Bulk Chemical
Protecting Workers and Boosting Throughput with Safe & Efficient Loading Access Solutions
Improving Safety and Efficiency in Bulk Chemical Loading Operations
Ensure your facility meets OSHA, MSHA, ANSI, EPA, and SPCC Standards
Chemical plants, refineries, and bulk transport facilities operate in environments that demand strict safety measures and regulatory compliance. SafeRack provides durable, OSHA-compliant access and fall protection solutions designed to enhance worker safety, streamline loading chemical tanker operations, and maintain operational efficiency. Our expert team works closely with facilities to implement reliable systems tailored to their needs.
Bulk Chemical
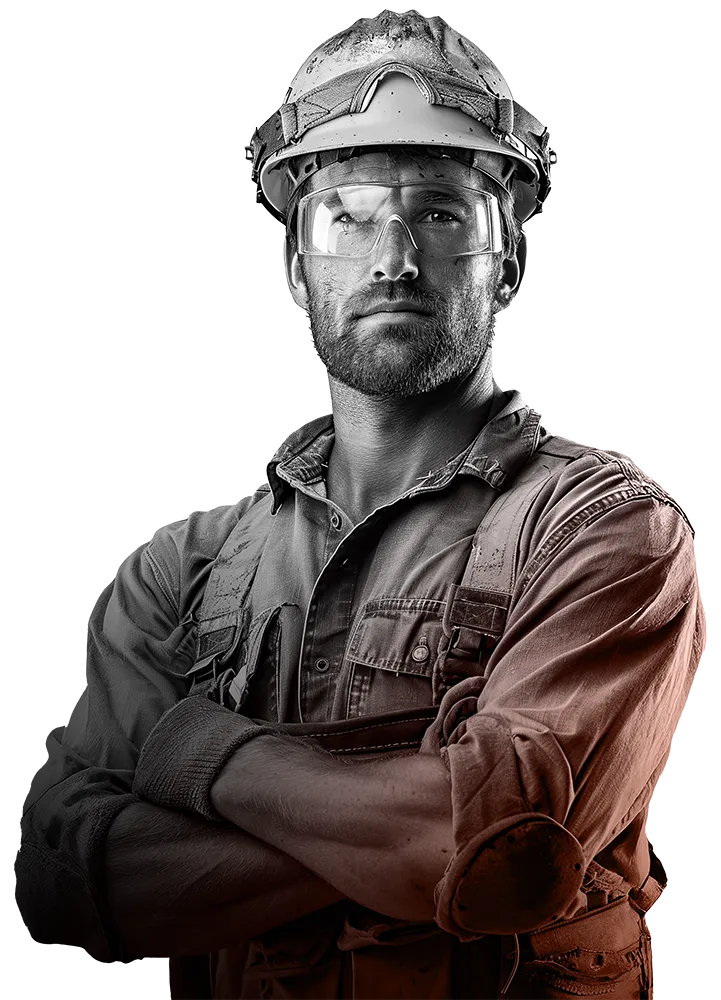
Your Full-Service Partner for
Bulk Loading Terminal Design & Compliance
– More Than Superior Products –
- On-Site Safety Assessments
Complimentary evaluations to identify risks, ensure compliance, and improve workflow efficiency. - Proprietary Configurator
Save time and costs with same-day 3D renderings, loading platform and gangway layout drawings, and budgetary quotes—all with built in compliance and efficiency.
- Compliance and Productivity Optimization
Expert design support to meet safety regulations while streamlining operations and reducing downtime. - Large Project Consultation
Collaboration with your team to design loading platform solutions that meet regulations and facility needs.
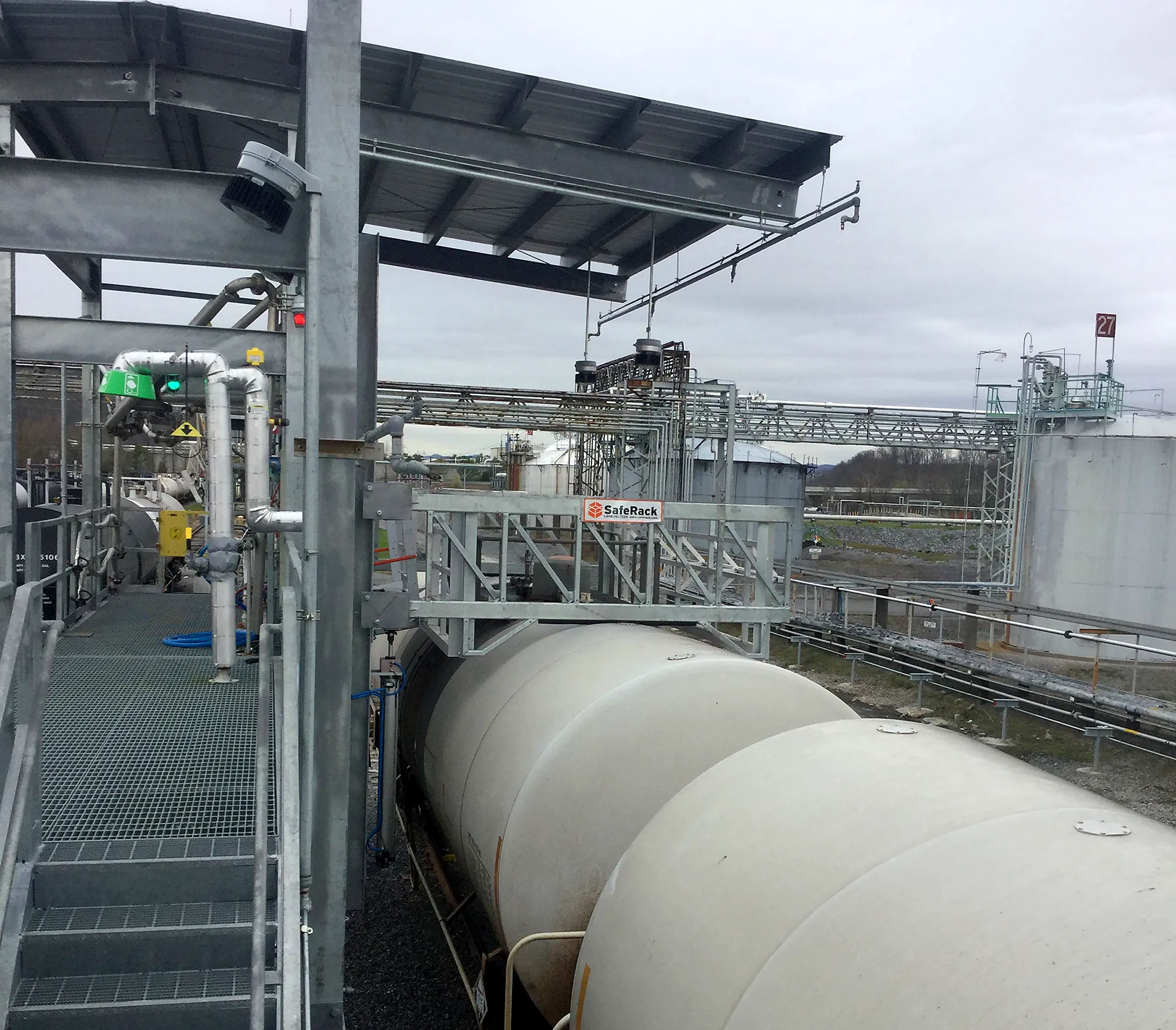
Reliable, Innovative Access Systems Designed for Safety and Efficiency
Beyond providing OSHA-compliant access and fall protection solutions, SafeRack partners with chemical plants, refineries, and bulk transport facilities to enhance safety, compliance, and efficiency at every stage of operations. Our team conducts on-site safety assessments to identify potential risks, ensuring seamless integration of chemical top loading arms, gangways, and platforms into your workflow.
