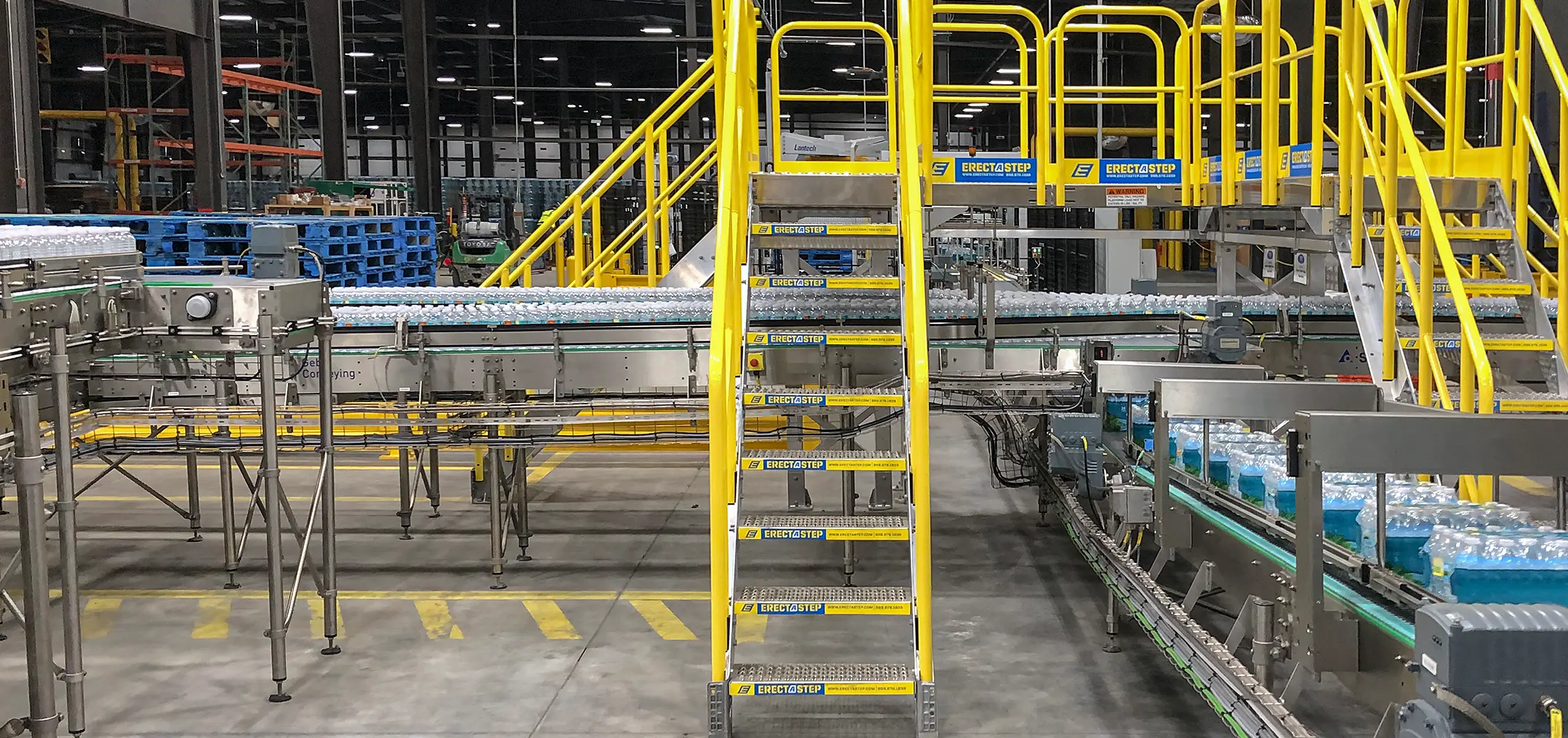
Food & Beverage
Safe, Efficient Access Systems for Food & Beverage Operations
Enhancing Safety, Efficiency & Compliance in Food & Beverage Operations
The food and beverage manufacturing industry requires safe, efficient, and compliant solutions to protect workers and maintain product integrity. SafeRack provides OSHA-compliant food industry platforms, gangways, and modular access solutions designed for food-grade applications, ensuring smooth operations while minimizing contamination risks. As North America’s #1 distributor of OPW and Emco Wheaton Loading Arms, we deliver trusted food manufacturing equipment solutions for everything from dairy processing to liquid chocolate and water bottling plants.
