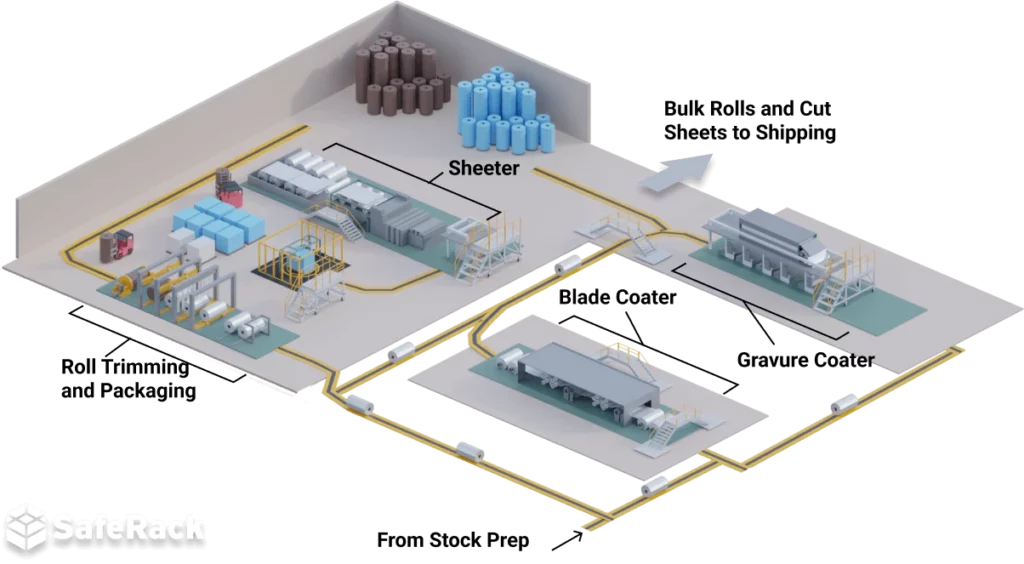
In the finishing area paper is prepared according to customer specifications. As finished rolls leave the winding area, they are transported to a packing station. Once in the packing station, the rolls receive a watertight polywrap or a moisture-resistant craft wrap. The wrap is applied while the rolls are spinning.The edges are also folded and glued down. End caps, which are thin cardboard caps, are pressed onto both sides of the roll. The roll then receives a label and is shipped to the customer.
When a customer requires a sheeted product, the rolls are loaded into a sheeter. The sheeter cuts the paper with a rotating blade and stacks them into reams..The reams then travel on conveyor belts to receive a moisture resistant wrap and product label. Finished reams are then packaged into cartons and shipped to the customer.
Depending on the customer’s specifications, a broad range of finishes or coating can be applied to the paper. During the coating process, coating or color is spread onto the surface of the paper. The coating substance can contain pigments, binding agents, and/or various additives. Multiple applications of a coating can increase the quality of the paper, with high-grade printer paper receiving up to 3 applications.
A gravure coater is a kind of roll coater, in which the resin is applied to an engraved roll. Typically a blade scrapes the resin off, leaving an appropriate amount in the engraved cells. Within a specific set of operating parameters, this is a highly repeatable process. However, modifying the coating laydown rate can be time consuming.
In blade coating, the coat weight is controlled by varying the pressure that is applied on the blade, which presses the blade tip against the paper.
Sheeting is the process of cutting paper into specific lengths and widths. Sheeters can take large rolls and create smaller sheets of material to meet any needs.
