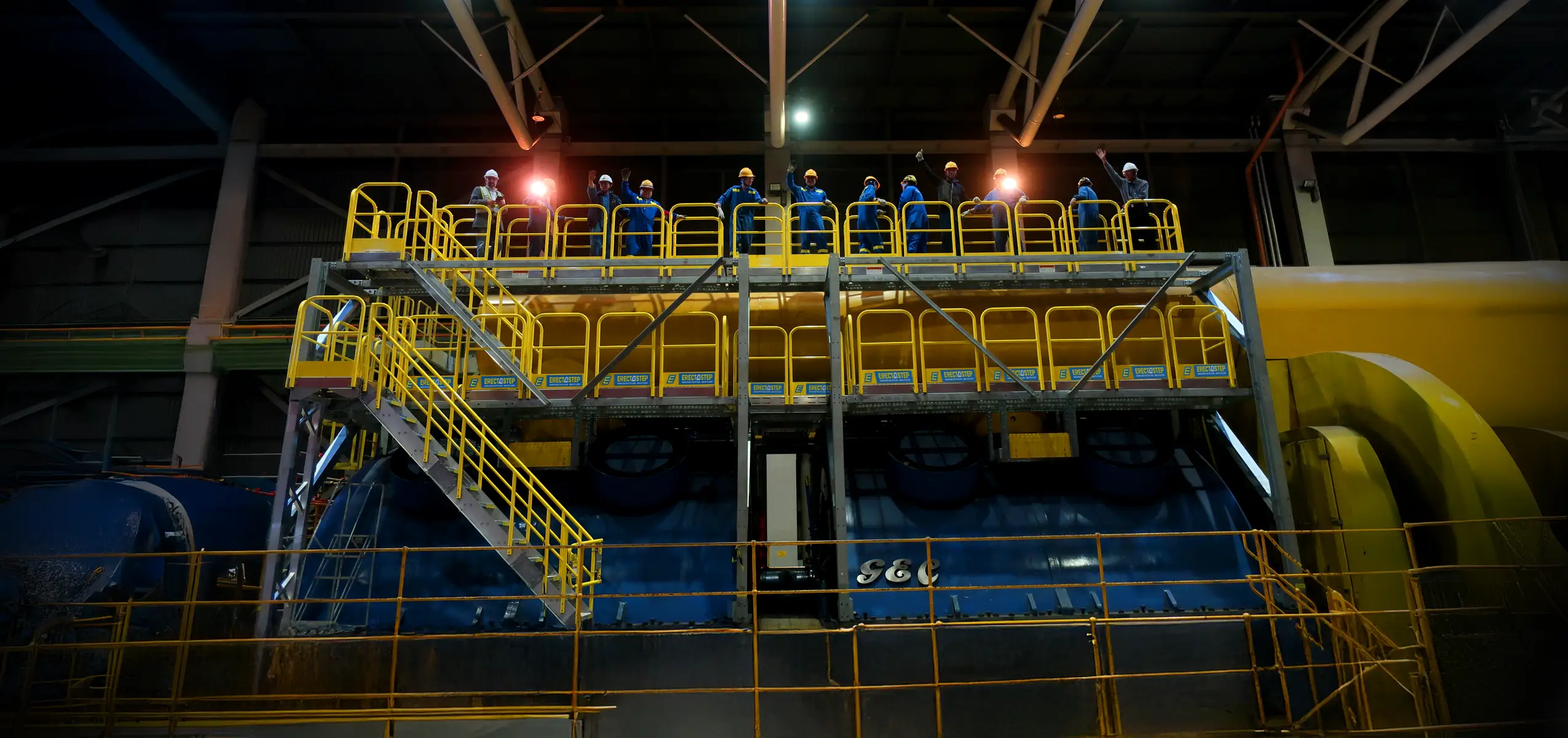
Power Generation
Safe and Efficient Access Solutions for Power Generation Facilities
Safe, Reliable Access Solutions for Power Generation Facilities
SafeRack provides OSHA-compliant platforms, stairs, and safety equipment designed to protect workers and improve accessibility in power plants, substations, and generator facilities.