- Safe Access & Fall Protection – Slip-resistant platforms, safety gates, and secure gangways reduce worker risks, meeting fall protection requirements for food manufacturing workers in food and beverage facilities.
- Regulatory Compliance – Equipment designed to meet OSHA, FDA regulations for food handling equipment, and USDA standards for sanitary and safe food and beverage processing.
- Operational Efficiency -ErectaStep modular access solutions and ergonomic workstations improve workflow and reduce facility downtime, addressing food & beverage manufacturing challenges.
- Cross-Contamination Prevention – Stainless steel and food-grade materials ensure sanitary handling of ingredients and food manufacturing equipment to meet industrial food manufacturing equipment standards.
- Customizable Solutions – Modular stairs, work platforms, and crossover systems accommodate a range of commercial food manufacturing equipment needs, from beverage manufacturing facilities to bulk ingredient handling.
- Trusted Industry Expertise – SafeRack’s experience in the food manufacturing industry ensures reliable, long-term safety solutions tailored for food and beverage manufacturing equipment applications.
Food & Beverage
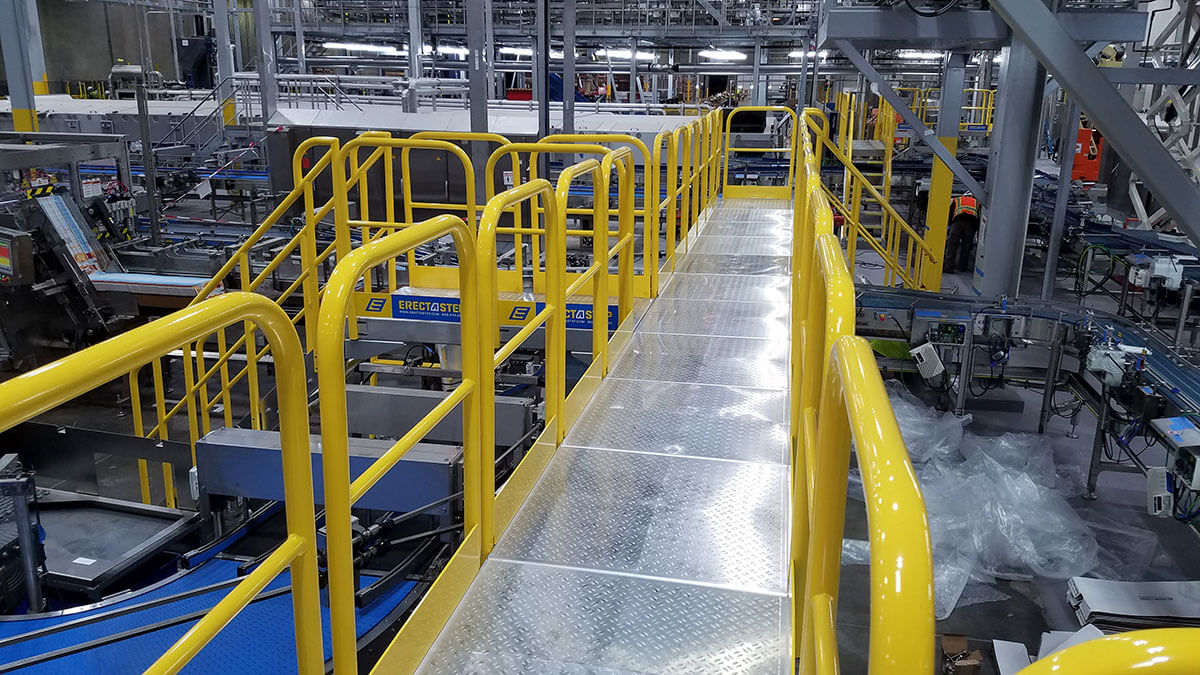
Streamlined Safety and Compliance for More Productive Worksites
Keeping Food & Bev Facilities Safe & Productive
From loading docks to processing plants, safety and efficiency go hand in hand in food and beverage manufacturing. SafeRack provides solutions that help businesses protect workers, streamline operations, and maintain compliance. Whether handling bulk liquids like dairy or liquid chocolate or ensuring safe worker access around processing lines, our modular safety systems are built to support productivity while reducing risks.
- Modular stairs and work platforms for sanitation and maintenance access
- Fall protection and access solutions for loading docks and transport areas
- OSHA-compliant crossover platforms to improve workflow and worker safety
Safe food and beverage manufacturing practices are crucial to your organization’s bottom line and the people who consume your products and the workers who produce them.