With expertise in regulatory compliance and equipment optimization, we help facilities reduce downtime, improve throughput, and extend the lifespan of critical infrastructure. Whether you’re installing a new chemical loading skid or upgrading an existing system, our solutions ensure safe, efficient, and compliant bulk chemical loading. From project consultation to long-term maintenance support, SafeRack is your full-service partner for chemical handling and transfer operations.
- Fall Hazards: Elevated platforms, tankers, and railcars require reliable fall protection solutions.
- Chemical Handling Risks: Safe transfer systems prevent spills and reduce exposure to hazardous materials.
- Explosion Protection & Static Grounding – Grounding and bonding systems help prevent static discharge and ignition risks in volatile chemical environments.
- Corrosive & Hazardous Material Containment: Secure platforms and spill containment help manage dangerous chemicals.
- Environmental Compliance: Equipment designed to meet EPA, OSHA, and industry-specific safety standards.
- Modular Access & Chemical Loading Solutions – Configurable platforms, gangways, and safety cages provide secure access to tanks, pipelines, and bulk transfer areas.
Truck Loading Platforms
SafeRack’s truck loading platforms provide safe, efficient, and compliant access for bulk loading and unloading operations. Designed to accommodate a wide range of truck configurations, our solutions enhance productivity while reducing risks. With custom-engineered designs, we ensure seamless integration into your existing infrastructure, delivering turnkey platforms that optimize workflow and safety.
Common Configurations
Pedestal Platform
Multi-Hatch Platform
Single Sided
Double Sided
Common Applications
- LPG & Cryogenic Liquid Loading
- Food-Grade and Pharmaceutical Loading
- Petroleum and Fuel Loading
- Bulk Chemical
- Closing/Opening Hatches (Hatching station)
- Asphalt
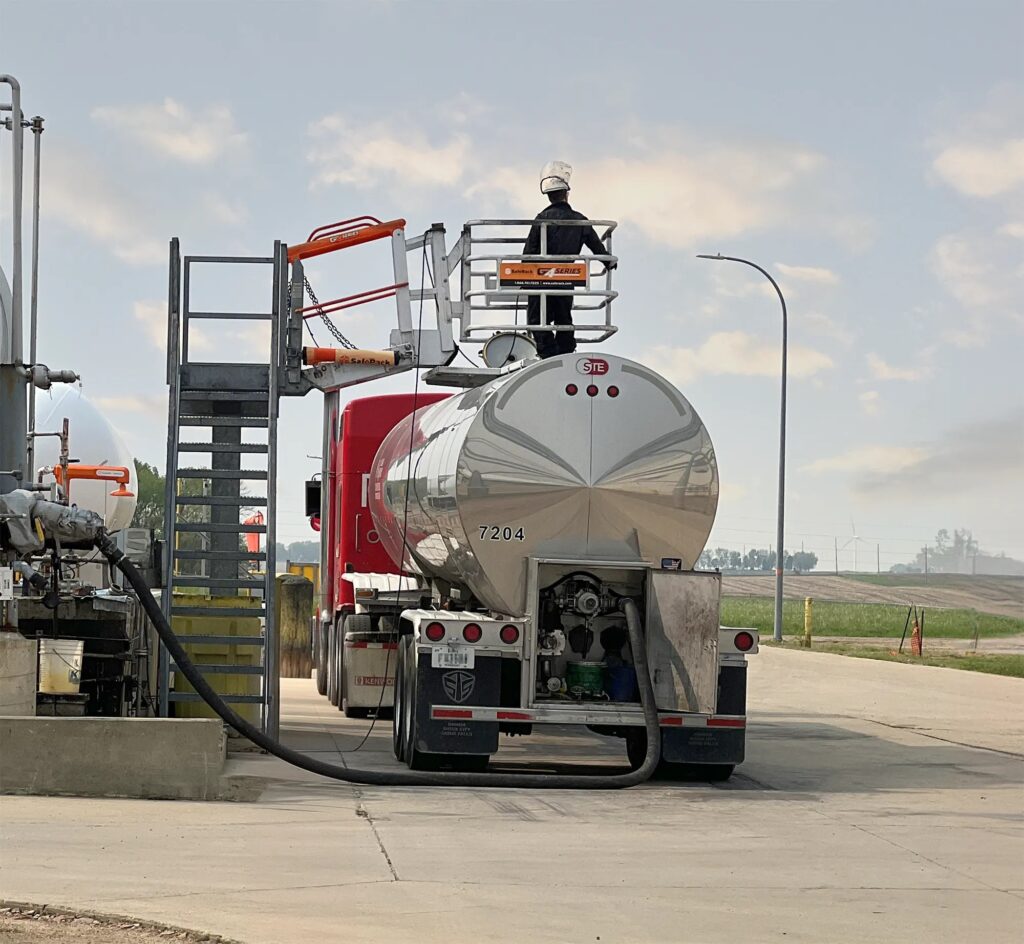
Railcar Loading Platforms
SafeRack’s railcar loading platforms offer secure and flexible access to railcars of any size. Our turnkey systems include loading racks, track-mounted gangways, safety cages, and multi-hatch access platforms, ensuring efficient and OSHA-compliant operations. With decades of experience in railcar fall protection, we design durable systems that streamline loading, protect workers, and keep operations running smoothly.