Shipping
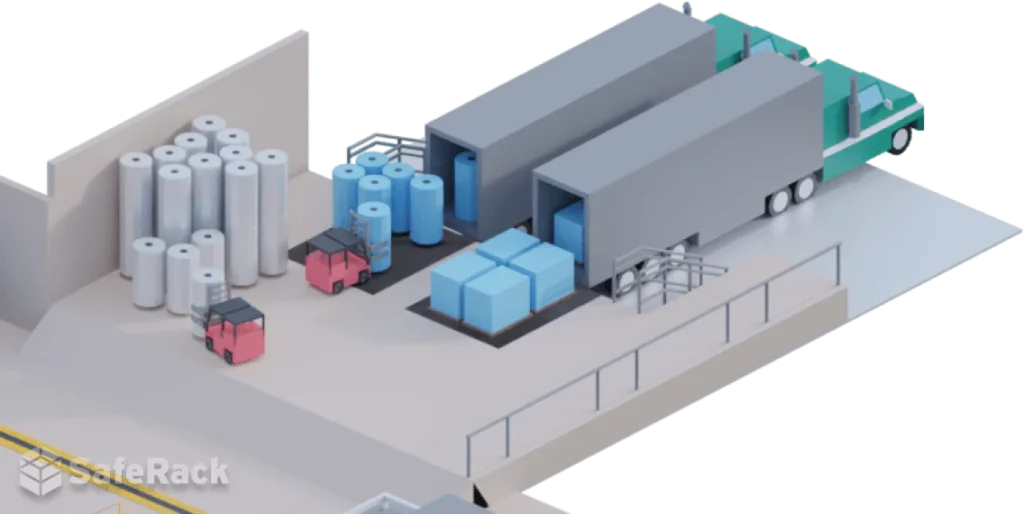
Pulp and paper mills are often required to ship a broad range of products. This can include bulk rolls, various size reams of paper, specialty paper products, and even pulp since some paper manufacturers do not produce pulp but source it from mills.
Pulp can be shipped wet or dry in either pressed bales or rolls but precautions must be taken to ensure that pulp does not get too wet during shipping. Excess moisture can damage the pulp and cause discoloration. Drainage can also damage other cargo on board.
Pulp and paper mills require safe and efficient loading and unloading solutions to meet unique shipping challenges. Awnings and canopies can help protect pulp and paper and workers from the elements during loading and unloading. Loading platforms and dock stairs give workers safe and efficient access to trucks and railcars, while safety gates and safety cages offer fall protection.
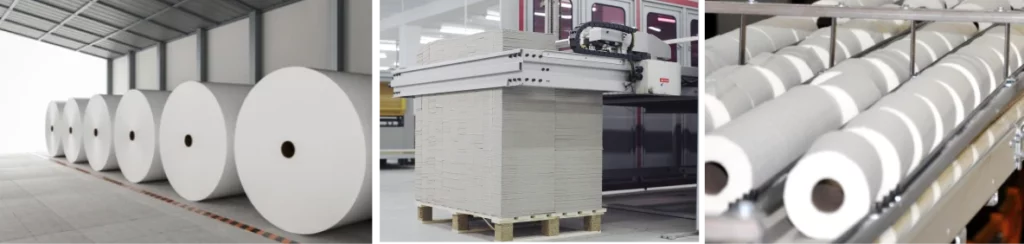
Utilities
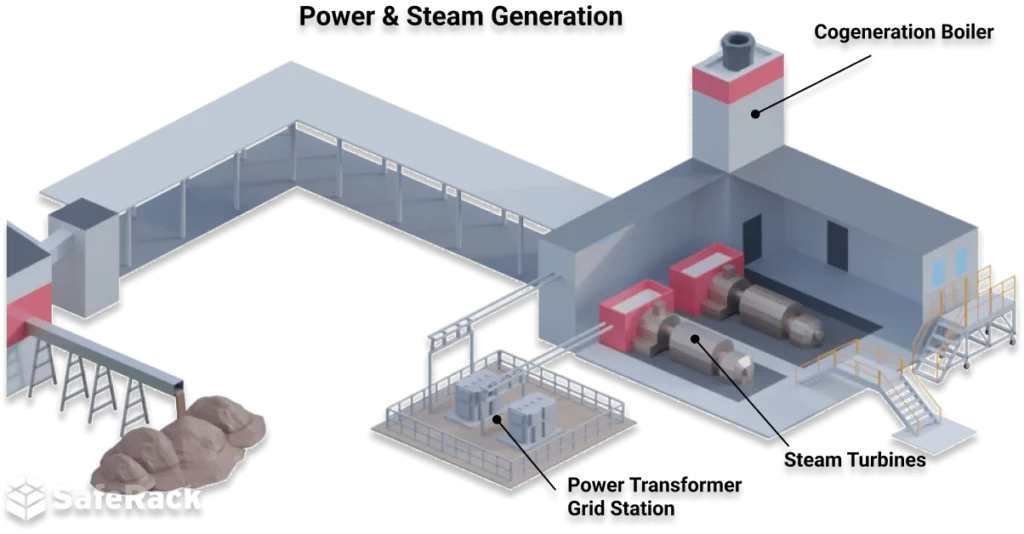
Pulp and paper mills require a massive amount of energy to process wood into pulp and pulp into paper products. These energy sources must be sustained all day, every day to ensure productivity and efficiency.