Meeting the Demands of the Booming Ready-to-Drink Market
Consumer preferences are shifting rapidly, and the Ready-to-Drink (RTD) beverage sector continues to grow at an unprecedented rate. Alcohol-based RTDs, including hard seltzers and craft spirit-branded drinks, are capturing market share across diverse demographics. This surge in demand places increased pressure on manufacturers to optimize operations and ensure safe, efficient production environments.
- SafeRack solutions support high-volume beverage production with secure loading and unloading platforms
- Modular systems that adapt to changing facility needs as production scales
- Anti-slip and corrosion-resistant materials designed for beverage manufacturing environments
Supporting Growth While Prioritizing Safety
The food and beverage industry is expanding beyond consumer products, with companies producing essential ingredients for emerging markets like renewable fuels. As supply chains shift and production scales up, ensuring worker safety remains a top priority. SafeRack helps facilities stay operational and compliant by reducing hazards and improving efficiency with adaptable safety systems.
- Customizable safety solutions for high-demand processing facilities
- Enhanced fall protection and ergonomic access to reduce workplace injuries
- Reliable safety equipment that keeps workers protected and production on track
Safe food and beverage manufacturing isn’t just about compliance—it’s about keeping workers safe, ensuring quality, and sustaining long-term productivity. SafeRack provides the solutions to make that happen.
Products
Semi Trailer & Truck Steps
Semi-truck steps for loading semi and flatbed trailers
Crude oil sample catchers and oil thieves
We offer Tulsa Oil Thieves in three models and five sizes. All of the sample catchers feature single trip (original with the Tulsa Thief), antifouling flat-ball assembly, a full opening horizontal closure system with rotating valve, two adjustable springs (one for closing tension and one for tripping tension for more flexible adjustment) and adjustable graduated trip rods that hold the thief in an upright position as a hydrometer cylinder.
Loading Dock Stairs
Prefabricated IBC, ADA, or OSHA Aluminum Loading Dock Steps that bolt together in about an hour.
Drench Showers
Emergency Drench Showers and Safety Eyewash Stations
Pipe Racks
Prefabricated Pipe Racks Constructed Faster and Easier Than Ever Before
Tools and Loading Accessories
A comprehensive range of facility and loading terminal equipment, accessories and safety solutions.
Grounding & Monitoring
Protect personnel, product, and terminals with static grounding (earthing) solutions
Safety Gates
Industrial safety swing gates, facility guardrails, mezzanine gates and barriers gates.
Spill Containment
Spill Containment
Top Loading Arms
Top Loading Arms
Loading Arms & Couplings
Loading Arms & Couplings
Portable Access Platforms
SafeRack’s MAUI mobile access units provide secure, adjustable stair solutions for safely accessing elevated truck and railcar work areas, even in the most challenging environments.
MaxRack Elevated Platforms
Powered elevating platform system for accessing railcars and trucks
Gangways
Truck, Railcar and Marine Gangways, Safety Cages, and Inspection Services
Stairs & Work Platforms
Fixed and Mobile Access Stairs, Work Platforms, Crossover Stairs, Rolling Stairs & Mobile Platforms, Roof Stairs and Access, Ship Ladder
Solutions
Loading & Safety Solutions for Food and Beverage Manufacturing Facilities
SafeRack provides food-grade loading platforms and sanitary loading systems for food processing designed to enhance safety, efficiency, and compliance in food and beverage manufacturing operations. Our team works closely with each facility to develop customized solutions that meet OSHA-compliant food industry standards while addressing bulk liquid transfer safety in food manufacturing.
Whether supporting food manufacturing equipment in a beverage manufacturing facility or providing spill containment for food processing plants, SafeRack delivers safe, reliable, and regulatory-compliant solutions to keep operations running smoothly.
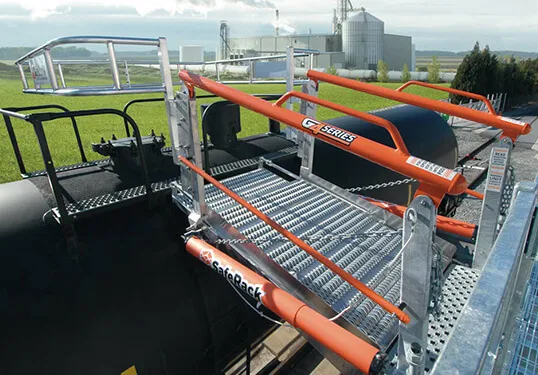
Loading Gangways
Since rail cars have off-set crash boxes SafeRack recommends a wider telescoping access gangway (48″-60″ is preferable) as it helps improve access and egress to and from the railcar. In addition, a wider gangway will reduce the risk of the operator’s PPE getting caught, torn or damaged, and will improve productivity and safety. Powered gangway solutions are also an option, with both hydraulic and pneumatic solutions being commonly used.