Common Configurations
Pedestal – Single Spot
Tower Support w/ Canopy – Single Spot
Connected Towers – Two Spot
Long Platform w/ Canopy – Multiple Spots
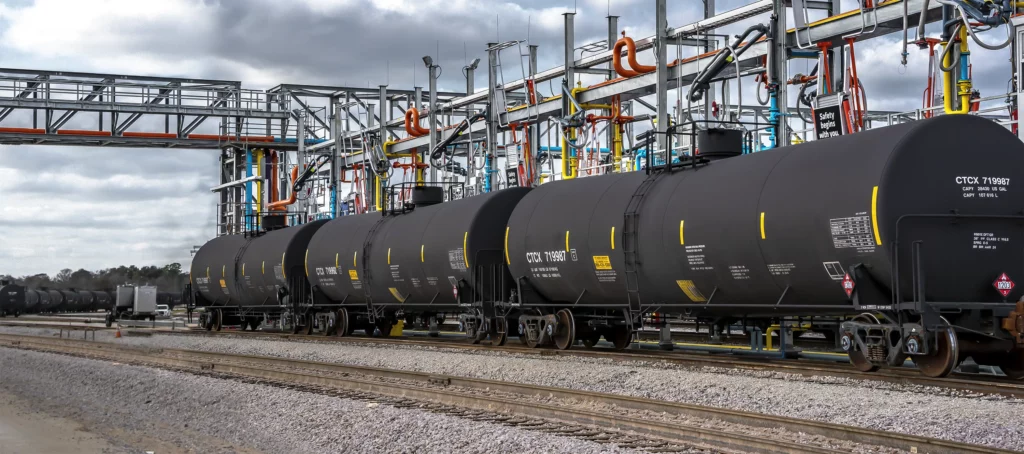
Loading Platform Canopies
Our loading platform canopy systems give you greater flexibility by preventing the environment from stopping the productivity of your project. The heavy-duty systems shield workers and equipment from the environment. Regardless of your application, SafeRack canopy systems provide the cover you need on your railcar loading platform to get the job done right.
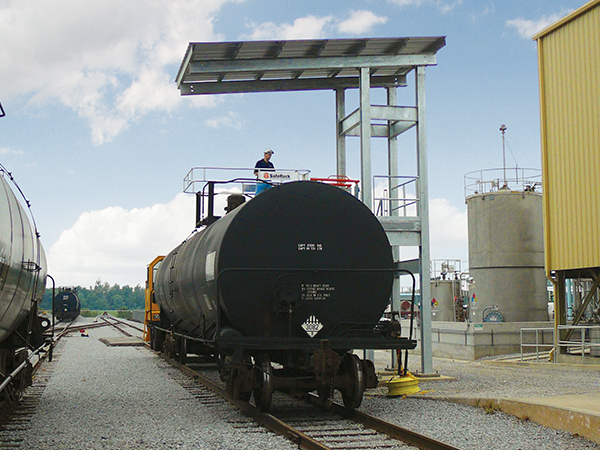
Single Loading Platform Canopy Systems
Whether you utilize a single platform or a long platform, our single canopy systems may be the ideal solution for your specific project. One thing is for certain: our expert engineers and unrivaled customer support team will make sure you get exactly what you need to get your job done.
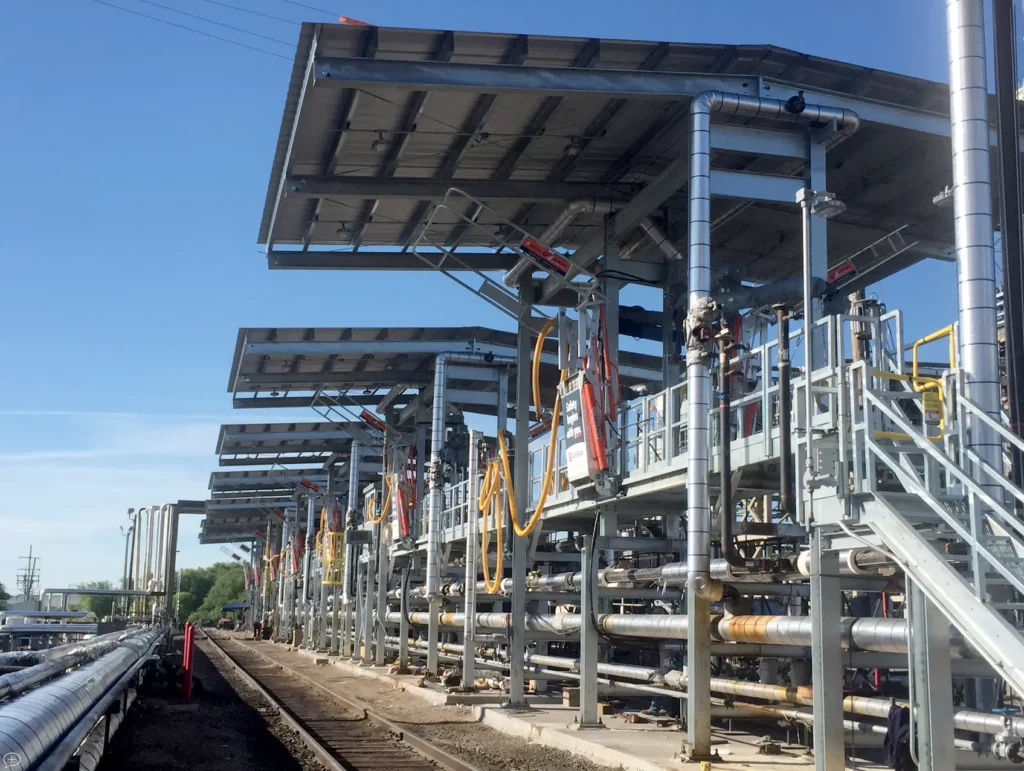
Acetic Acid
Acetic Acid handling design & loading
Acetic Anhydride
Acetic Anhydride handling design & loading
Acetonitrile
Acetonitrile handling design & loading
Acrolein
Acrolein handling design & loading
Acrylic Acid
Acrylic Acid handling design & loading
Acrylonitrile
Acrylonitrile handling design & loading
Aluminum Chloride
Aluminum Chloride handling design & loading
Aluminum Sulfate
Aluminum Sulfate handling design & loading
Ammonia
Ammonia handling design & loading
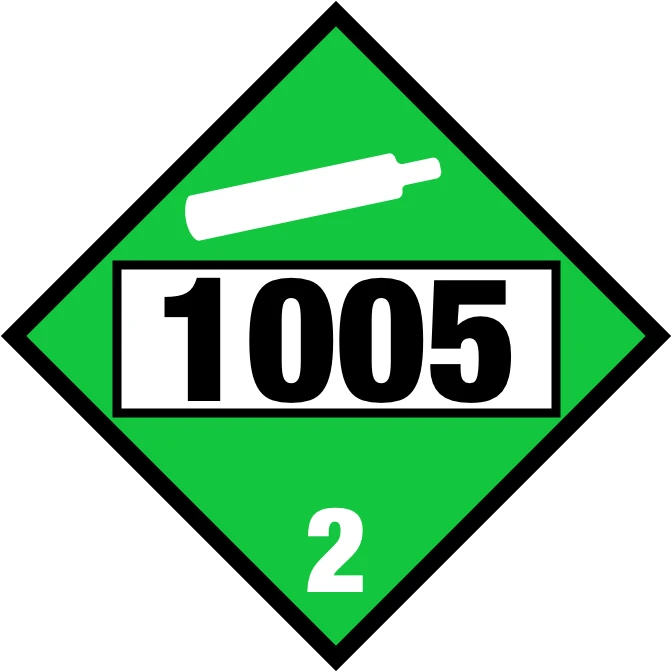
Ammonium Hydroxide
Ammonium Hydroxide handling design & loading
Ammonium Nitrate
Ammonium Nitrate handling design & loading
Aniline
Aniline handling design & loading
Benzene
Benzene handling design & loading
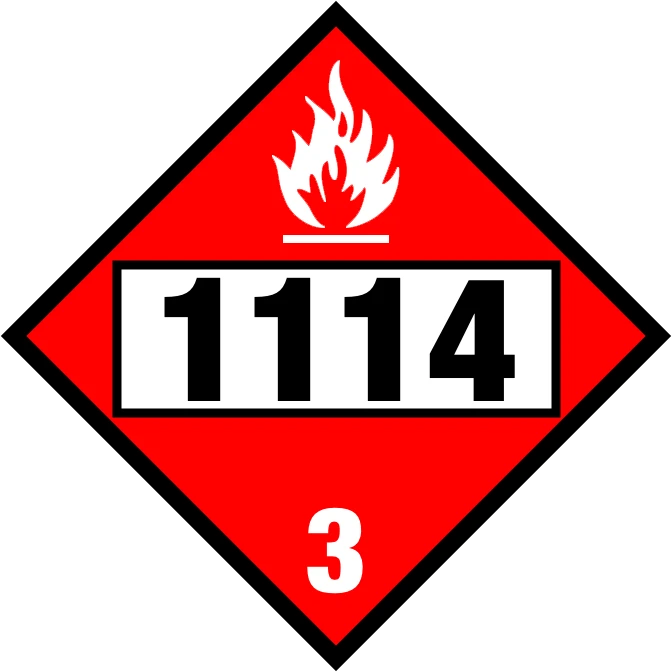
Benzyl Chloride
Benzyl Chloride handling design & loading
Bromotrifluoro methane
Bromotrifluoromethane handling design & loading
Butadiene
Butadiene handling design & loading
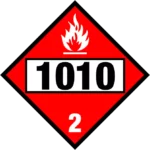
Carbon Dioxide
Carbon Dioxide handling design & loading
Caustic
Caustic handling design & loading
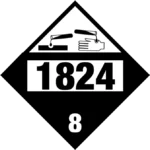
Chlorine
Chlorine handling design & loading
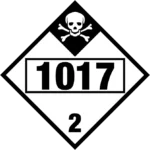
Chloroform
Chloroform handling design & loading
Chlorosulfonic Acid
Chlorosulfonic Acid handling design & loading
DMH
Dimethylformamide handling design & loading