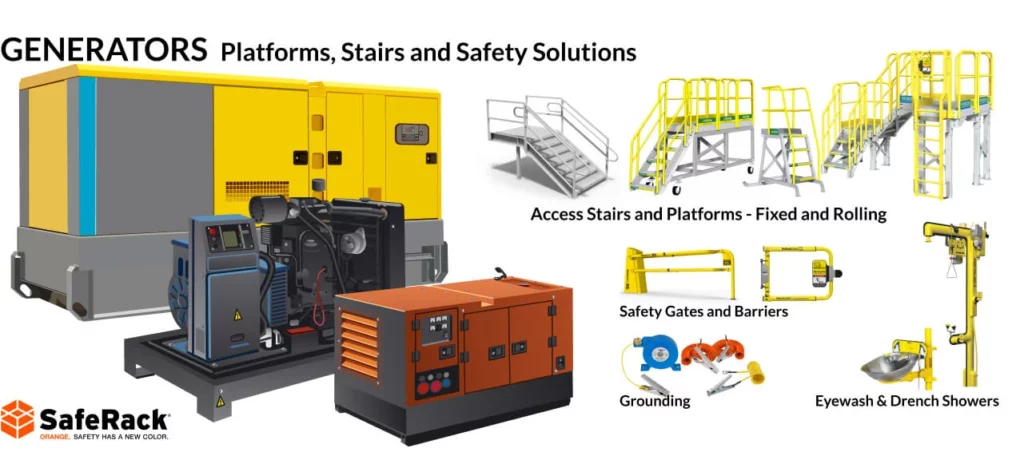
- Safe Access & Fall Protection – Modular platforms, crossover stairs, and guardrails improve worker safety in high-risk areas, including elevated generator platform access points.
- Regulatory Compliance – OSHA-compliant solutions help power plants meet industry safety standards and reduce liability through proper generator maintenance safety equipment.
- Durable, Low-Maintenance Equipment – Corrosion-resistant materials withstand extreme temperatures, chemicals, and heavy industrial use—ideal for generator servicing platforms and heavy-duty generator maintenance solutions.
- Emergency Preparedness – Drench showers, eyewash stations, and grounding systems support workplace safety protocols during generator maintenance or emergency servicing.
- Efficient Equipment Access – Work platforms, generator access platforms for maintenance, and mobile stairs provide secure access for servicing turbines, electrical systems, and generators.
- Expert Consultation & Support – On-site evaluations ensure facilities receive the right safety and access solutions, from routine maintenance for power plant generators to full generator platform design and installation.
Power Generation
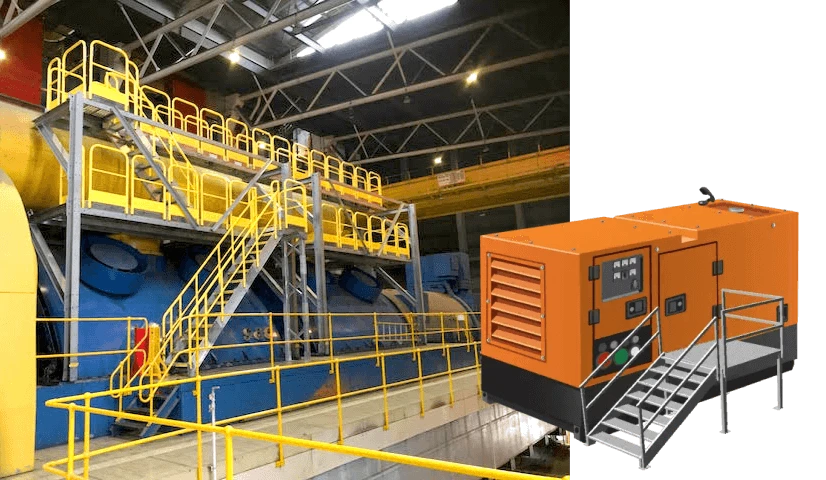
Comprehensive Solutions for Power Generation Projects
SafeRack offers a range of prefabricated generator platforms and access solutions suitable for power generation projects of all sizes. From elevated generator platforms for large industrial turbines to portable generator platforms for smaller commercial backup units, our designs facilitate quick assembly—often requiring just a few hours and basic tools like a wrench. For more complex or customized requirements, our team of experts collaborates with you to develop tailored solutions. Utilizing our state-of-the-art configurator tool, we provide accurate quotes and detailed custom drawings within minutes, streamlining your project planning process.