Each gangway will be fitted with a two-rail safety cage for the railcar crash box. This will be a centered 7’6”x 6’ safety cage to sit directly over the cashbox; and will provide a safe, secure work environment for your operator when accessing hatches on railcars.
For tank truck applications (loading or unloading) SafeRack’s standard 24” wide Self-Adjusting (SAS) gangway with a deeper 4’x6’x4-rail safety cage would be the preferred solution.
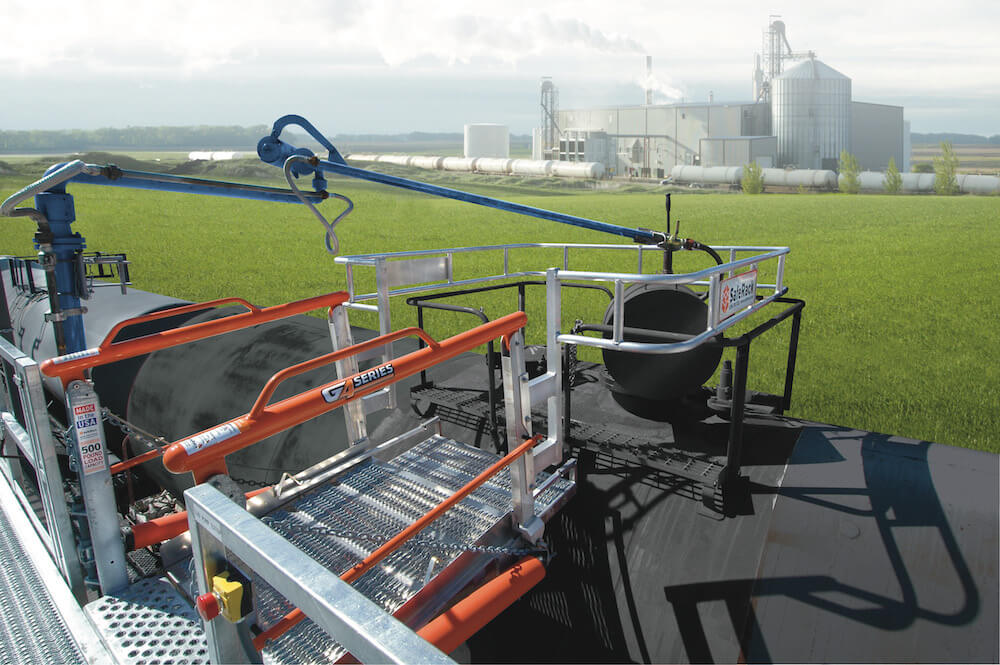
Loading Arms
Product can be splash loaded into railcars and tank trucks via loading arms or chemical hoses. The current best loading practice is to use a 3″ carbon steel or stainless steel arm for tank trucks with PTFE or ChemRaz seals. Vapor recovery is optional and is used in conjunction with a splash plate, vapor cone, or inflatable hatch seal.
Railcar loading will use a similar setup as trucks but with a 4” arm as higher flow rates must be obtained to load the higher capacity vehicles at an acceptable rate.
The loading arms layout will ensure that it is self-draining after use as to completely evacuate product when the arm is stored to reduce product leakage which could injure passer-bys and corrode platform, support, and process piping located on the rack. Safety options such as high-level sensors/probes can be added to the arm to switch off loading should the level hit a predetermined height in the vehicles.