Diethylene Glycol
Diethylene Glycol handling design & loading
Dodecylbenzene Sulfonic Acid
Dodecylbenzene Sulfonic Acid handling design & loading
Ethanol
Ethanol handling design & loading
Ethyl Acetate
Ethyl Acetate handling design & loading
Ethyl Chloride
Ethyl Chloride handling design & loading
Ethylene
Ethylene handling design & loading
Ethylene Dichloride
Ethylene Dichloride handling design & loading
Ethylene Oxide
Ethylene Oxide handling design & loading
Ethylene Glycol
Ethylene Glycol handling design & loading
Ferric Chloride
Ferric Chloride handling design & loading
Ferrous Chloride
Ferrous Chloride handling design & loading
Hexane
Hexane handling design & loading
Hydrochloric Acid
Hydrochloric Acid handling design & loading
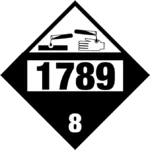
Hydrofluoric Acid
Hydrofluoric Acid handling design & loading
Hydrofluorosilicic Acid
Hydrofluorosilicic Acid handling design & loading
Hydrogen Cyanide
Hydrogen Cyanide handling design & loading
Hydrogen Peroxide
Hydrogen Peroxide handling design & loading
Hydrofluoric Acid
Hydrofluoric Acid handling design & loading
Isopropyl Acetate
Isopropyl Acetate handling design & loading
Liquid Argon
Liquid Argon handling design & loading
Liquid Nitrogen
Liquid Nitrogen handling design & loading
Liquid Oxygen
Liquid Oxygen handling design & loading
Maleic Anhydride
Maleic Anhydride handling design & loading
Methanol
Methanol handling design & loading
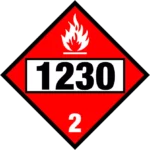
Methyl Chloride
Methyl Chloride handling design & loading
Methyl Isocyanate
Methyl Isocyanate handling design & loading
Methyl Ethyl Ketone
Methyl Ethyl Ketone handling design & loading
Methyl Methacrylate
Methyl Methacrylate handling design & loading
Molten Sulphur
Molten Sulphur handling design & loading
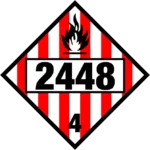
MDI
MDI handling design & loading
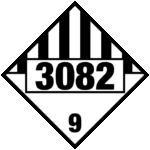
Nitric Acid
Nitric Acid handling design & loading
Oleum
Oleum handling design & loading
Phenol
Phenol handling design & loading
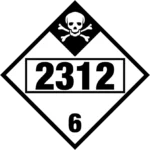
Phosphoric Acid
Phosphoric Acid handling design & loading
Phosphorus Oxychloride
Phosphorus Oxychloride handling design & loading
Phosphorus Trichloride
Phosphorus Trichloride handling design & loading
Polypropylene
Polypropylene handling design & loading
Renewable Diesel
Renewable Diesel handling design & loading