Generator Maintenance Access
Generators can deliver years of reliable service when maintained regularly. Adhering to a structured maintenance schedule is crucial for ensuring operational efficiency and longevity. Key maintenance tasks include:
- Air filter inspection
- Oil change
- Fuel level check
- Cooling system check
- Belt inspection
- Battery check
- Replacement of worn parts
Products
Industrial Metal Stairs
Prefabricated industrial metal stairs and access platforms offer safe, durable, and expandable access with quick, no-fabrication installation.
Loading Dock Stairs
Prefabricated IBC, ADA, or OSHA Aluminum Loading Dock Steps that bolt together in about an hour.
Portable Access Platforms
SafeRack’s MAUI mobile access units provide secure, adjustable stair solutions for safely accessing elevated truck and railcar work areas, even in the most challenging environments.
Rolling Ladder
The Tilt and Roll Rolling Ladders are designed with ample room to complete any task efficiently.
Barrier Gates
YellowGates XL barrier gate provides 6 feet of adjustability protects every pathway in your facility
Safety Swing Gates
YellowGate – The Original Universal Self Closing Safety Gate
Drench Showers
Emergency Drench Showers and Safety Eyewash Stations
Grounding/Earthing
Protect personnel, product, and terminals with static grounding (earthing)
Project Profiles
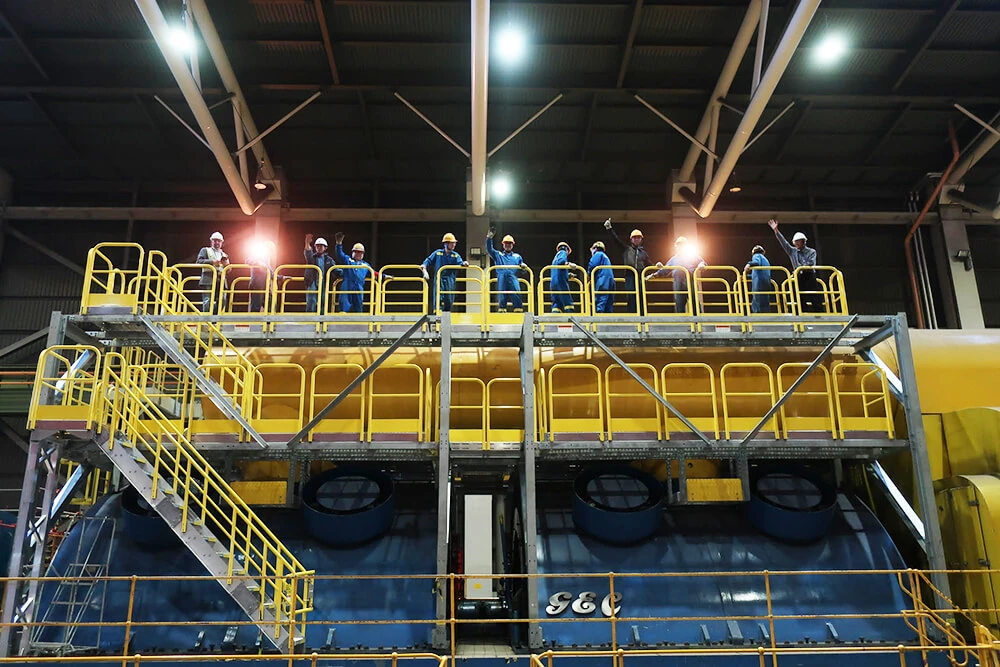
INSTALLATIONS
Projects
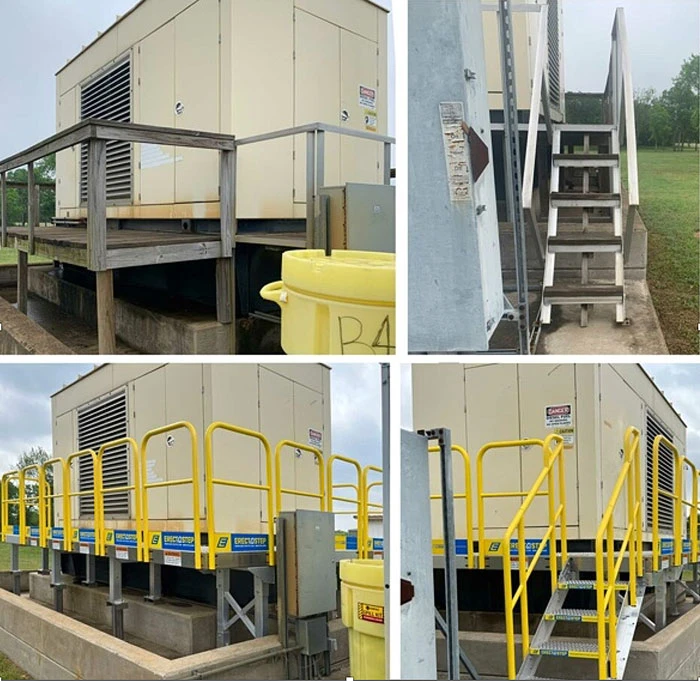
Case Study
Elevated Generator Platform
- The solution provided needed to be able to support the weight of the generators, as well as withstand winds and other weather conditions.