Example of gravity fed top loading arm:
Example of gravity fed top loading arm
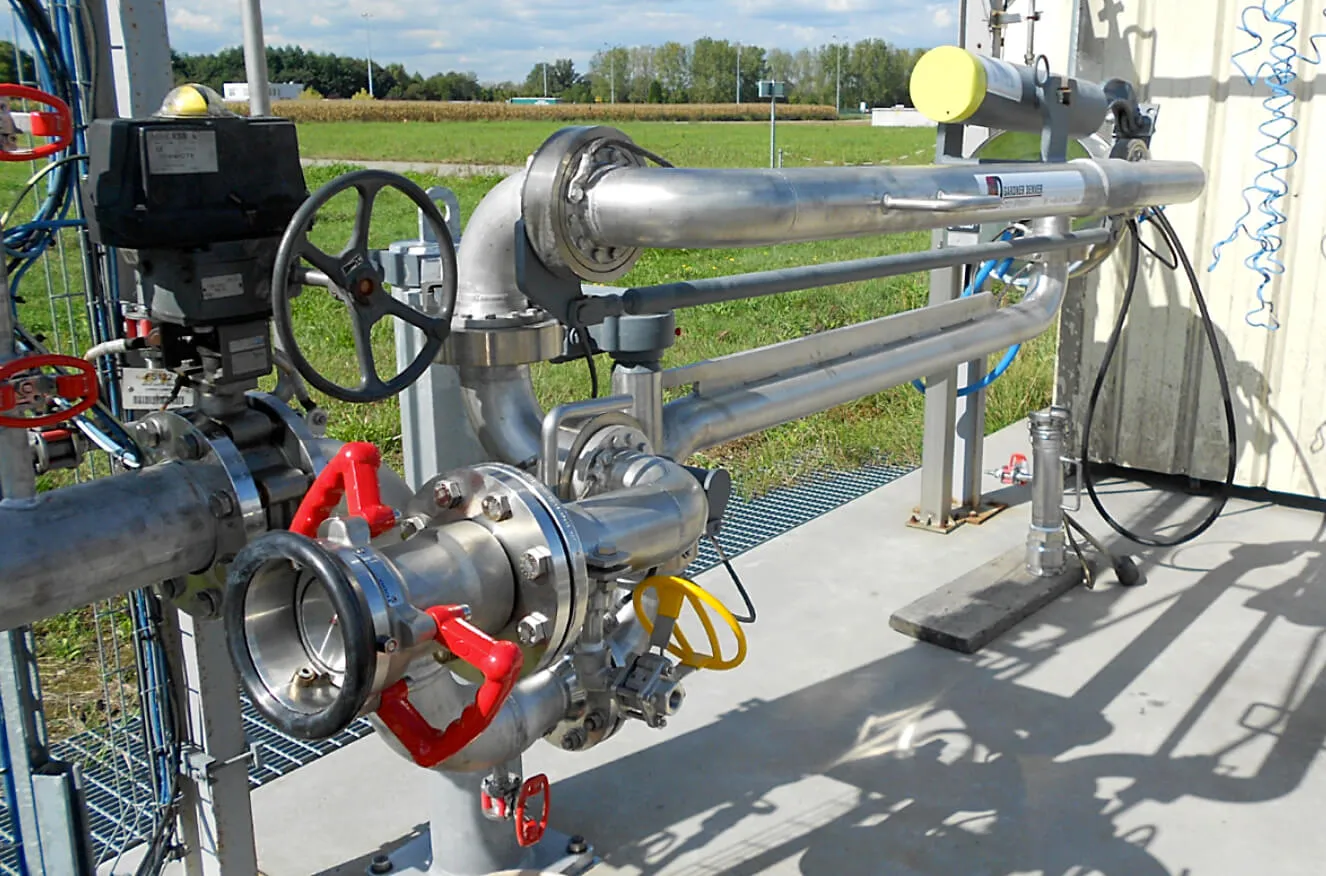
These are generally 4”, carbon steel, ANSI 150Lb rated loading arms, that will be fitted with quick-couplings and an emergency break-away unit. The arm itself will be fitted to a support stand post and will be self-draining in design.
We would also recommend that the arm be fitted with a parking latch and parking sensor to ensure that the arm is stored in a safe place when not in operation.