Steam plays a key role in many pulp and paper processes. It is used to separate fibers and soften pulp. It is used in bleaching and mixing oxygen into the pulp. And it helps evaporate moisture from pulp and to prepare wastewater for reuse.
Plants and mills that use cogeneration boilers can utilize exhaust energy from gas turbines to produce steam. The steam can be used for additional energy production with no additional fuel consumption. This process helps reduce energy costs, conserve energy, reduce emissions, and ensure a reliable energy stream.
A cogeneration boiler is responsible for recovering combustion gases and transforming them into thermal energy through steam and power, which is then used for self-consumption. Cogeneration boilers can also be equipped with economizers and afterburners to preheat the water that feeds them.
Post Treatment
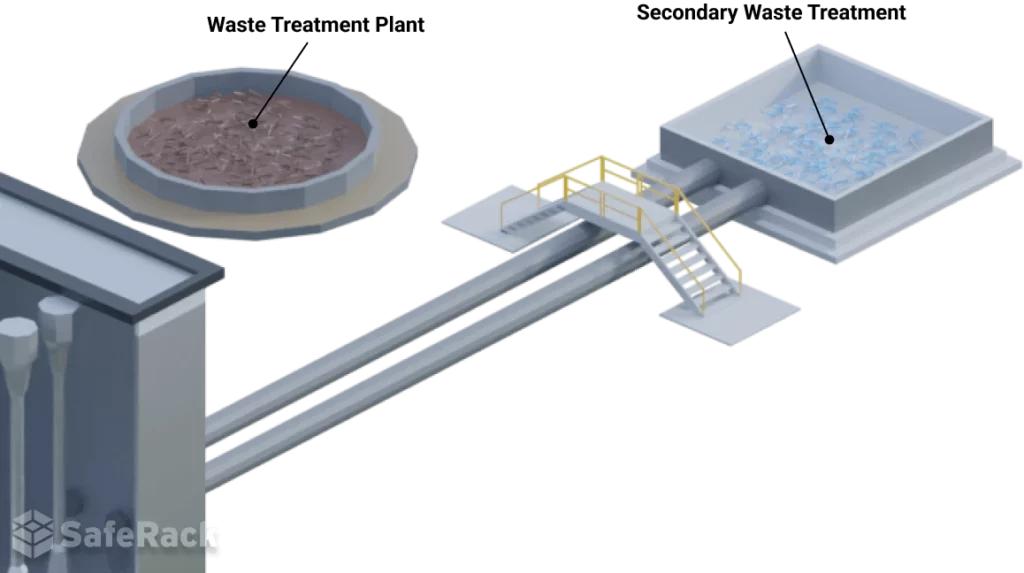
The paper and pulp industry is one of the largest industrial users of water resources in the world. With water being used in almost every step of the manufacturing process, pulp and paper mills require an average of approximately 54-70 m3 (18,000 gallons) of water per metric ton (2,200 pounds) of processed paper goods.