- Customer’s diesel generator had a wood generator platform that didn’t meet OSHA regulations
- Using in-stock ErectaStep components, the wood platform was replaced with minimal delivery and installation time.
- This generator platform bolted together and didn’t require special tools, equipment, or welding.
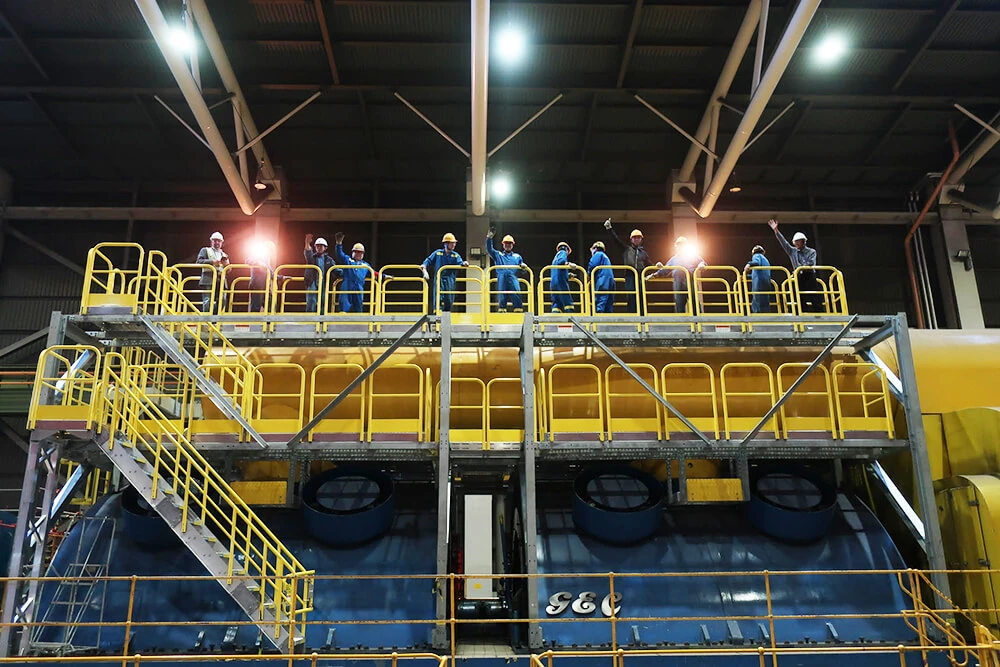
Case Study
Turbine Generator Platform in China
- Client in China wanted to replace the long-term use of scaffolding with a permanent, OSHA-compliant solution for safe access to their GEC Turbines
- They were looking to reduce the cost of renting scaffolding
- SafeRack was chosen, and the client was delighted with the outcome – Safety and productivity working in harmony
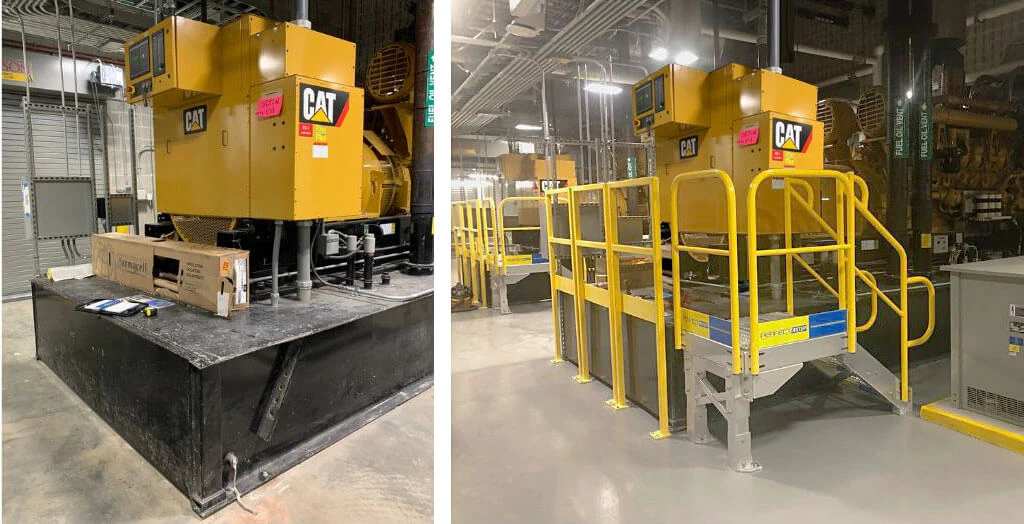
Case Study
Access platform and fall protection for several interior generators