Sodium Cyanide
Sodium Cyanide handling design & loading
Sodium Hypochlorite
Sodium Hypochlorite handling design & loading
Sodium hydroxide
Sodium hydroxide handling design & loading
Styrene Monomer
Styrene Monomer handling design & loading
Sulfuric Acid
Sulfuric Acid handling design & loading
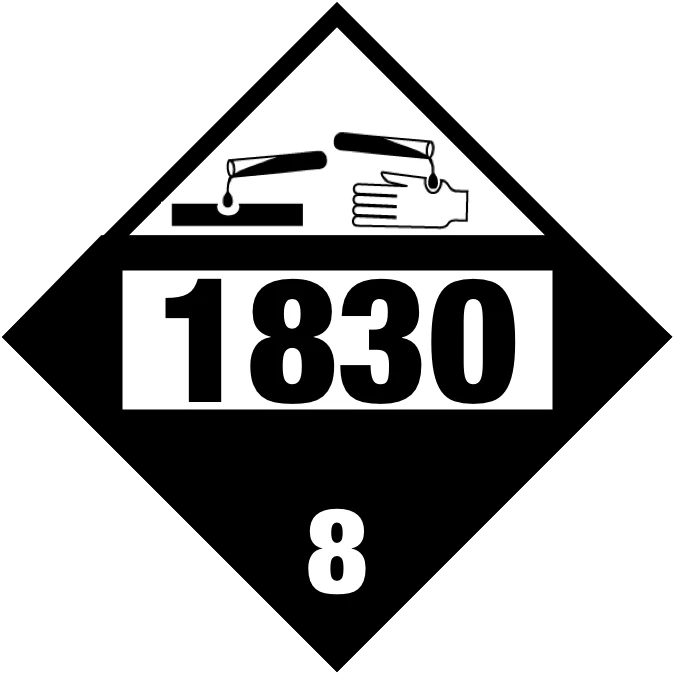
Sulfur Dioxide
Sulfur Dioxide handling design & loading
Titanium Tetrachloride
Titanium Tetrachloride handling design & loading
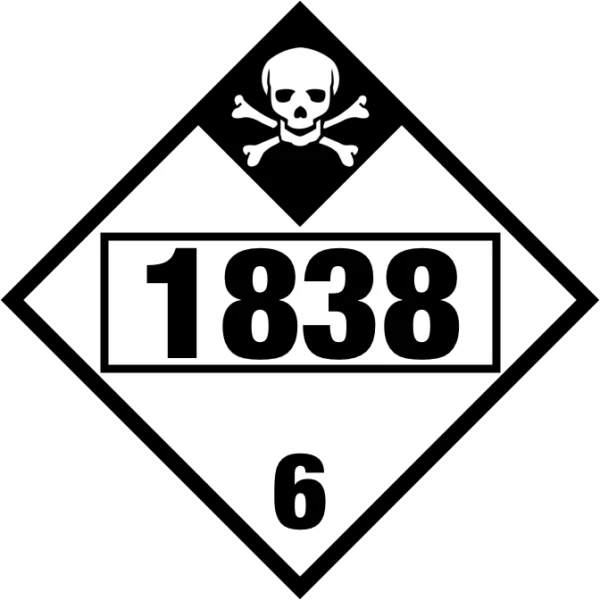
Toluene
Toluene handling design & loading
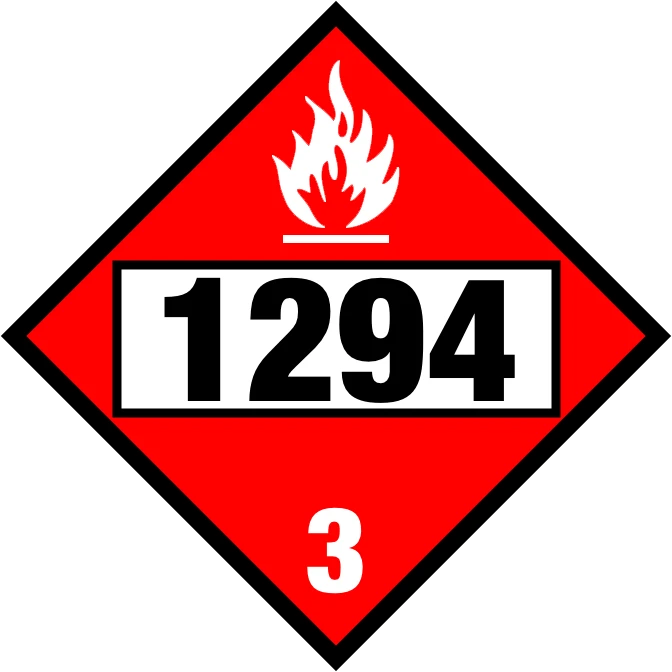
Toluene Diisocyanate
Toluene Diisocyanate handling design & loading
Turpentine
Turpentine handling design & loading
UAN (Urea Ammonium Nitrate)
UAN handling design & loading
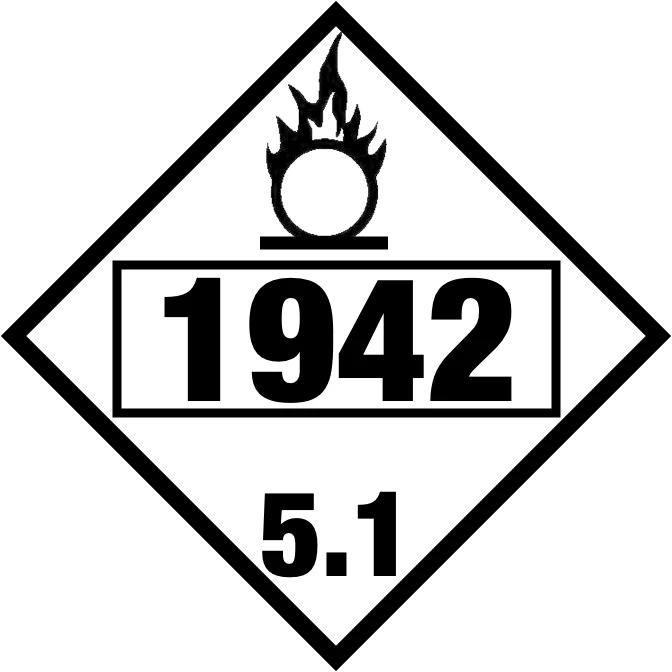
UREA
UREA handling design & loading
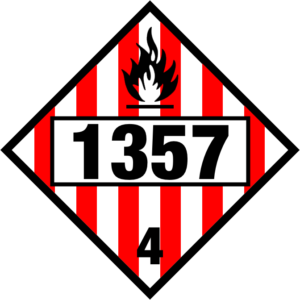
Vinyl Acetate
Vinyl Acetate handling design & loading
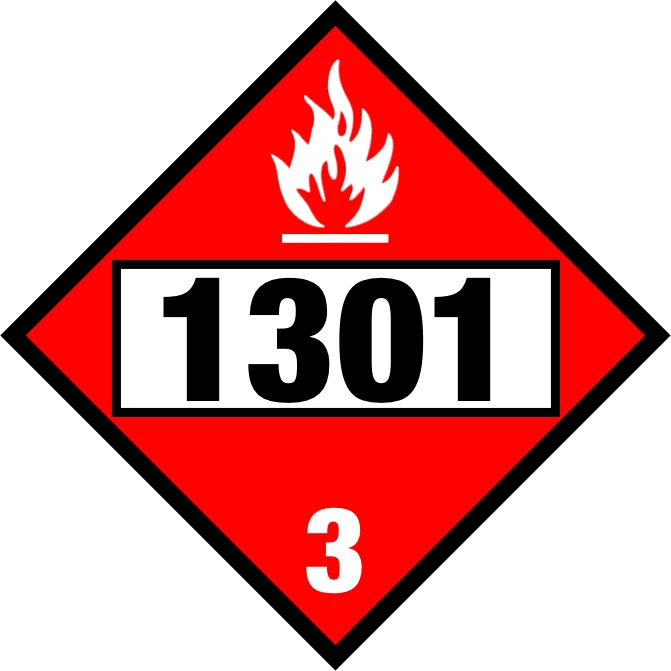
Vinyl Chloride
Vinyl Chloride handling design & loading
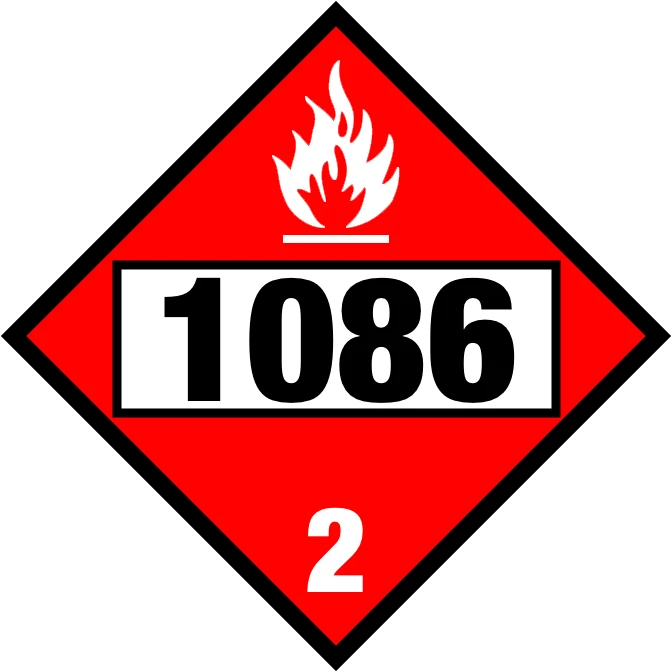
Xylene
Xylene handling design & loading
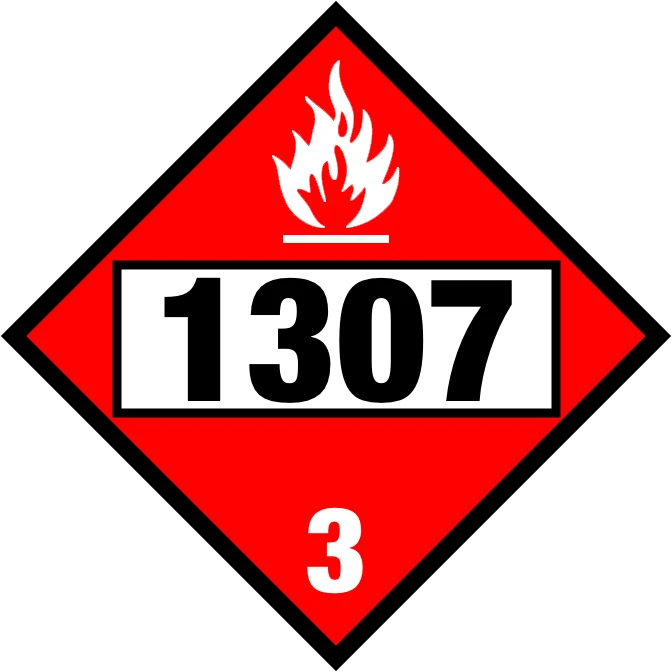
Zinc Chloride
Zinc Chloride handling design & loading
Bulk Chemical Products
Track Mounted Gangways
Gangways that can be horizontally positioned to access top hatches without repositioning the vehicle.
Semi Trailer & Truck Steps
Semi-truck steps for loading semi and flatbed trailers
Samplers and Oil Thieves
Crude oil samplers, including oil thieves and sample catchers.
Barrier Gates
YellowGates XL barrier gate provides 6 feet of adjustability protects every pathway in your facility
Railcar Movers & Brake Sticks
SafeRack’s railcar wheel chocks provide fast blocking of all types of railcars
Safety Swing Gates
YellowGate – The Original Universal Self Closing Safety Gate
Loading Dock Stairs
Prefabricated IBC, ADA, or OSHA Aluminum Loading Dock Steps that bolt together in about an hour.
Skids
Transloading Skids
Mobile Work Platforms
The MP Series is a highly mobile work platform designed to bring the workspace and stability of a fixed platform to a rolling stair mobile unit.
Signs and Signals
Signs and Signals
Railcar Chocks/Blocks
SafeRack’s railcar wheel chocks provide fast blocking of all types of railcars
Lighting
Industrial Lighting Solutions for Hazardous Environments