These processes also produce large amounts of wastewater and residual sludge. Approximately 80% of the wastewater includes suspended solids, trace heavy metals, recalcitrant chlorinated organic compounds, biological oxygen demand (BOD), and bacteria, among others. Given the environmental implications, pulp and paper mills must prioritize advanced wastewater treatment processes to prepare wastewater for environmentally safe discharge or reuse.
There are many methods that are used to separate solids from effluents. Sedimentation is the simpliest of these methods. Solids suspended in the effluents settle in sedimentation tanks and the settled sludge is removed. Biological waste water treatment works by degrading pollutants through the actions of micro-organisms.
Pulp and paper mills often utilize a combination of wastewater treatment technologies and methods. For instance, biiological treatment has been used with tertiary treatment such as advanced oxidation, activated carbon, and membrane treatment systems to produce high quality water that can be reused in manufacturing processes. Treated wastewater can also be used to potentially recharge aquifers, which is particularly important in coastal areas where saltwater intrusion of ground water is an issue.
Pulp and Paper Mill Safety Reminders
Here are the four leading areas of concern regarding pulp and paper mill safety:
Noise Hazard Reduction
Noise-induced hearing loss is one of the most prevalent occupational health hazards facing American workers, affecting approximately 30 million people at their worksites each day. Papermill employees are among those workers regularly exposed to extremely harmful levels of noise for prolonged periods of time.
While noise-induced hearing loss is irreversible, it is preventable and its risk can be reduced via the application of noise controls and occupational hearing loss prevention programs.
In addition to frequently monitoring your plant’s noise levels, you should also utilize low-noise machinery and noise barriers. You must also provide effective ear protection for your workers, implement a safety program focused on PPE compliance, and keep abreast on all emerging noise-reduction solutions.
Chemical Hazard Prevention
The paper and pulp industry consumes a huge amount of wood, water, and other resources each year, creating significant amounts of solid waste and wastewater that must be treated.
Paper mills also use a wide range of substances that are hazardous to employees’ health, as well as dangerous to your surrounding communities. The substances include sulfuric acid, chlorine, chlorine dioxide, and other gaseous sulfur compounds.
These chemical hazards should be handled in multiple ways.
For starters, proper labeling and storage are essential, as is the use of spill berms and spill containment pallets. Properly marked shower and eyewash locations should also be located in each employee workstation
Workers must not handle any chemicals without appropriate PPE. The PPE must be in good condition and fit properly in order to provide appropriate protection. Employees must also be provided with replacement PPE as its condition deteriorates.
Equipment-related hazards can pose significant risks to your employees, as well as considerable fines for your company.
Workers may be struck or crushed by falling, rolling, or sliding pulpwood loads or suffer lacerations, amputations, or worse from the misuse of equipment — especially if it’s used improperly or without proper safeguards.
Employees should not work on machines lacking proper safeguards. All guards must be inspected on a regular basis so that issues can be spotted and worked stopped until safety problems can be resolved.
Also, strict protocols should be followed for shutting down equipment during maintenance and repairs. Proper lockout/tagout processes must also be employed in order to control hazardous energy when traditional controls have been removed or briefly disabled.
OSHA-compliant fall protection must be used when loading and unloading flatbed trailers, and other safety enhancements like customized work platforms, durable guardrails, and metal handrail systems that can further bolster the safety of your mill by improving stability, ergonomics, and productivity in and around equipment.
Human Error Prevention
While your employees don’t try to become injured on the job, human factors like fatigue, distraction, and working on auto-pilot can significantly increase the likelihood and risk of accidents.
Training your workers to be aware of these conditions and counteract them will help them prevent mistakes, such as overlooking lockout/tagout steps and other vital procedures before, during, or at the end of their shifts.
These training programs will also help them identify and report unsafe work conditions, as well as help keep each other safe in the event coworkers forget to follow safe work practices.