- Generators were at height, and while accessible, maintaining them was dangerous and not OSHA compliant. Installing ErectaStep platforms, steps, and rails… increasing efficiency, and safety… and is now OSHA compliant.
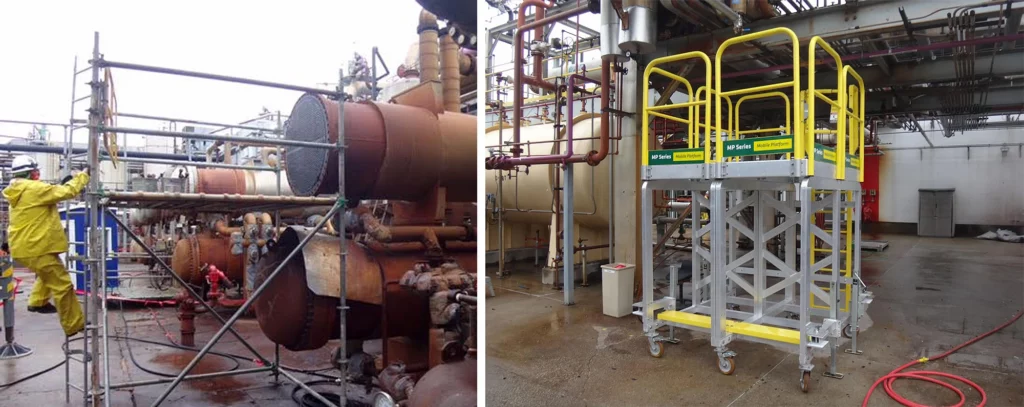
Case Study
Rolling platform to replace scaffolding
- A large tire manufacturing plant had to regularly access its heat exchangers. Every 4-6 weeks scaffolding was used to access these heat exchangers for maintenance.
Safe Alternatives to Scaffolding
There are safe alternatives to scaffolding that are automatically OSHA compliant. Modern modular work platforms are constructed to exact standards that give users immediate OSHA compliance. Modular systems are designed to give workers superb fall protection, stable workspaces, and ease of construction. Mobile work platforms and fixed work platforms are perfect for scheduled maintenance projects, manufacturing environments, and production line crossovers.