Drench Showers
Emergency Drench Showers and Safety Eyewash Stations
Pipe Racks
Prefabricated Pipe Racks Constructed Faster and Easier Than Ever Before
Tools and Loading Accessories
A comprehensive range of facility and loading terminal equipment, accessories and safety solutions.
Metering
Pressure Gauges, Meters, Sight-flow indicators
Overfill Protection
Preventing costly spills and ensuring safety during tank loading operations
Grounding/Earthing
Protect personnel, product, and terminals with static grounding (earthing)
Grounding & Monitoring
Protect personnel, product, and terminals with static grounding (earthing) solutions
Beam Trolley & Lifeline
Fall Arrest Systems for Horizontal Mobility at Heights
Safety Gates
Industrial safety swing gates, facility guardrails, mezzanine gates and barriers gates.
Drum & IBC Spill Containment
Interior and exterior SPCC compliant and EPA approved spill pallets
Truck Spill Containment
SPCC & EPA Compliant Truck Spill Containment Solutions
Railcar Track Pans
SPCC & EPA Compliant Track pans for capturing hazardous spills from railroad tankers and railcars
Spill Containment
SPCC and EPA compliant solutions. Railcar track pans, truck spill containment, drum and IBC spill pallets, and industrial containment berms.
Top Loading Arms
Top Loading Arms
Loading Arms & Couplings
Truck, rail, and marine bulk fluid transfer top/bottom loading arms, couplings, swivel joints, hoses, and breakaways.
Safety Cages
Fall prevention enclosures for accessing trucks or railcars.
Portable Access Platforms
SafeRack’s MAUI mobile access units provide secure, adjustable stair solutions for safely accessing elevated truck and railcar work areas, even in the most challenging environments.
Transloaders & Metering Skids
Metering skids configured for a variety of materials, including propane, ethanol, crude oil, aviation fuel, NGL, LPG, and other refined petroleum products.
MaxRack Elevated Platforms
Powered elevating platform system for accessing railcars and trucks
Ship, Fixed and Rolling Ladders
Fixed ladder, steep inclined ship ladders and rolling ladders for areas where standard stair length runs are not feasible.
Crossover Stairs
Crossover Stairs
Industrial Metal Stairs
Prefabricated industrial metal stairs and access platforms offer safe, durable, and expandable access with quick, no-fabrication installation.