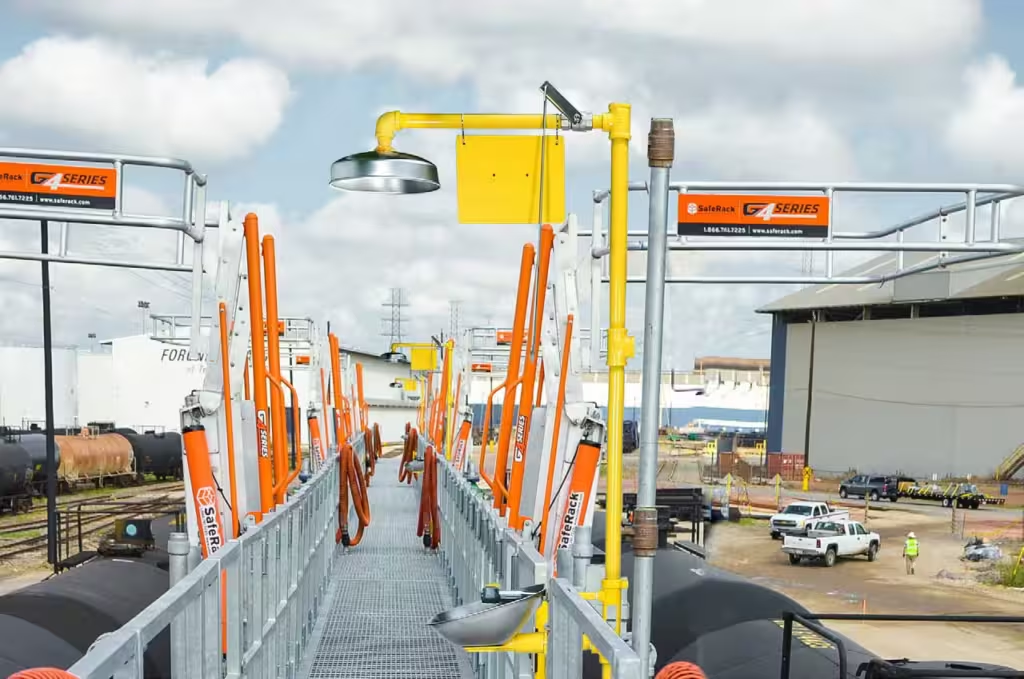
Eye Wash/Drench Showers
ANSI guidelines state that an Eye Wash/Drench Showers need to be located 10 seconds or 55′ (16.8m) from contaminants or hazardous materials. Eyewash stations need to be on the same horizontal plane with no obstructions.
Therefore, we would propose the installation of a standard combination Drench Shower/Eyewash Unit, which will save limited space and fit easily into any work environment.
This is a fundamental safety requirement for any loading or unloading station.
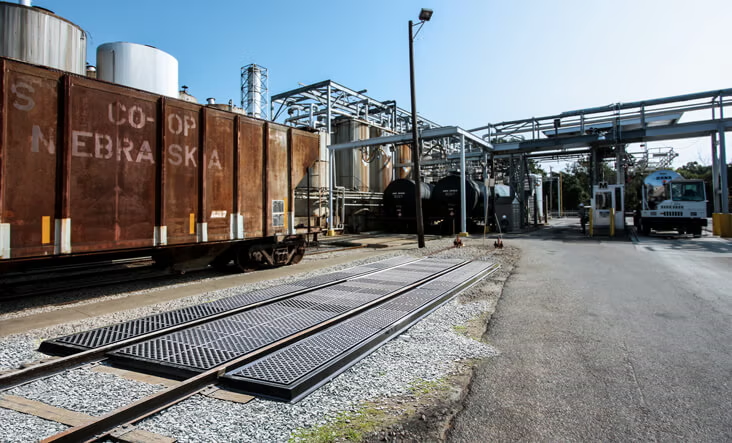
Spill Containment
Spill containment pans will be provided at the point of loading operations and are an essential piece of equipment in overall site safety and environmental protection. SafeRack recommends a minimum 20’ long galvanized, polyethylene or composite track pan to mitigate spills.
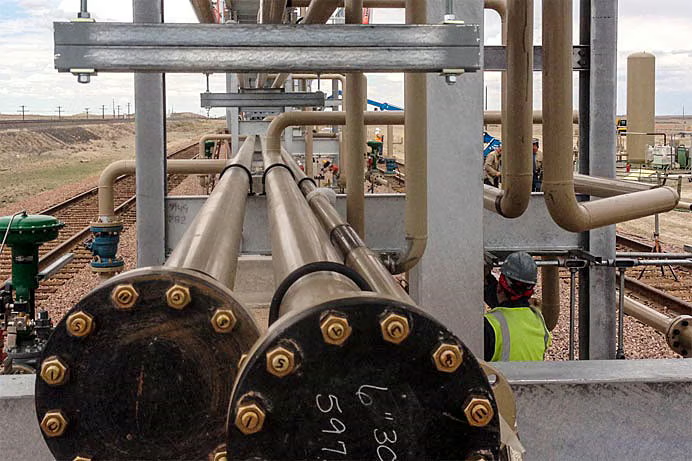
Piperacks
Because wastewater treatment plants have pipe runs throughout the facility, ErectaRack pipe racks are pre-fabricated for a variety of pipe dimensions and applications. Because they’re pre-engineered, ErectaRack skips the long engineering and fabrication process, saving weeks, if not months in the installation process.
