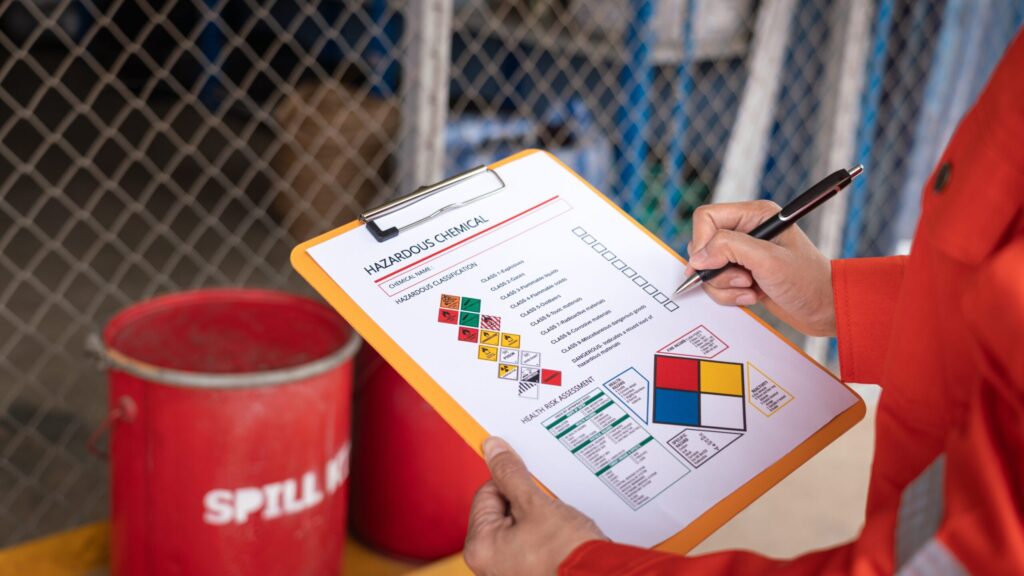
In the manufacturing industry, chemical safety ensures worker well-being while maintaining operational efficiency. With hazardous substances at play, it’s essential to implement appropriate safety measures to minimize risk without impacting production. This article covers key aspects of chemical safety and outlines essential safety guidelines.
Key Points You’ll Learn:
- Common Chemical Hazards: Understand the primary risks in chemical manufacturing, including chemical exposure, fire, spills, equipment failure, and fall risks.
- Safety Guidelines: Learn essential safety measures such as proper labeling, PPE use, chemical compatibility, and emergency preparedness.
- Fall Prevention: Explore how gangways, platforms, and anti-slip products enhance worker safety around hazardous substances.
- Spill Containment: Discover products to manage chemical spills and leaks to prevent contamination and exposure.
- SafeRack Solutions: See how SafeRack’s products, like gangways and spill containment systems, improve chemical safety and regulatory compliance.
The Importance of Chemical Safety
Manufacturing facilities in the chemical industry utilize dangerous chemicals, from solvents and acids to gases and flammable materials. These substances pose various risks to operators and visitors, including exposure to toxic fumes, skin contact with corrosive materials, and the potential for explosive reactions. Ensuring chemical safety is not just a regulatory requirement but a moral imperative to protect workers from harm.
Common Hazards in Chemical Manufacturing
Chemical manufacturing presents several hazards that require careful management. Among the most significant are:
- Chemical Exposure: Inhalation, ingestion, or skin contact with hazardous chemicals can lead to acute or chronic health issues, including respiratory problems, chemical burns, or poisoning.
- Fire and Explosions: Flammable chemicals and volatile substances can ignite or explode if not handled properly, causing severe injuries or fatalities.
- Spills and Leaks: Accidental spills and leaks can lead to contamination, slip hazards, and exposure to toxic substances.
- Equipment Malfunction: Faulty or improperly maintained equipment can release hazardous chemicals or fail to contain them, leading to exposure risks.
- Falls and Slips: Working around chemicals often requires accessing elevated areas or navigating slippery surfaces, increasing the risk of falls and related injuries.
General Chemical Safety Guidelines
To mitigate the risks associated with chemical manufacturing and ensure the safety of employees, companies should implement the following comprehensive safety practices:
Labeling and Storage: All chemicals should be labeled accurately and stored according to compatibility guidelines to prevent dangerous reactions.
Personal Protective Equipment (PPE): Workers should be equipped with appropriate PPE, including gloves, goggles, and lab coats, to safeguard against exposure to hazardous chemicals.
Safety Data Sheets (SDS): Keep SDS accessible for every chemical in the facility. These sheets provide critical information on hazards, safe handling, and emergency procedures.
Chemical Compatibility: Understand chemical interactions to prevent accidental reactions. Properly segregate incompatible chemicals during storage and use.
Training and Emergency Preparedness: Regular training on chemical safety protocols and emergency procedures, such as spill response, ensures workers are prepared for potential incidents.
Waste Disposal: Adhere to correct hazardous waste disposal methods to protect the environment and comply with regulations.
Products that Enhance Chemical Safety
There is a range of products designed to improve safety in chemical manufacturing facilities. These solutions can help address key safety challenges, particularly in fall prevention and safe chemical handling.