Truck & Railcar Gangways
The industry’s safest and most ergonomic gangway for truck and railcar access.
Gangways
Truck, Railcar and Marine Gangways, Safety Cages, and Inspection Services
Stairs & Work Platforms
Fixed and Mobile Access Stairs, Work Platforms, Crossover Stairs, Rolling Stairs & Mobile Platforms, Roof Stairs and Access, Ship Ladder
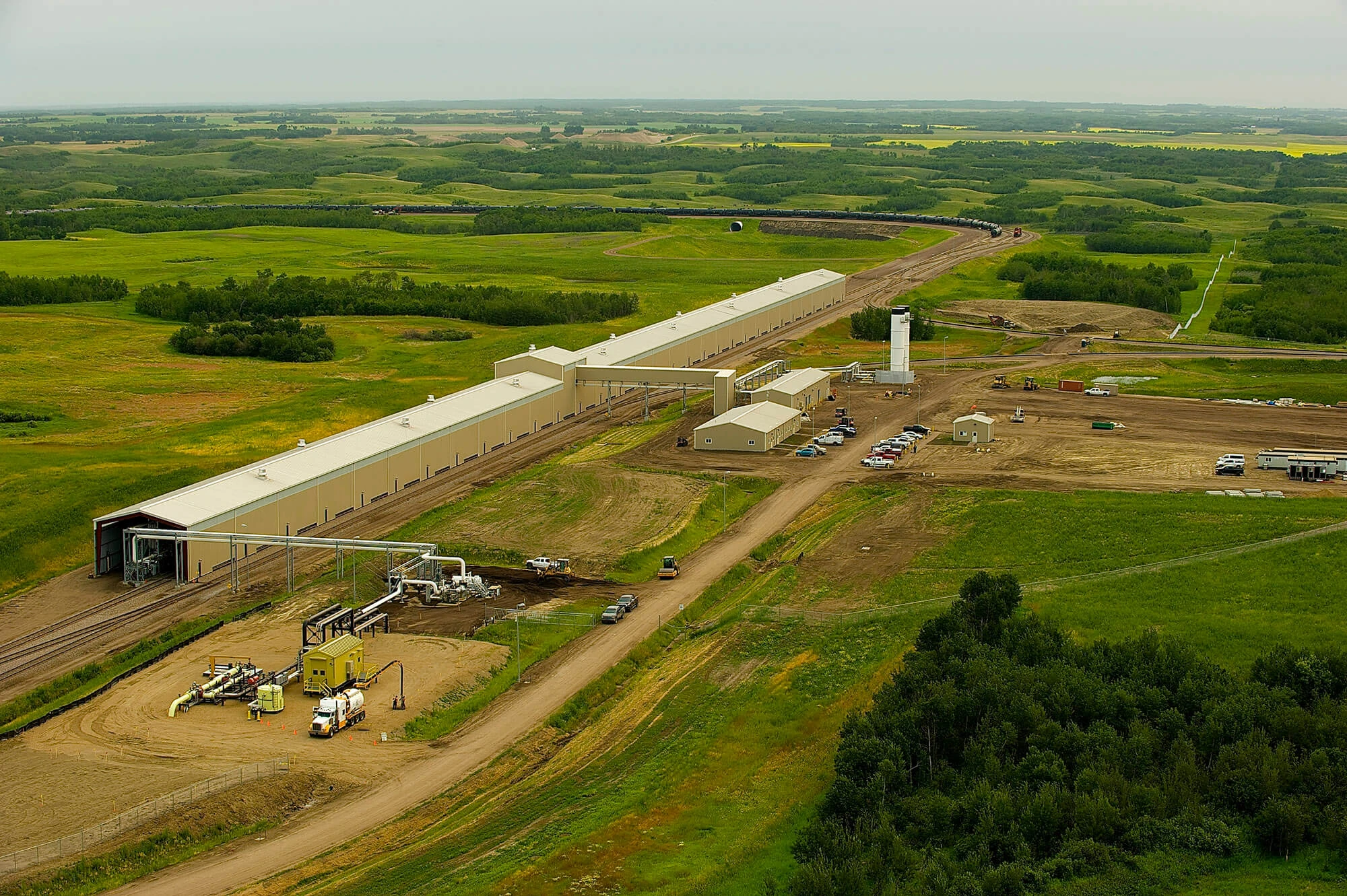
North America’s largest loading terminal
As one of the primary railcar loading points, Hardisty is one of the major crude oil hubs in North America and a major origination point of pipelines that export to the United States. SCS was asked to supply and construct a SafeRack crude oil loadout terminal spanning nearly half a mile. The USD Hardisty terminal can load up to two 120-railcar unit trains per day and consists of a fixed loading rack with 62 railcar loading positions enclosed, separate control, operator, and mechanical buildings, as well as a unit train staging area and loop tracks capable of holding multiple unit trains simultaneously. SCS also supplied and installed boom-supported loading arms with supply and vapor management systems.
Why SafeRack?
SafeRack is more than a supplier—we’re a full-service partner committed to safety, efficiency, and compliance. This approach, The SafeRack Way, goes beyond equipment to include on-site safety assessments, workflow optimization, and seamless integration of systems.
With years of experience in loading chemical tankers, we understand both technical requirements and operator behavior. From project consultation to long-term support, we help facilities reduce risks, improve throughput, and maintain compliance—keeping your operations safe and efficient.
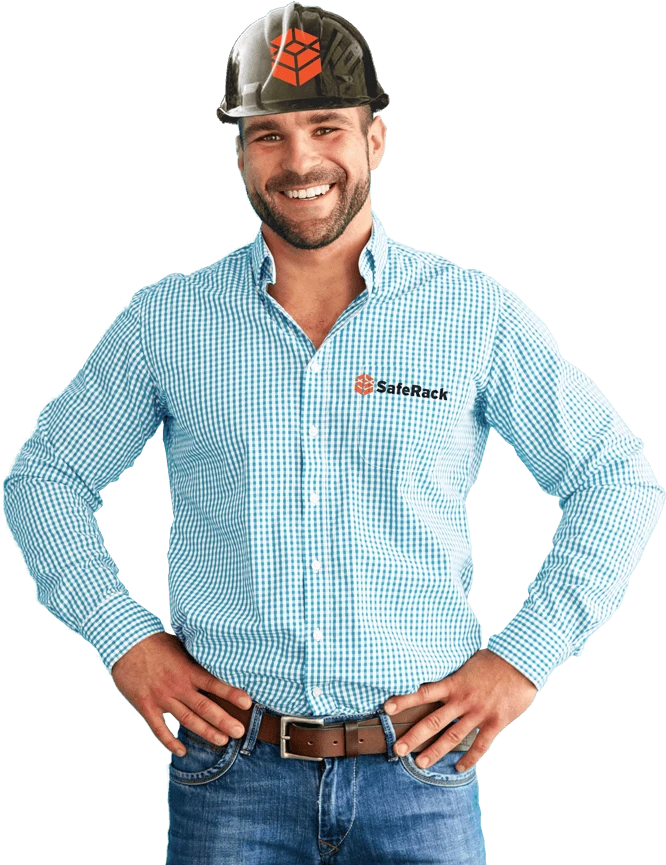
Ensure Your Plant or Facility Stays Compliant with OSHA, MSHA, ANSI, and SPCC Standards — SafeRack Has You Covered!