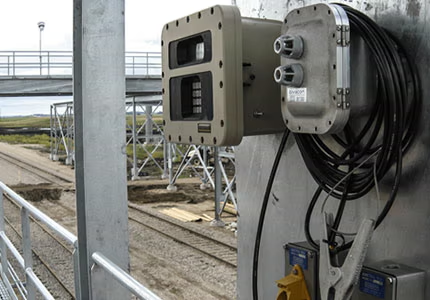
Grounding
Many food or pharma products are not flammable, industry best practice includes the grounding of all vessels before starting the (un)loading process.
Explosion-proof enclosures — meet or exceed UL, CSA, and Ex requirements
Vehicle grounding and bonding — ensure true grounding before product flow is permitted
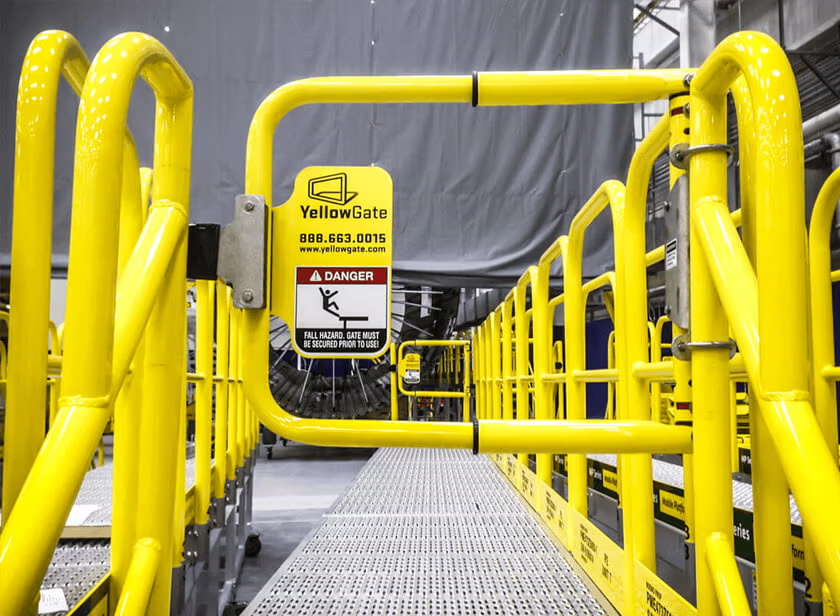
Safety Gates, Stairs, Ladders, & Platforms
Safety Gates will be installed at the top of the stairs and any other openings to ensure operator safety.
SafeRack’s line of industrial safety gates is the most flexible product on the market with the ability to span openings between 16” and 36” and is field adjustable with nothing more than a wrench. We also have guardrails, metal handrails, and full-fledged fall protection solutions with customizable options to fit your needs.
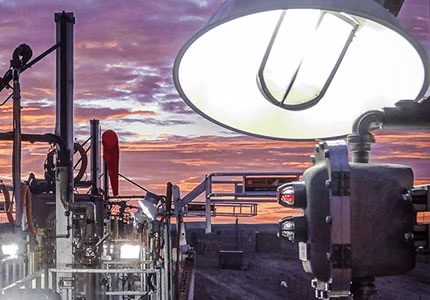
Loading Platform Options
Lighting – General exterior and task lighting to illuminate work and walk areas.
Platform & Canopies – Full platform canopies reduce exposure to the elements and improve the safe and productive loading operation from the operator’s perspective.
Operator Shelter—Depending on your site requirements, consider the requirement of an operator or guard building to keep personnel out of the elements. This can be customized to meet specific site requirements.
Wheel Chocks – SPCC options to allow for safe access and storage of water treatment chemicals.
Keeping Food and Beverage Facilities Safe and Productive
Maintaining high safety standards is essential to protecting both workers and consumers while ensuring uninterrupted operations in the food and beverage manufacturing industry. Achieving compliance requires a commitment to sanitation protocols, proper equipment use, routine maintenance, and comprehensive employee training to meet FDA regulations for food handling equipment and OSHA-compliant food industry platforms standards.
- All employees, supervisors, and managers must follow strict fall protection requirements for food manufacturing workers and workplace safety guidelines.
- Subcontractors and suppliers should meet the same safety expectations, ensuring food manufacturing equipment and handling processes adhere to industry regulations.
- Regular safety audits, spill containment for food processing plants, and equipment inspections help prevent hazards and maintain compliance.