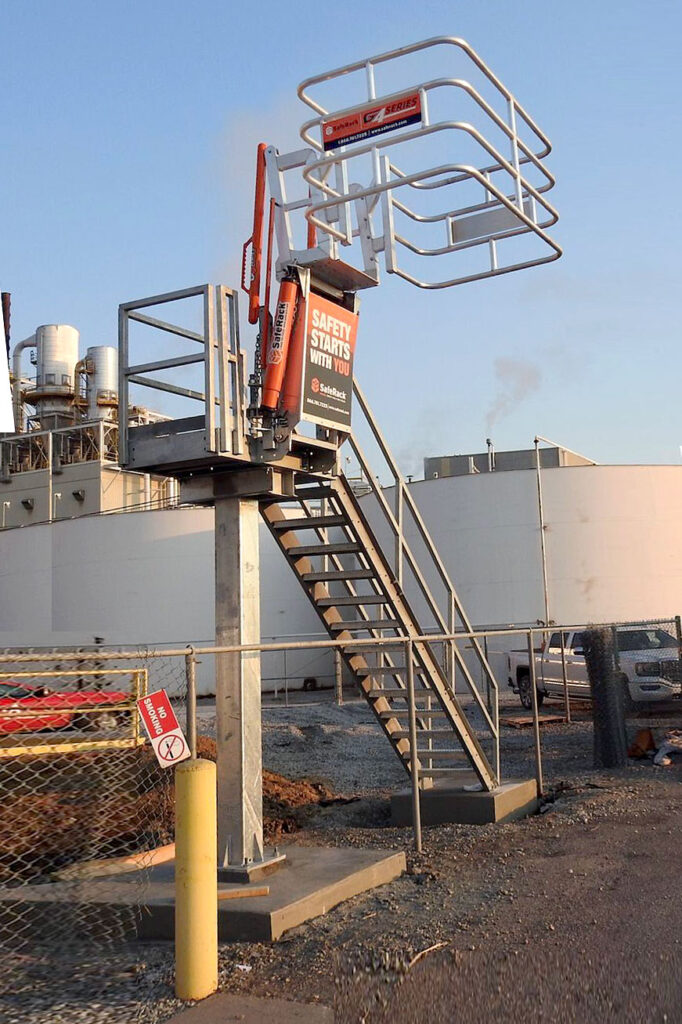
Gangways and Platforms: Gangways and platforms provide safe access to trucks, railcars, and other elevated work areas. With features like self-leveling stairs and adjustable platforms, these products reduce the risk of falls while ensuring secure footing for workers handling chemicals.
Safety Cages and Handrails: Safety cages and handrails are designed to prevent falls from elevated surfaces, offering additional protection in areas where chemicals are used or stored. These structures can be customized to fit specific work environments and are built to withstand harsh chemical conditions.
Spill Containment Solutions: Spill containment systems, including track pans and spill berms, help contain leaks and spills, preventing them from spreading and reducing the risk of exposure and environmental contamination.
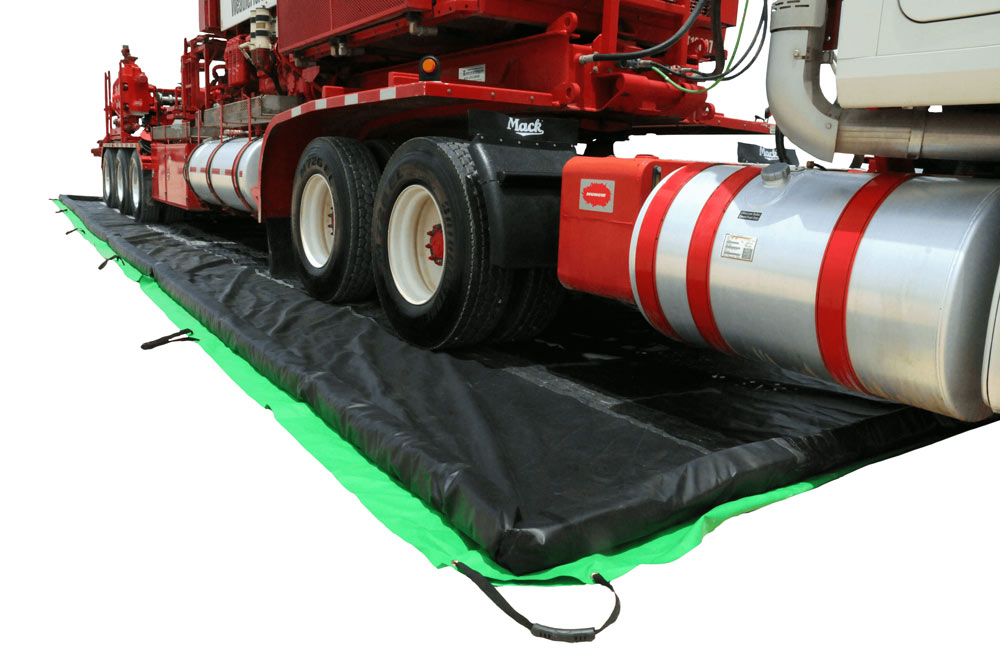
Anti-Slip Products: Anti-slip products, such as treads and coatings, are essential for preventing slips and falls in areas where chemicals are present. These products are designed to maintain traction, even in wet or oily conditions.
Conclusion
Chemical safety in manufacturing is essential for protecting workers and maintaining a safe work environment. By following best practices to keep employees and visitors safe on site and utilizing safety solutions, manufacturing companies can significantly reduce the risks associated with chemical hazards. Whether through fall prevention, proper chemical handling, or emergency preparedness, prioritizing safety ensures that manufacturing processes remain efficient and accidents are minimized.
Investing in the proper safety equipment and protocols protects workers and helps companies comply with regulatory standards and avoid costly incidents. SafeRack is committed to providing the tools and solutions necessary to support these efforts, making chemical manufacturing environments safer for everyone.
Ensure your facility is fully equipped to handle chemical hazards safely. Contact a SafeRack representative to explore our range of spill containment solutions, gangways, and anti-slip products designed to protect workers and maintain compliance with safety regulations.