Scaffolding Rental vs Semi-Permanent ErectaStep Metal Modular Platforms
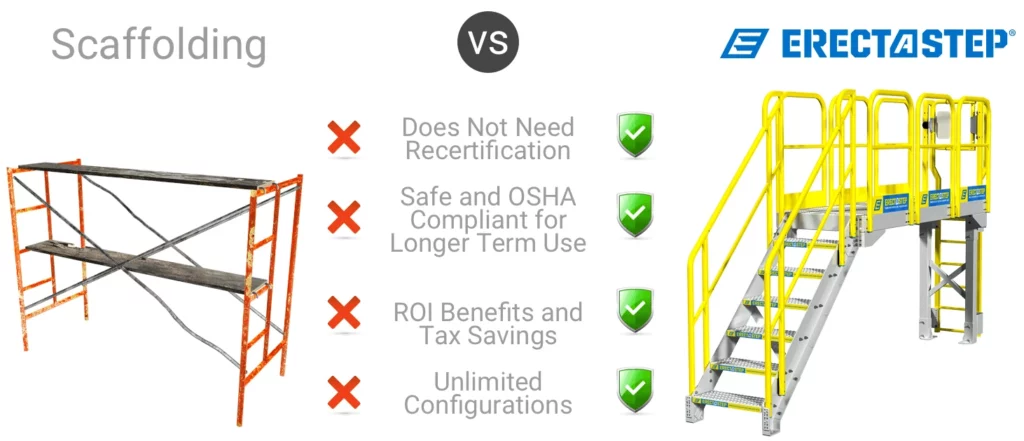
Eliminate Scaffolding Rental Re-certifications
Renting or leasing typical metal scaffolding for semi-permanent or longer-term applications has many disadvantages and some are just downright UNSAFE if not installed correctly. Not the least of which is that scaffolding must be reinspected and re-certified on a regular basis. Sometimes creating timely delays and costly fines if not performed on time.
Fast Scaffolding Replacement
ErectaStep and RollaStep solutions can serve as an even better alternative to all types of semi-permanent to permanent scaffolding. When comparing the two types of access platforms – rental versus SafeRack variants – it is SafeRack’s solutions that can be more effective in many industrial, plant or warehouse uses.
The Hazards and Downfalls of Scaffolding
- More prone to corrosion, rust, and decay
- Cannot easily reach areas without having multiple support columns
- Fastener joints can easily loosen or break
- Large and unsafe gaps in handrails
- Many components and pieces needed to build even a simple platform
Generator Maintenance
Performing regular maintenance will ensure your industrial generator will operate reliably, helping your business avoid the financial losses associated with a shutdown. Now to the tactical application on “how”. That’s going to entirely depend on the manufacturer. Generators can give years of reliable service, but that’s typically only possible with the proper maintenance. The following items are things that need to be checked at least annually.
Air Filter Inspection
Air Filters can get dirty. Really dirty. When the filter is loaded with dirt, dust, and other small particulates, it can cause significant damage to the engine. These should be inspected and cleaned regularly. If they are still fouled after cleaning, just replace them. You don’t need the engine gasping for air when it’s running.
Oil Change
If you’ve ever owned anything with an engine, you know how critical this is. Just like a car, a generator engine requires oil, and oil breaks down over time. Regular oil changes are absolutely necessary for the health of your generator engine and should be included in any maintenance plan.
Fuel Level Check
Make sure that you’re using high-quality fuel and make sure you don’t run it down to empty. The bottom of the fuel tank can have water and sediment that will end up being run through the filter which can clog the fuel filter. This could result in unfiltered debris damaging your engine, so try not to run it empty, and make sure you change the fuel filter if it looks to be clogged.
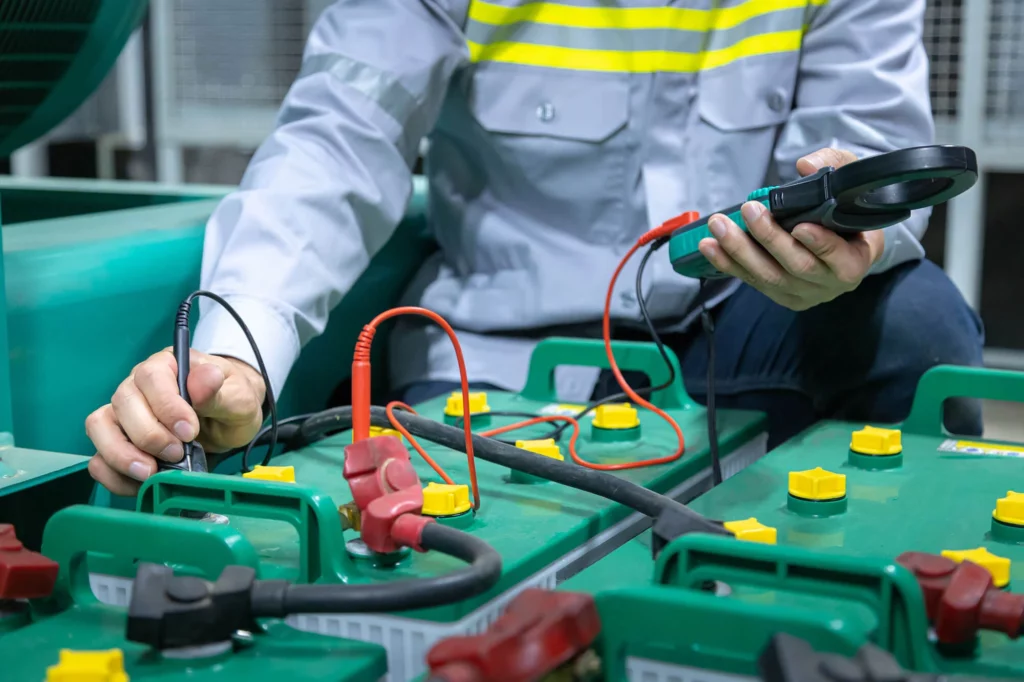
Battery Check
Your battery’s connections should be cleaned and tightened to help prevent battery failure. Also, make sure to run the battery for a few minutes to check its operation. If your generator doesn’t start up, it could be a simple battery malfunction or a larger issue with the system, so you should have a qualified technician look it over to determine the root cause of the power failure.