Failure to uphold safety standards can lead to costly recalls, production downtime, and serious risks to worker and consumer health. Investing in reliable safety solutions not only protects your workforce but also enhances bulk liquid transfer safety in food manufacturing, improves operational efficiency, and ensures long-term success.
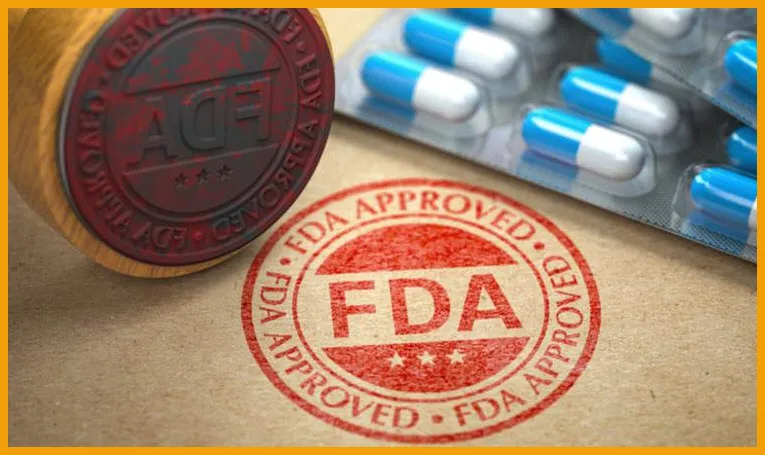
Key Safety Considerations in Food Manufacturing
Sanitation
According to the Food and Drug Administration (FDA), poor plant sanitation is one of the biggest factors contributing to food contamination. Food products can become contaminated at any time before, during, or after processing.
Sanitation procedures — including equipment disassembly procedures and methods used — must be documented, as well as the time required, types and amounts of chemicals used, and water temperatures.
All aisles and working spaces should be unobstructed and wide enough to allow employees to perform their jobs and protect against contamination. During processing, employees must use the proper protective products (like gloves, hairnets, and face masks) to prevent contaminating work areas and food, as well as to protect themselves from any bacteria or other pathogens they may come into contact with. There should be adequate drainage of all outside areas that may contribute to contamination, as well as proper spill containment solutions in place to decrease the chances of a spill and mitigate the damage after one.
Equipment Access and Use
Not only must all employees understand and follow equipment guidelines, but no workers should be allowed to operate any machinery without being properly trained on how to use it. Take, for instance, handling hot chocolate to make chocolate-covered treats. Our solution allows temperature control and visual acuity of the hot chocolate via temperature sensors — at the elbows and swivel joints — hard-wired to a Programmable Logic Control (PLC) system. These sensors are then linked to the plant automation system. Truly, we offer a holistic approach that treats the product like liquid gold.
In addition to wearing appropriate safety gear, employees should also avoid wearing any clothing or jewelry that could get caught in machinery. Such incidents can damage equipment, cause workers to become entrapped, and/or result in loose items entering and contaminating food during processing. With this in mind, it is imperative that machine guards are in place during operation and that employees know where to find and activate emergency shut-off switches in the event of an emergency.
Of course, providing workers with safe access to, from, and around the equipment is just as important as them using equipment safely. Not only should aisles and workspace be clear, but proper slip, trip, and fall prevention measures (including warning signs and hazard notifications) should also be in place.
Ergonomically designed gangways and loading racks boost employee and productivity during bulk loading, while crossovers allow workers safe and clear access over conveyor lines, as well as to and from other equipment.
Maintenance
Improper maintenance can lead to damaged equipment, compromised products, and injured or ill employees.
Broken seals can allow unwanted chemicals to seep into your products. Forklifts and other vehicles can expose and damage wires and cables, creating trip hazards. Dull blades can slip and cause jams. Worn-out belts can snap, contaminating food and harming employees.
Preventing these and other maintenance issues will protect both your manufacturing process and your employees.
In addition to keeping equipment clean during use, regular maintenance procedures — like making sure no cable or wires are frayed, or that all chemicals are labeled and used properly — must be followed.
Note: Only qualified personnel should be allowed to service or maintain equipment.
Food Security
Food products aren’t always contaminated as a result of poor sanitation or an accident. Sometimes, they are tampered with by bad actors via chemical, biological, or radioactive means.
Proper measures must be taken to maintain the integrity of your food chain.
While there are no guarantees when it comes to safety or preventing incidents, you can decrease the likelihood of tampering by employing various safety measures, including fencing, security cameras and teams, metal detectors, open floor plans, and controlled entrances to your facilities.