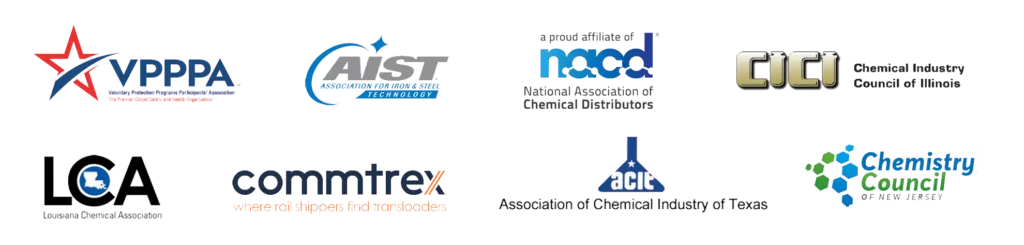
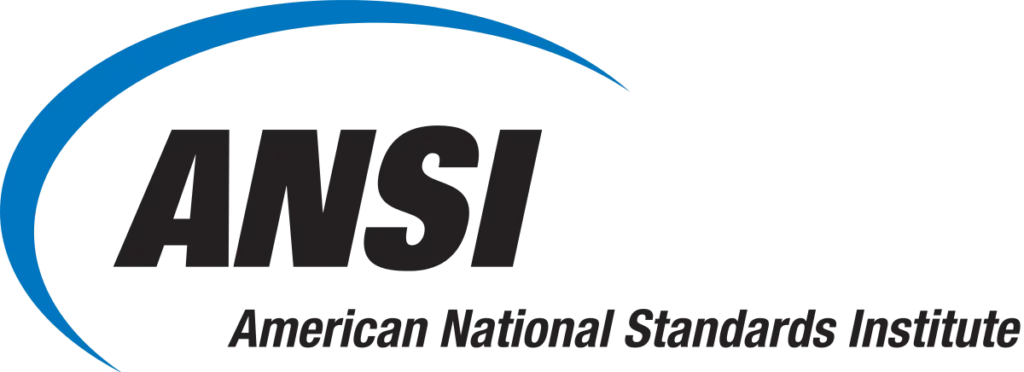
Emergency Eyewash and Safety Showers
Staying Compliant with ANSI/ISEA Z358.1 – 2014
In the event of chemical exposure, immediate access to emergency eyewash stations and safety showers is critical to prevent permanent eye damage or chemical burns.
According to ANSI/ISEA Z358.1 – 2014, eyewash and drench showers must be:
- Located within 10 seconds or 55 feet of hazardous materials
- Positioned on the same horizontal plane with no obstructions
- For bottom loading/unloading operations, an additional shower should be placed at grade level
SafeRack provides ANSI-compliant eyewash stations, drench showers, and additional safety equipment to help facilities maintain compliance and protect workers during bulk chemical loading and unloading operations.
OSHA Compliance Experts
Keeping Your Chemical Loading Systems Up to Standard
Is your chemical safety equipment and loading system fully compliant with the latest OSHA regulations? SafeRack’s experienced technical sales consultants can work directly with your team to evaluate your current setup and recommend solutions that meet or exceed OSHA’s evolving national and regional safety standards.
From lifeline and trolley beam fall arrest systems to metal stairs and access platforms, SafeRack offers comprehensive safety solutions to help your facility stay compliant, efficient and focused on worker protection.
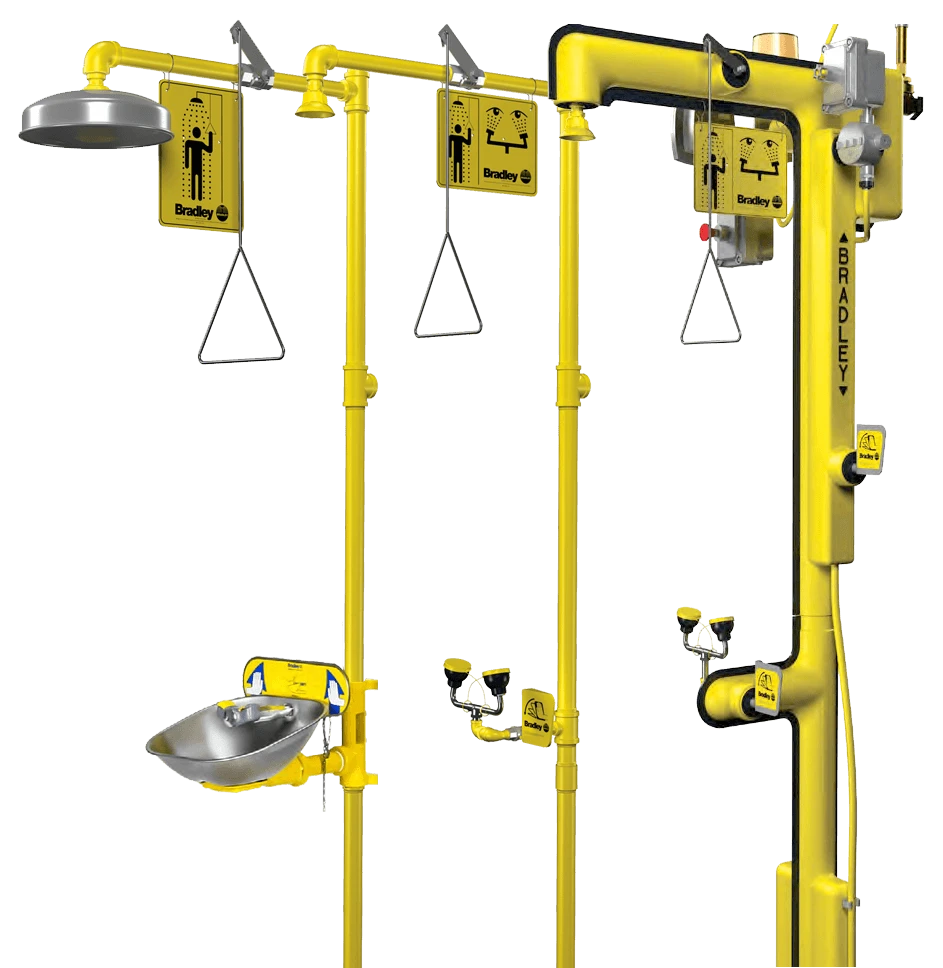