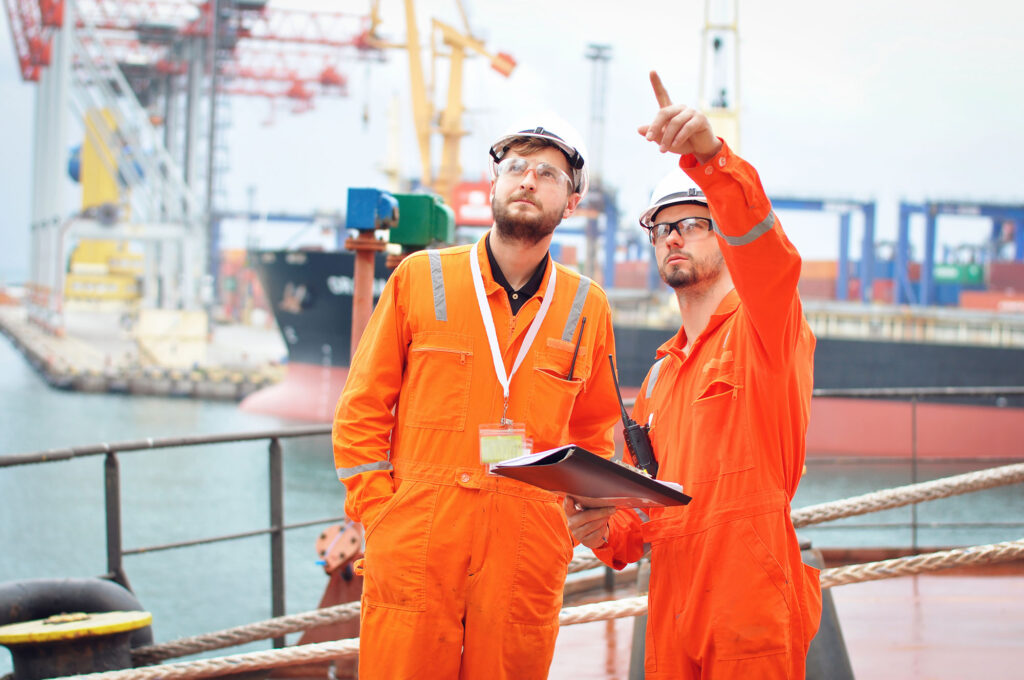
A strong safety culture is the backbone of any industry-leading organization. It not only reduces accidents but also enhances productivity, employee morale, and overall business success. Let’s explore key lessons from industry leaders on enhancing the safety culture within an organization.
- Leadership Commitment: Companies like Alcoa demonstrate that leadership commitment is the cornerstone of a strong safety culture. Former Alcoa CEO Paul O’Neill famously prioritized worker safety above all else, and this top-down approach resulted in not only an outstanding safety record but also financial success. Leadership commitment sets the tone for the organization, making safety a core value rather than an afterthought.
- Continuous Learning: Leaders in safety like ExxonMobil see accidents and near-misses as opportunities for learning and improvement rather than isolated incidents. They conduct thorough incident investigations to identify root causes and systemic issues, and they share these learnings openly to prevent future occurrences.
- Employee Engagement: Companies like DuPont involve employees at all levels in safety activities – from hazard identification to safety training development. This engagement gives employees a sense of ownership over safety procedures, making them more likely to follow and improve upon them.
- Holistic Approach: BASF, a leading chemical company, integrates safety into all aspects of their business, from research and design to manufacturing and distribution. They understand that safety is not just about personal protective equipment (PPE) or isolated procedures; it’s about considering safety at every stage of the process.
- Robust Communication: At British Petroleum (BP), effective safety communication is a priority. This includes not just top-down communication, but also fostering an environment where employees feel comfortable voicing their concerns or suggestions related to safety. Robust communication ensures everyone understands their roles and responsibilities in maintaining a safe work environment.
- Ongoing Training: Toyota, a pioneer in manufacturing safety, emphasizes ongoing safety training. Rather than treating training as a one-time event, it’s seen as an ongoing process that keeps safety at the forefront and adapts as procedures, technologies, or workforce change.
- Performance Metrics: Companies like Shell don’t just track lagging indicators like incident rates; they also track leading indicators such as safety audits, training completion, and employee engagement in safety activities. This forward-looking approach allows them to preempt potential safety issues.
With ever-increasing health and safety regulations, the potential for hazardous incidents in today’s workplace has never been more of an issue. When it comes to chemical loading operations associated with bulk railcars, fall protection is a key priority for safety inspectors due to the high risks involved.
SafeRack is the recognized industry leader in truck and railcar loading platform systems, maintenance work platforms, rolling platforms, and related safety and fall protection products. To learn more about our products and how we can help keep your workplace safe, contact a member of our team today.