Cooling System Check
A well-maintained cooling system will help keep your generator engine from overheating, which could damage it beyond repair. Check the coolant level and refill as needed. You’ll also want to flush the cooling system entirely at the manufacturer’s recommendation. This will help maintain coolant quality so that your generator gets the maximum benefit.
Belt Inspection
The belts that run the alternator, fan, and other parts of your engine can start to wear down over time. This can cause them to warp and crack, and could eventually break entirely. You might even notice strange squealing sounds coming from the belts. These are signs that the belts need to be replaced before they wreak havoc.
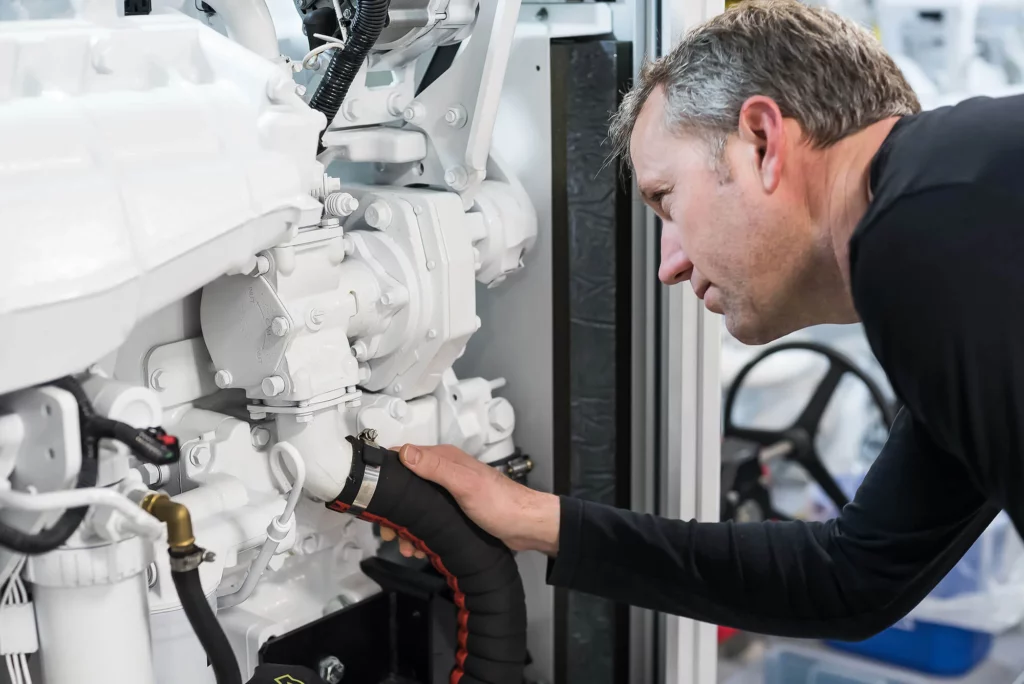
Replacement of Worn Parts
Cracked hoses, corroded connections, and other worn-out parts should be repaired or replaced as soon as possible. Left unaddressed, your generator can become less efficient and experience additional wear and tear, eventually causing a breakdown of your power system.